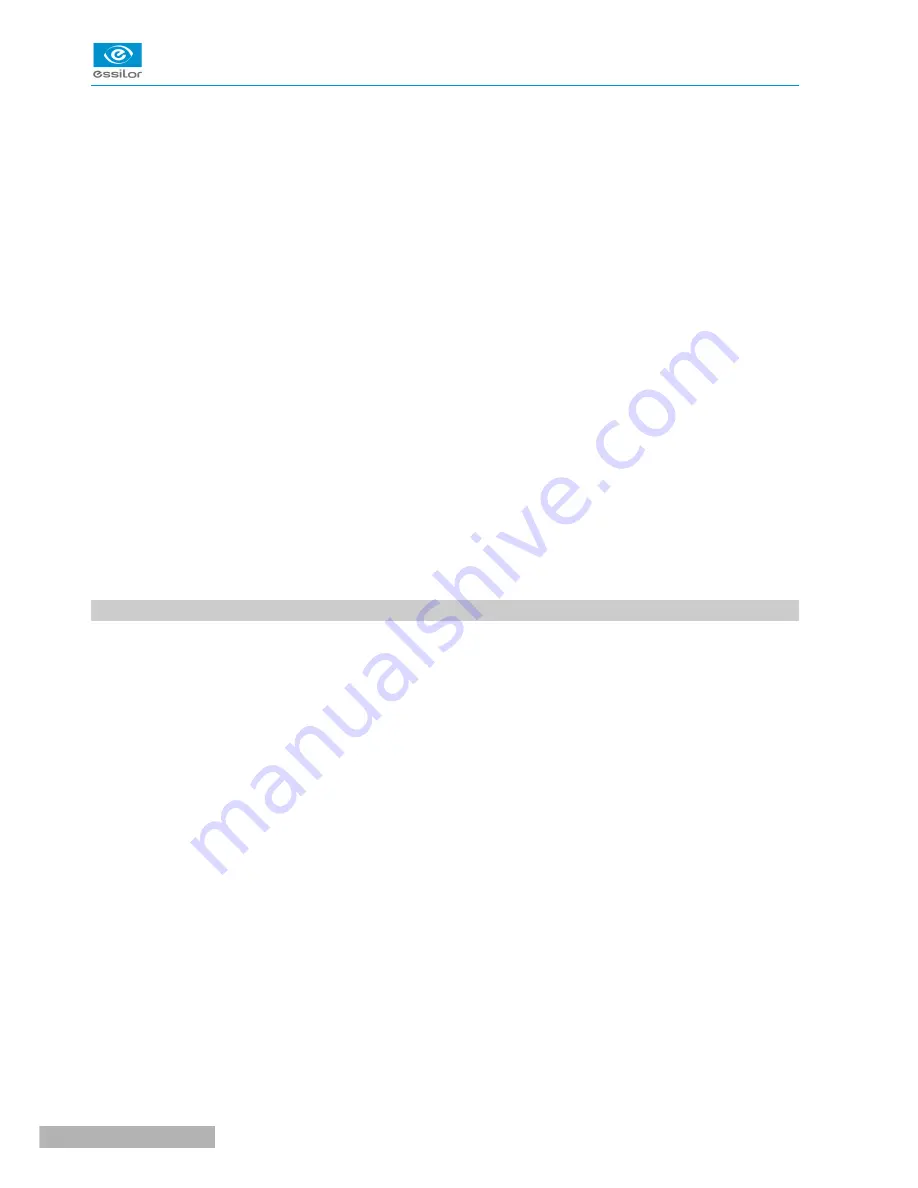
It is an electrical appliance compliant with the applicable safety standards. In the event of malfunction, repairs must be carried out by
qualified personnel approved by Essilor. Otherwise, user safety is likely to be compromised.
In the event of a long period of non-use and before maintenance and/or replacement of certain accessories, you must unplug your edger
from the mains.
The equipment must be plugged into an earthed power supply. The earthing must comply with public standards and be checked by a
technician. Avoid using extension cables or adaptors which could create a poor contact.
Never pull on the cables to unplug them from the power socket.
Before plugging your edger into the mains, check that the switch is set to OFF or 0.
If the switch no longer operates ON/OFF (0/I) you must stop using your edger. Defective switches must be replaced by an approved
repairer.
Your system is a professional tool which must only be used by specialized, responsible operators. It must not be used by anyone apart from
these operators.
This machine is neither adapted nor intended to operate in an environment where there is a risk of explosion. Do not use this system in the
presence of liquids or flammable gases.
Make sure that the equipment is connected to a mains supply which complies with standard NFC 15-100. In addition, make sure that the
plug type is 3-pin 10/16 A (earthed) protected by a high sensitivity differential circuit-breaker, maximum 30 mA, and that the wall outlet is
easy to access.
It is strongly advised to wear gloves to protect your hands when you empty the tank to clean it.
7. E
LECTROMAGNETIC
WAVES
Electromagnetic waves emitted by various equipment (radio and TV receivers, mobile phones, radio transmitters, etc.) are likely to disturb
the operation of the instrument. This instrument is also likely to interfere with this same equipment. Avoid installing or placing devices likely
to generate interference close to the instrument. Likewise, never place the instrument on or near this type of device. The instrument could
be subject to malfunction or breakdown.
Interference and micro-outages
The products have been designed to resist interference and operate despite its presence and the possibility of micro-outages on the
network. However, if these malfunctions are too serious and abnormal, the machine cannot be guaranteed to operate normally.
Neksia > v1.0 - 02.14
80
U
SER
M
ANUAL
> G
ENERAL
INFORMATION
Summary of Contents for Neksia
Page 1: ...User Manual...
Page 2: ......
Page 6: ......
Page 7: ...I FIRST STEPS...
Page 14: ...Neksia v1 0 02 14 14 USER MANUAL I FIRST STEPS...
Page 15: ...II EDGING A LENS...
Page 45: ...USER MANUAL II EDGING A LENS 45 Neksia v1 0 02 14...
Page 46: ......
Page 47: ...III CONFIGURING THE EDGER...
Page 55: ...IV MAINTENANCE SERVICING...
Page 72: ...Neksia v1 0 02 14 72 USER MANUAL IV MAINTENANCE SERVICING...
Page 73: ...TECHNICAL DATA...
Page 76: ...Neksia v1 0 02 14 76 USER MANUAL TECHNICAL DATA...
Page 77: ...GENERAL INFORMATION...
Page 81: ...GLOSSARY...
Page 83: ......