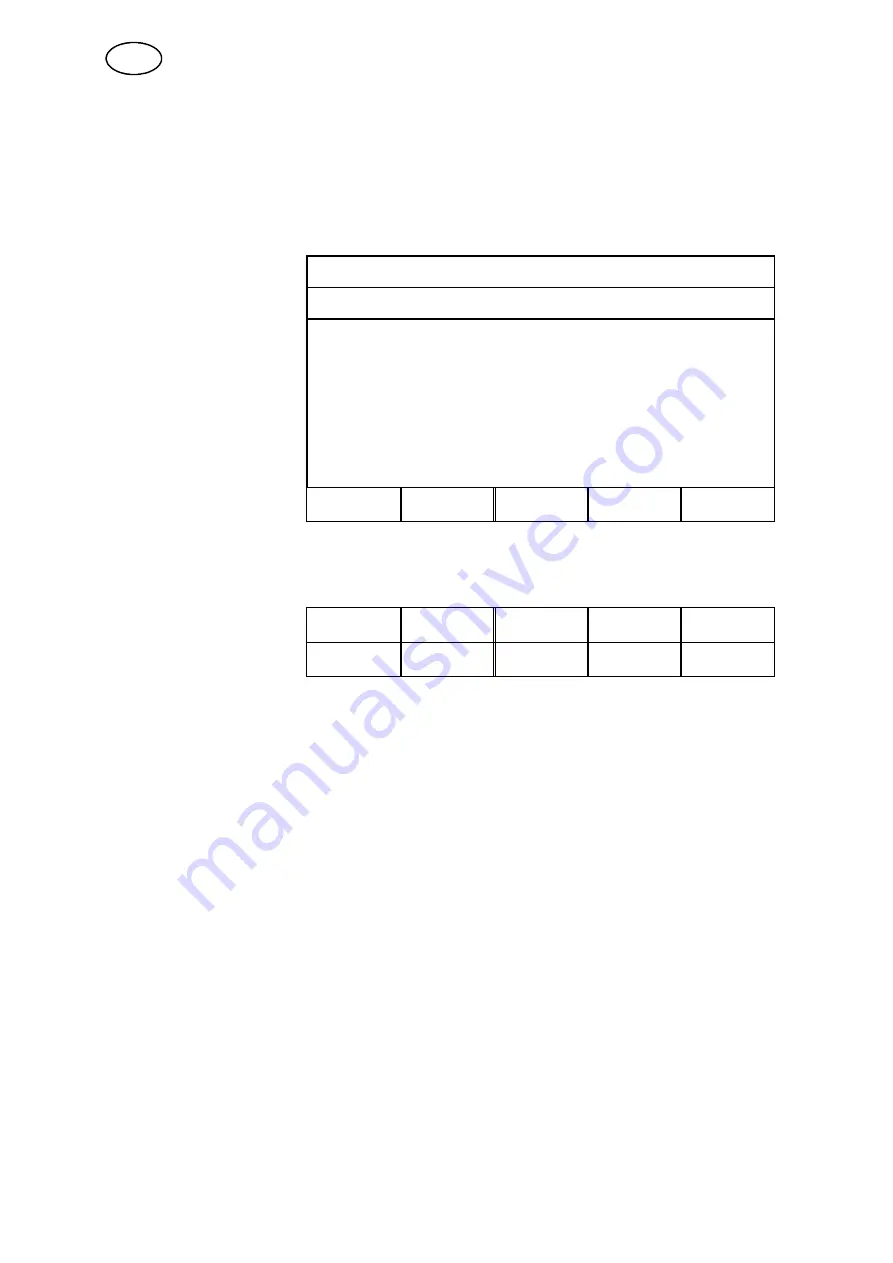
-- 48 --
bi09d1e2
S
Trigg weld data switch ON/OFF
The selection you set for weld data switch before the soft key is activated applies
with weld data switch ON. AT ARC OFF or ON.
Weld data switch is off when weld data switch OFF is selected.
The display image contains two columns: one for
function
and one for
key number
ASSOCIATE FUNCTIONS TO SOFT KEYS
Function
Soft key
NONE
7
GAS PURGE
6
WIRE INCHING
5
TRIGGER MODE (2/4)
3
CRATER FILL ON/OFF
1
CREEP START ON/OFF
4
CRATER
FILL
HOT
START
4--
STROKE
QUIT
2ND
FUNCT
The controller has five soft keys. Pressing the far right key
”2ND FUNCT” accesses an additional five soft keys.
When you assign functions to the keys, these are numbered from the left as follows
1
2
3
QUIT
2ND
FUNCT
4
5
6
7
2ND
•
FUNCT
How to assign a new function to a soft key:
S
Position the cursor on the function row with the function ”NONE” and press the
soft key with the function that is to switch key number,
S
Repeat the above for the key with the key number to be used.
S
Position the cursor on the function row to which you want to give a new key
number and press the soft key to which you want to assign the function.
The other two keys can each have a new function assigned in the same way, by
pairing one of the functions in the left--hand column with a key number in the
right--hand column.
Gas purge
The gas purge function is used when measuring the gas flow or to purge the gas
hoses of any air and moisture before welding commences. Gas purging proceeds as
long as the key is pressed down, and is conducted without voltage and wire feed
being switched on.
Cold wire feed (wire inching)
Cold wire feed is used when you want to feed the wire without switching on the
welding voltage. The wire is fed at the set wire feed speed as long as the button is
pressed down.
GB