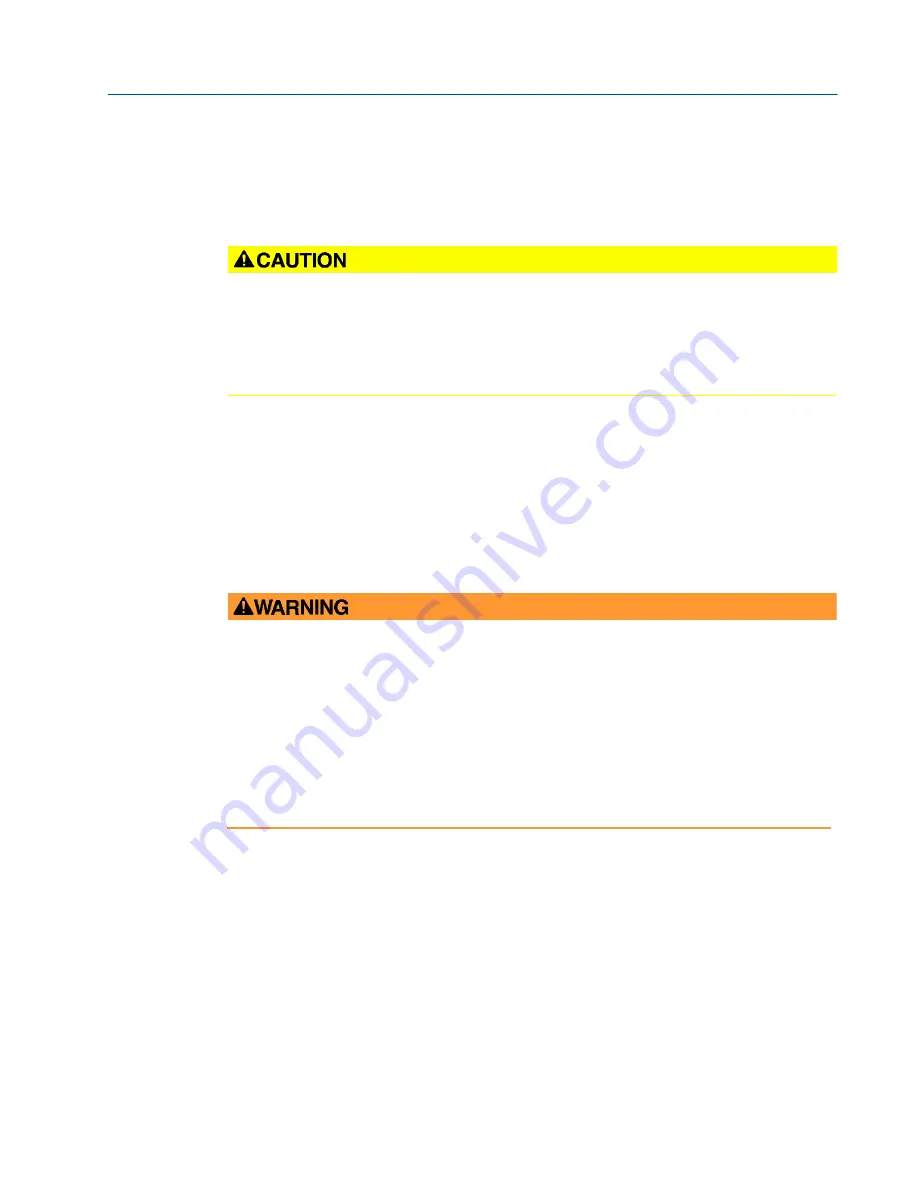
Owner and operator manual
Section 2: Installation
3-9008-001 Rev M
January 2015
Orifice Plate Installation
41
10.
Install the Sealing Bar (9 or 9HP), the Sealing Bar Gasket (9A, 9A-HP or 9CF), and the
Clamping Bar (12 or 12HP) in position on the Top (14) and tighten the Clamping Bar
Screws (11). Refer to
Section 5.3: Torque information
for actual torque values to use.
11.
Rotate the Slide Valve Shaft (5) to the CLOSED position. This closes the slide valve,
separating the Body (4) from the Top (14).
Steps 11 and 12 are for Seniors equipped with lubricated slide valves only. For Soft Seat
equipped Seniors, skip to step 13.
12.
Once the Slide Valve Shaft (5) is in the CLOSED position, remove the stem from the
Grease Gun (23) and insert a Daniel lubricant stick (refer to
) into the Grease Gun (23).
13.
Return the stem to the Grease Gun (23) and begin turning the stem by hand into the
Grease Gun (23) until resistance is felt. Once resistance is felt, use the supplied Daniel
Operating Wrench (2) to continue to turn the stem at a rate of 4 to 6 turns per minute.
14.
Close both the Equalizer (1) and the Bleeder Valves (10B).
15.
Remove any commissioning equipment (flanges, tubing, etc.) from the system.
16.
The Senior is now ready for final pressurization and operation.
LOOSE CLAMPING BAR SCREW HAZARD
The factory assembled and shipped this product with loose clamping bar screws. Tighten all
clamping bar screws before applying pressure to this product.
Failure to do so may result in injury or equipment damage.
PRESSURIZED FLUID HAZARD
Using the Grease Gun (23), inject grease into the slide valve seat channels at a rate of 4 to 6 turns
per minute and only under the following conditions:
• Bleeder Valve is open.
• Sealing bar/Clamping bar is in place and tight.
Injection of the grease at a faster rate will lead to the separation of the valve strip from the valve
seat, resulting in release of pressurized fluid which may cause serious injury or death.