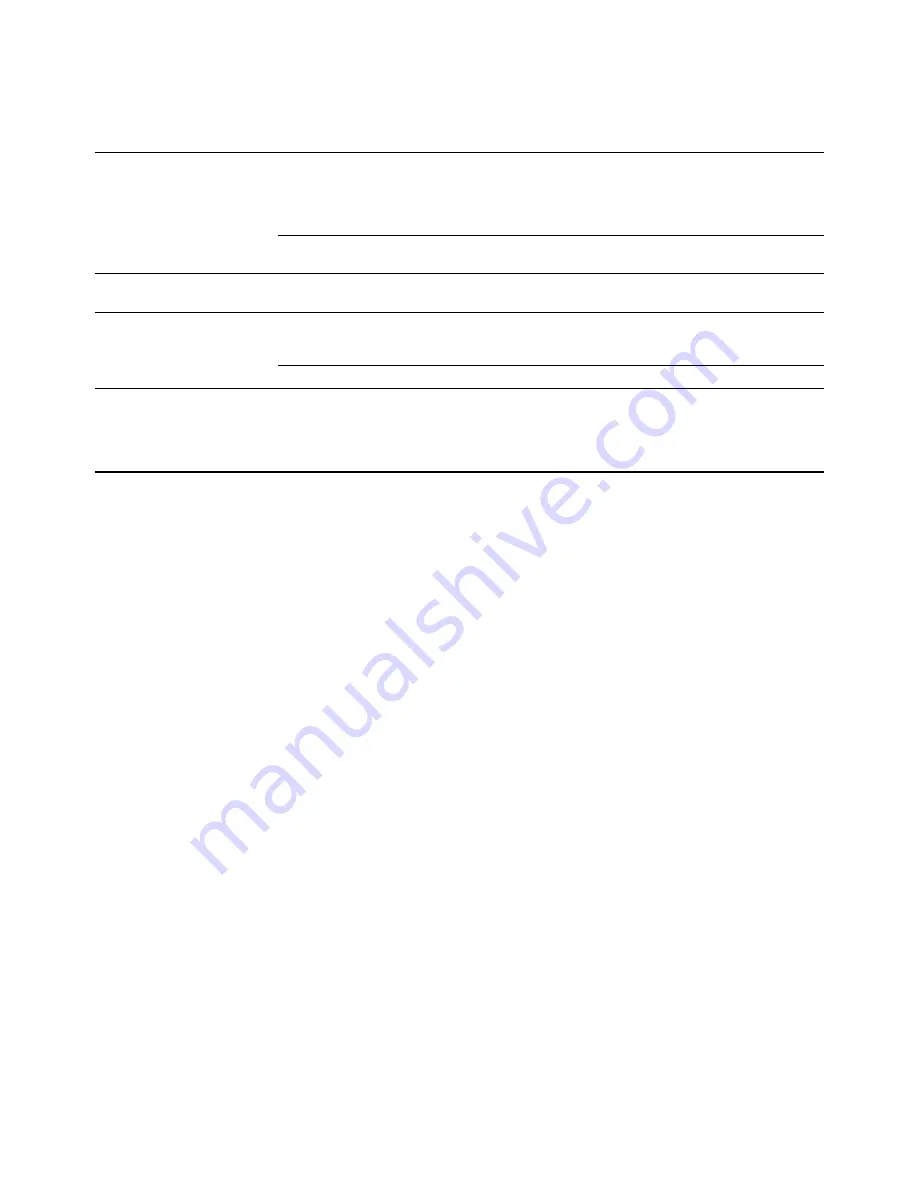
136
Micro Motion
®
Model 2400S Transmitters with Analog Outputs
Troubleshooting
11.10
Simulation mode
Simulation allows you to set the outputs to simulate process data for mass flow, temperature, and
density. Simulation mode has several uses:
•
It can help determine if a problem is located in the transmitter or elsewhere in the system. For
example, signal oscillation or noise is a common occurrence. The source could be the PLC, the
meter, improper grounding, or a number of other factors. By setting up simulation to output a
flat signal, you can determine the point at which the noise is introduced.
•
It can be used to analyze system response or to tune the loop.
If simulation mode is active, the simulated values are stored in the same memory locations used for
process data from the sensor. Therefore, the simulated values will be used throughout transmitter
functioning. For example, simulation will affect:
•
All mass flow, temperature, or density values shown on the display or reported via transmitter
outputs or digital communications
•
The mass total and inventory values
•
All volume calculations and data, including reported values, volume total, and volume
inventory
•
All related values logged by Data Logger (a ProLink II utility)
Accordingly, do not enable simulation when your process cannot tolerate these effects, and be sure to
disable simulation when you have finished testing.
Note: Unlike actual mass flow and density values, the simulated values are not
temperature-compensated.
Note: Simulation does not change any diagnostic values.
Simulation mode is available via ProLink II (
ProLink > Configuration > Sensor Simulation
) or the
Communicator (
Detailed Setup > Set up Simulation Mode
). To set up simulation mode, follow the
steps below:
1. Enable simulation mode.
Consistently incorrect
frequency measurement
Output not scaled correctly
• Check frequency output scale and method.
See Section 11.19. Verify voltage and
resistance match the frequency output load
resistance value chart (see your transmitter
installation manual).
Incorrect flow measurement unit
configured
• Verify flow measurement unit configuration.
See Section 11.21.
Erratic frequency
measurement
RF (radio frequency) interference from
environment
• See Section 11.14.3.
Cannot zero with zero button Not pressing zero button for sufficient
interval
• Button must be depressed for 0.5 seconds to
be recognized. Depress button until LED starts
to flash yellow, then release button.
Transmitter in fault mode
• Correct transmitter faults and retry.
DI is fixed and does not
respond to input switch
Possible internal/external power
configuration error
• Internal means that the transmitter will supply
power. External means that an external pull-up
resistor and source are required. Refer to your
transmitter installation manual for wiring, and
verify configuration (see Section 6.3).
Table 11-2
I/O problems and remedies
continued
Symptom
Possible cause
Possible remedy
Summary of Contents for Micro-Motion 2400S
Page 8: ...vi Micro Motion Model 2400S Transmitters with Analog Outputs ...
Page 20: ...12 Micro Motion Model 2400S Transmitters with Analog Outputs ...
Page 30: ...22 Micro Motion Model 2400S Transmitters with Analog Outputs ...
Page 42: ...34 Micro Motion Model 2400S Transmitters with Analog Outputs ...
Page 66: ...58 Micro Motion Model 2400S Transmitters with Analog Outputs ...
Page 76: ...68 Micro Motion Model 2400S Transmitters with Analog Outputs ...
Page 138: ...130 Micro Motion Model 2400S Transmitters with Analog Outputs ...
Page 190: ...182 Micro Motion Model 2400S Transmitters with Analog Outputs ...
Page 197: ......