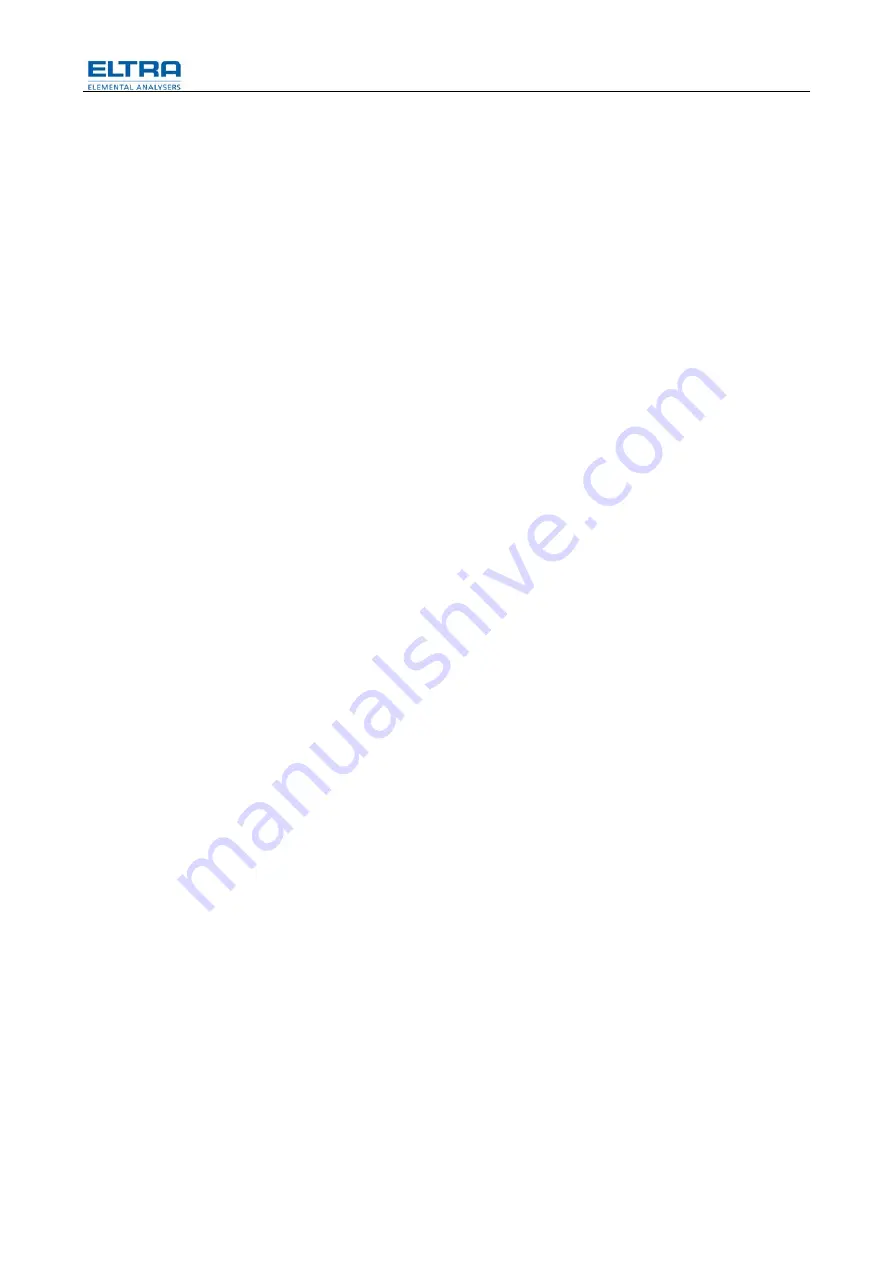
31
be too low oxygen pressure in the analyzer, especially at moments of high oxygen
consumption, like when burning samples or purging the furnace.
3.2.11
77B
Heavy item is placed on the plastic tube of the oxygen supply
Years of experience have shown that not only bent plastic tubes can be a reason
for insufficient oxygen supply, but also that a foot of the analyzer’s cabinet was
placed on the tube, squeezing it and restricting the oxygen flow. In one case, the
customer prolonged the tube using a fitting with too small inner diameter causing
the same effect like bending or squeezing the tube.
3.2.12
78B
Twisted plastic tube inside the analyzer
It happened that, when fixing cap nuts of the black plastic tube inside the analyzer
but also at the furnace outlet, the tube was turned with the nut and twisted, badly
restricting the oxygen flow.
3.2.13
79B
Oxygen supply is interchanged with the compressed air supply
In case of reported bad combustion, we experienced in a number of cases, that the
tubes of oxygen and compressed air supplies were interchanged. Compressed air
in the induction furnace will provide combustion but a bad one, because of only
20% of oxygen existing in the air. Therefore the peaks are low and long, consisting
of more than one peak, looking like mountains.
CAUTION: Oxygen in the pneumatic cylinder can lead to its explosion.
3.2.14
80B
Blocked dust filter cartridge
The dust filter cartridge is on the front panel so that contamination is visible for the
operator. In the gas flow circuit, this dust cartridge is connected after the metal filter
and its following glass tube with magnesium perchlorate, so that the carrier gas
passing thru the cartridge is already filtered. The cartridge is used as an additional
safety to ensure that the carrier gas passing thru the IR cell and the flow sensor,
are as clean as possible. Therefore it takes long until the cartridge is contaminated,
so that its ranking is almost at the end of the list.
3.2.15
81B
Blocked fittings
This case is extremely unlikely to happen in case of an induction furnace analyzer,
because the analyzed materials in question are inorganic materials like metals and
ceramics, so that they don’t create fumes, volatiles and moisture. Even cement
analysis is not as critical as organics analysis. Anyway, this information is included
in this list in order to have it complete.
In case of analysis of materials causing major contamination, the fittings of the IR
cells can be blocked so that they have to be cleaned.
Also fittings elsewhere can be blocked, like the fittings for plastic tubes on the
reagent glass-tube holders.
3.2.16
82B
Blocked flow sensor assembly
If the flow sensor is blocked, it should normally be replaced.
For those who may decide to clean them - please read the description about
cleaning.
3.2.17
83B
Electronic problem
The flow controller consists of 3 components:
1.
The flow sensor
2.
The board HF-42 (The lower half of the board only).
3.
The proportional valve V6.
The electronic devices involved in the flow regulation are the board HF-42 and the
flow sensor. The only influence of the PC and of the microcontroller on the flow, is
the start/stop of the flow in case of gas saving mode.
Summary of Contents for CS-800
Page 3: ...3 ...
Page 10: ...10 Fig 2 Draft 12057 ...
Page 11: ...11 Fig 3 Draft 11660 ...
Page 12: ...12 Fig 4 Draft 12200 ...
Page 14: ...14 Fig 6 Draft 12058 Signal and control ...
Page 17: ...17 Fig 8 Draft 6 2 4 Gas flow diagram furnace closed ...
Page 18: ...18 Fig 9 Oxygen flow schematically ...
Page 19: ...19 Fig 10 Draft 12059 signal and control board ...
Page 21: ...21 Fig 12 Draft VG 96 connector ...
Page 22: ...22 Fig 13 Draft 1 14 4 1 ...
Page 23: ...23 Fig 14 Draft IR 45 power supply ...
Page 24: ...24 Fig 15 Draft IR sources Fig 16 Draft 7 pin plug ...
Page 80: ...80 Abb 46 IRC 1 3 ...
Page 82: ...82 Fig 29 Mainboard Cut out IR Cell general test points ...
Page 91: ...91 Abb 47 Pneumatics parts 2 1 3 4 5 6 7 8 9 10 11 12 13 14 15 ...
Page 94: ...94 bar 0 5 1 1 5 2 2 5 0 PR2 1 Fig 49 Front side 4 5 47BPurge pressure Fig 50 PR2 5 6 ...
Page 109: ...Service 109 10 10 11 9 b7 10 1 12 8 5 6 Fig 60 b7 10 1 ...
Page 110: ...Service 110 ...
Page 119: ...Miscellaneous 119 77510 Heaters for IR cell ...
Page 120: ...Miscellaneous 120 6 1 2 121BFront side Fig 41 Front side ...
Page 122: ...Miscellaneous 122 6 1 3 122BRight side Fig 42 Right side ...
Page 126: ...Miscellaneous 126 6 1 5 124BOscillating circuit Fig 44 Oscillating circuit ...
Page 132: ...Miscellaneous 132 21010 Heather section 21120 Quartz tube 70380 O Ring 70380 21120 21010 ...
Page 134: ...Miscellaneous 134 Fig 47 12055 I ...
Page 135: ...Miscellaneous 135 Fig 48 12055 II ...
Page 136: ...Miscellaneous 136 Fig 49 12072 ...
Page 137: ...Miscellaneous 137 Fig 50 12064 ...
Page 138: ...Miscellaneous 138 Fig 51 12550 Vacuum cleaner ...
Page 139: ...Miscellaneous 139 Fig 52 12015 I ...
Page 140: ...Miscellaneous 140 Fig 53 12015 II ...
Page 141: ...Miscellaneous 141 Fig 54 12016 ...
Page 143: ...Miscellaneous 143 6 2 1 127BUNI 1 ...
Page 144: ...Miscellaneous 144 6 2 2 128BGas flow system ...
Page 145: ...Miscellaneous 145 ...
Page 146: ...Miscellaneous 146 6 2 3 129BValve controlling Fig 55 Valve controlling I 11001 6001 ...
Page 155: ......
Page 156: ......
Page 157: ......