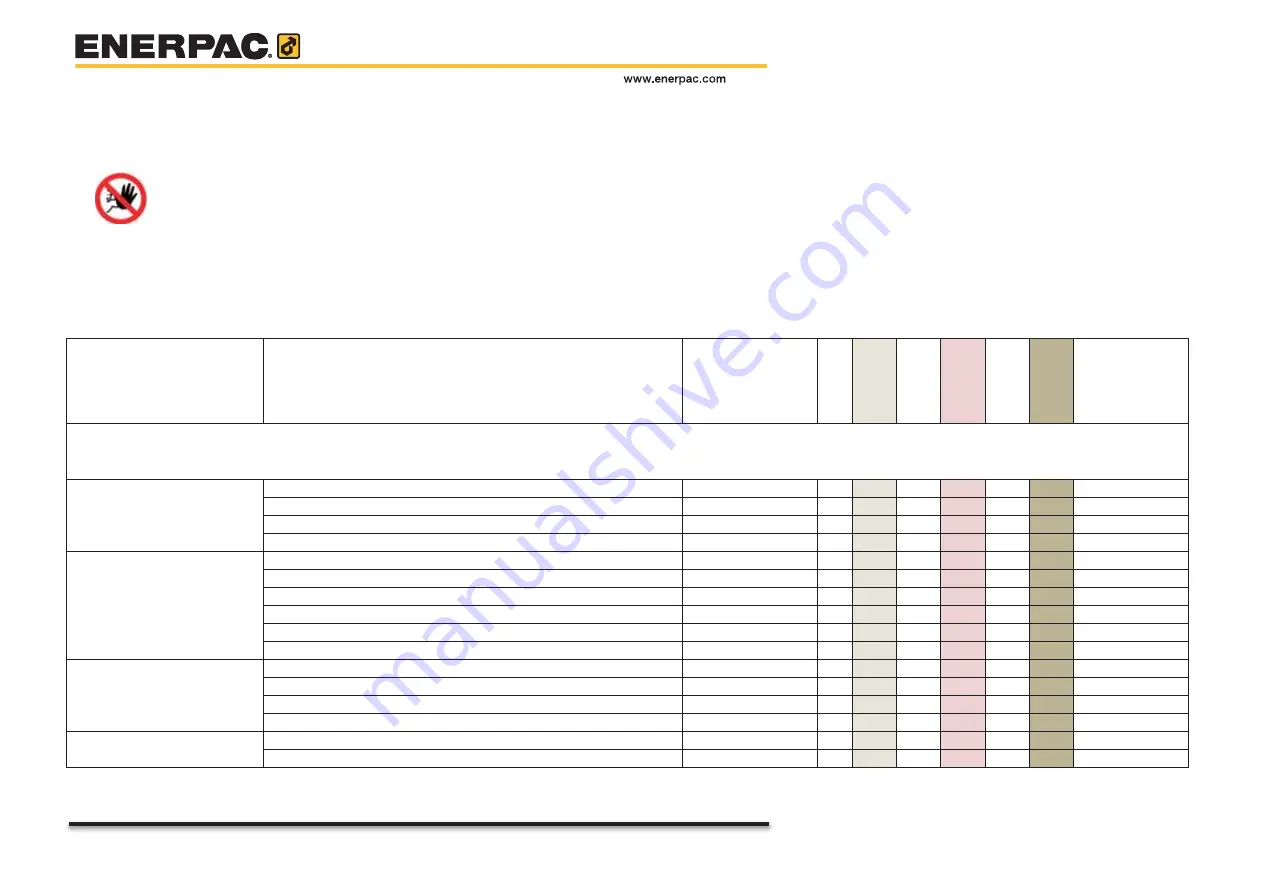
Document number: ED. 03622.00.001.R04.ENG
Page 113 of 151
ED.02518.00.001.R08.ENG
Page 113
)
Enerpac strongly advises to apply parts as bought from Enerpac.
Hazard
Applying parts which to not apply to the specifications may cause
hazards to
personnel
and the system
Perform maintenance on the mechanical part according to the list as shown below.
Record all activities in Appendix E
“
Recording maintenance
”.
For hydraulic fluid safety information sheet, see Appendix J
“
Hydraulic fluid safety information
”.
Subject
Action
Person
O (Owner)
EE (Enerpac expert)
First
40 hours
8 hours
Daily
40 hours
Weekl
y
500 ho
urs
yearly
2000 h
o
urs
2 years
10000
hours
10 ye
ars
Remarks
1. Electro motor, tank and cooler
1.1. Motor
Check on oil leakage, damages and paint work
O
x
Check if the bolts are still tightened
O
x
x
Check on damages
x
Wipe it clean and free from dust
x
1.2. Hydraulic tank
Check on oil leakage, damages and paint work
O
x
Check if the bolts are still tightened
O
x
x
Replace all seals
EE
x
Replace the level gauges
EE
x
Drain the tank (water and sludge)
EE
x
Exchange the filler cap (which contains a filter)
O
x
x
1.3. Valves
Check on oil leakage and damages
O
x
Check if the bolts are still tightened
O
x
x
Replace all seals
EE
x
Check all valve settings
O
x
1.4. Manifolds
Check on oil leakage and damages
O
x
Check if the bolts are still tightened
O
x
Summary of Contents for SBL1100
Page 134: ...Document number ED 03622 00 001 R04 ENG Page 134 of 151 ED 02518 00 001 R08 ENG Page 134 ...
Page 136: ...Document number ED 03622 00 001 R04 ENG Page 136 of 151 ED 02518 00 001 R08 ENG Page 136 ...
Page 138: ...Document number ED 03622 00 001 R04 ENG Page 138 of 151 ED 02518 00 001 R08 ENG Page 138 ...
Page 141: ...Document number ED 03622 00 001 R04 ENG Page 141 of 151 ED 02518 00 001 R08 ENG Page 141 ...
Page 142: ...Document number ED 03622 00 001 R04 ENG Page 142 of 151 ED 02518 00 001 R08 ENG Page 142 ...
Page 143: ...Document number ED 03622 00 001 R04 ENG Page 143 of 151 ED 02518 00 001 R08 ENG Page 143 ...
Page 145: ...Document number ED 03622 00 001 R04 ENG Page 145 of 151 ED 02518 00 001 R08 ENG Page 145 ...
Page 146: ...Document number ED 03622 00 001 R04 ENG Page 146 of 151 ED 02518 00 001 R08 ENG Page 146 ...
Page 147: ...Document number ED 03622 00 001 R04 ENG Page 147 of 151 ED 02518 00 001 R08 ENG Page 147 ...
Page 148: ...Document number ED 03622 00 001 R04 ENG Page 148 of 151 ED 02518 00 001 R08 ENG Page 148 ...
Page 149: ...Document number ED 03622 00 001 R04 ENG Page 149 of 151 ED 02518 00 001 R08 ENG Page 149 ...