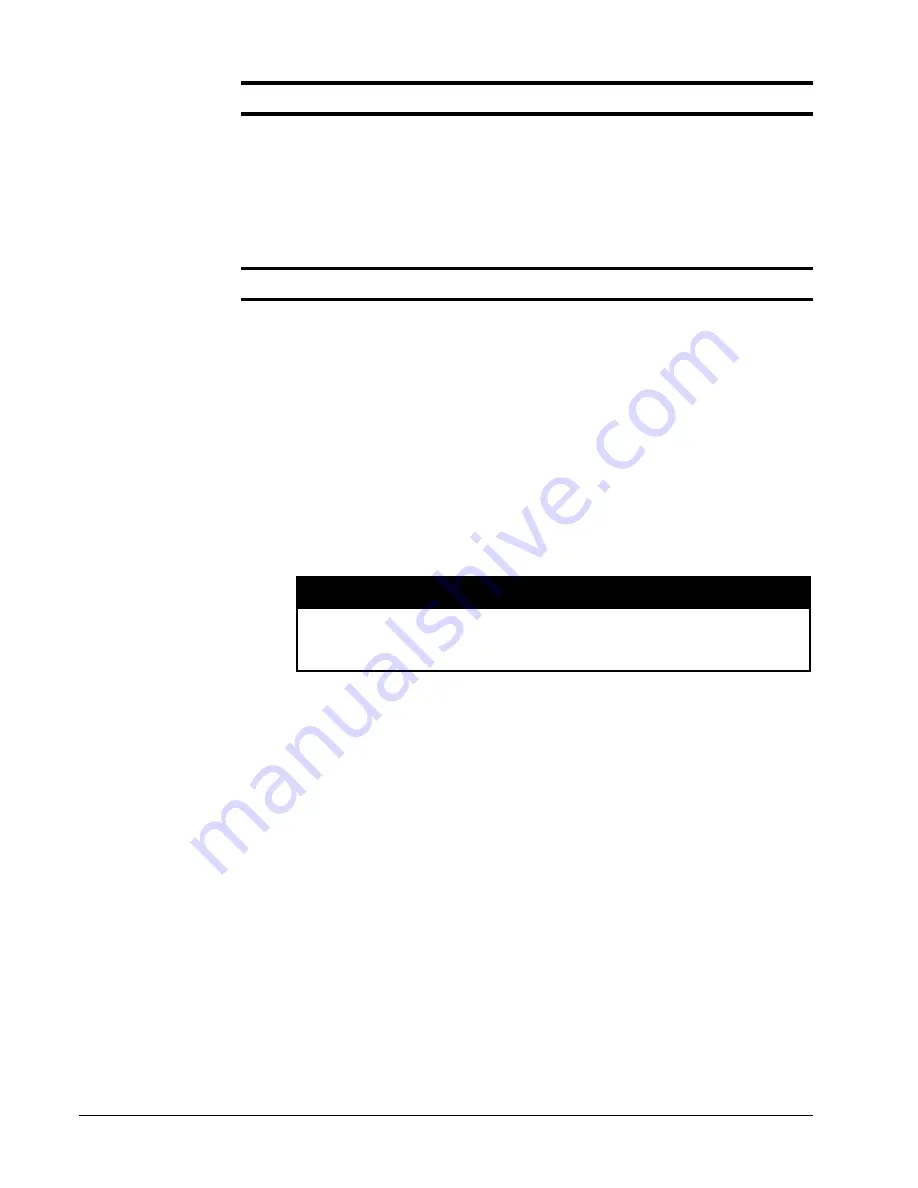
PCM-22 Rotary Knife Controller
56
© EMERSON Motion Control
115
Reset Master
Performs the same function as the
Force Reset Master Processing
flag
described in the FF command. It is intended for troubleshooting
purposes.
Note:
Resetting the Master Cycle Processing
will only occur when a
Follower Cycle is not executing and the Follower axis is not
moving.
116
Cycle Exit
Upon activation of this input function, the Follower will complete the
current cycle. When it has reached the end of the Working Segment, the
cycle will exit at the Working Segment velocity (see Working Ratio) and
execute the next step in the PCX program. After exiting the cycle, all
program steps are allowed except
Dwell
immediately following the
Y
Execute Follower Cycle statement
.
Dwell
requires that the Follower axis
be at zero velocity. If there are additional motion statements, the
Working Ratio velocity at the end of the Working Segment will serve as
the initial velocity for them. This is similar to compounded Indexes but
also works with Homes as well. If there are no more motion statements,
the Stop/Hold Decel Time from the Limits screen will be used after the
completion of the Working Segment.
This input is a latching type function. This means that the input need
only be pulsed once. It is cleared when the cycle is exited.
WARNING!
The next motion statement following the
Y Execute Follower Cycle
statement should not be an
Absolute Index
because the Follower axis
might reverse direction.
When used in conjunction with the
Cycle Drop Out
input function, the
following behaviors will be observed.
Please note that a machine cycle is viewed as going from the end of one
Working Segment
to the end of the next
Working Segment
. This input
function is only functional when in a cycle. See Figure 11.
•
If the
Cycle Drop Out
input function is active and the
Cycle Exit
input function is activated, the Follower will complete the
Cycle Drop
Out
and then exit the cycle at the
Cycle Drop Out Position
.
•
If the
Cycle Exit
input function is active and the
Cycle Drop Out
input function is activated, the
Cycle Drop Out
input function is
ignored and the Follower will exit the cycle at the end of the current
Working Segment
.
•
If the
Cycle Exit
input function and the
Cycle Drop Out
input
function are activated simultaneously, the
Cycle Drop Out
input
function is ignored and the Follower will exit the cycle at the end of
the current
Working Segment
.