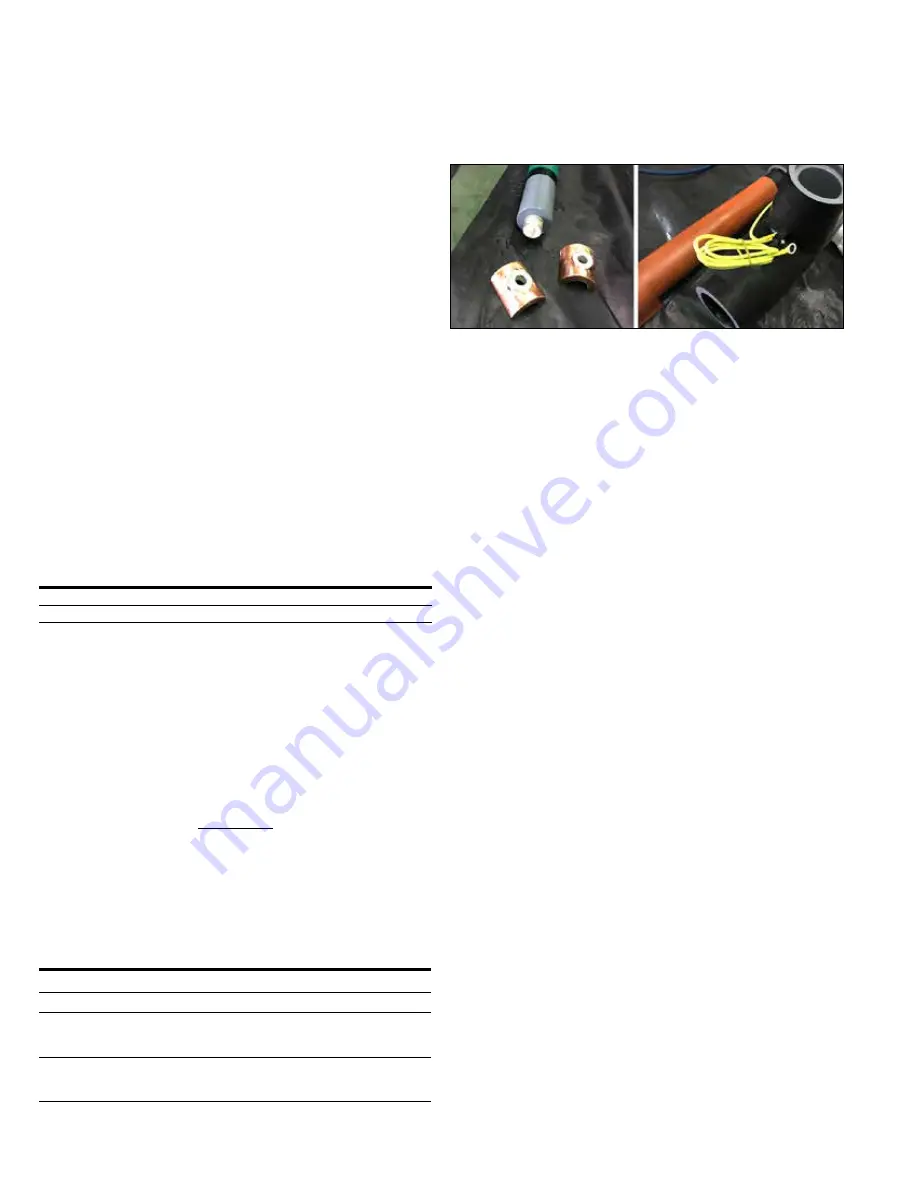
52
Instruction Booklet
IB022018EN
Effective July 2020
Instructions for the installation and
EATON
www.eaton.com
5.9.2 Field installation precautions
5.9.2.1 Handling of SSIS silicone rubber insulator plug-in
parts
SSIS (Solid Shielded Insulation System) components are insulated
with silicone. All conductors, terminations and covering devices
must be inspected for damage or defects prior to operation.
All SSIS silicone insulator surfaces must have no
•
Bubbles
•
Scratches
•
Visible damage
•
Foreign material contaminants
•
Evidence of wear
If any surface contamination is noticed on any SSIS component,
it must be cleaned. Remove any dirt, oil or grease on any silicone
insulator using a soft clean, lint-free wipe;
Clean silicone rubber insulators using the provided special wet
cleaning wipe. Apply medium force to clean the black area of the
silicone rubber insulator connect to the bus. Never wipe from the
black area to the red insulation surface;
Use a dry, soft, clean lint-free wipe to remove excessive cleaning
solution. The solution may cause a slight expansion of the silicone
rubber, so any cleaned silicone parts must be air-dried for at least 15
minutes.
Apply the provided silicone grease evenly to the insulator and
silicone rubber part, according to
.
Table 11. SSIS bus and joints silicone grease application guide
Part
Silicone grease amount
SSIS bus and bus joints
About 20g
SSIS bus plug
About 10g
•
Clean and dry the contact surface of the socket and the silicone
rubber part. Apply another thin layer of silicone grease.
•
Assemble the cleaned conductors and couplings immediately.
5.9.2.2 Preparations before installation
Unpack the equipment, check the contents of the accessory kit and
the XGIS vertical sections. The accessory kit includes NB52 grease,
silicone grease and cleaning wipes, etc.
5.10 Installing the bus and bushing
IMPORTANT
Successful application of the SSIS busbar connecting XGIS vertical
sections depends upon proper centerline distances between
vertical section phase cones. Busbar sections to be used between
the cones will have these lengths. Confirm these distances before
installing SSIS busbar sections. See
Table 12. Main bus cone centerline distances
Adjacent section configuration
Centerline distance between
phase cones
Two 600 mm sections
600 mm
Two 800 mm sections
800 mm
One 600 mm and one 800 mm (left to right) phase A - 650 mm
phase B - 700 mm
phase C - 750 mm
One 800 mm and one 600 mm (left to right) phase A - 750 mm
phase B - 700 mm;
phase C - 650 mm
Use the smooth cleaning wipe supplied with the accessory kit to
thoroughly clean the bus (copper bar) and silicone bus joint, on the
inside and outside surfaces.
Figure 88. SSIS busbar and bush joint.
The silicone surface tends to absorb dirt which cannot be removed
with the smooth wipe. If this has occurred, anhydrous alcohol or
acetone cleaner can be used to wipe it clean.
After the silicone bushing has been cleaned, it must be air dried.
Alcohol or acetone will cause the silicone to expand. Any expansion
must be eliminated before final installation can be started. Use a
drying gun to facilitate quick evaporation of alcohol from the surface
after cleaning to minimize likelihood of dust re-settling on the
silicone surface.
When a 2500 A main bus feeds vertical sections rated 1250 A,
the bus joints used are used in a way that accommodates each
connection point. See