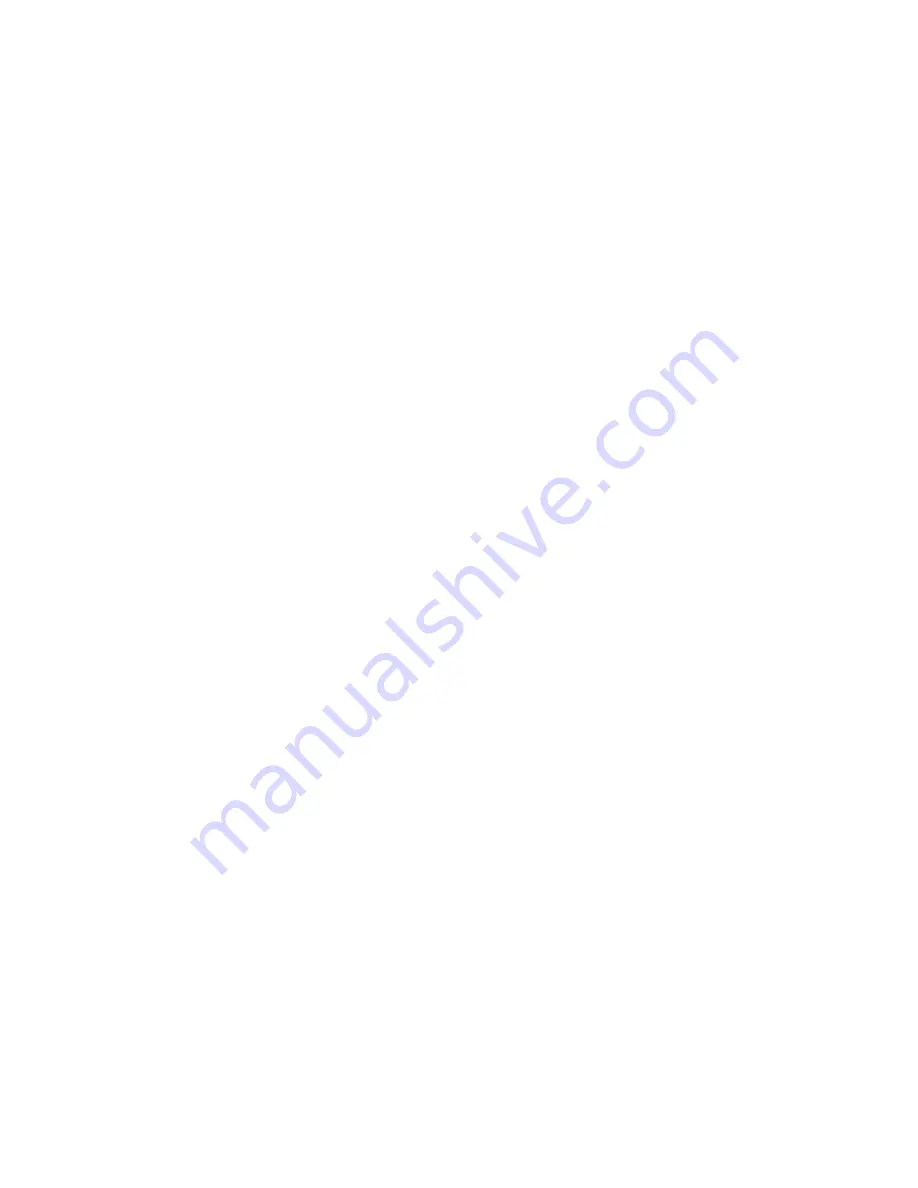
76
Instruction Booklet
IB022018EN
Effective July 2020
Instructions for the installation and
EATON
www.eaton.com
Appendix A - XGIS switchgear commissioning checklist,
continued
Key Interlocking (3PDS)
Confirm operation of 3PDS Kirk key and Padlock interlocking,
per the provided interlocking schemes:
Prevent Closing (PC) and Prevent Grounding (PG)
(standard)
Locked in Closed position and Locked in Grounded position
(if furnished)
Any additional interlocking sequences of operation as
required by the application
Verify Kirk Key number and exchange
Additional Interlocking
Verify with BREAKER open and 3 position switch open
that the switch cannot be moved to GROUND if voltage is
detected by the CVD (capacitive voltage device)
Verify that the VT Earthing Switch can be locked in either the
CONNECTED or GROUND position
VT Installation/ removal
Have MSDS’s for installation products, De-natured alcohol,
Silicone grease, etc.
Verify proper voltage ratings
Clean both sides of primary connections, Spout and socket
Lubricate spout and socket
Using adequate lifting device (500 pound minimum rating),
lower the VT into its socket, being careful of alignment. Note:
the approximate weight of a VT is 200 pounds. See section
.
Using a 30” minimum length 3/8 inch extension with a 6mm
hex key type socket, secure all four hold down bolts. Make
sure to secure the socket and 6mm bolt either magnetically or
with adhesive tape.
Gas sampling (optional)
Have proper required Material Safety Data Sheets for any
cleaning products and SF
6
Gas
Check SF
6
gas filling (allow time for ambient temperature
equalization
Check gas pressure
Test for leaks
Clean area around sample/ access port
Remove protective cap
Install adapter
Take sample
Check gas quality (optional)
Prepare sample for proper shipment per DOT requirements
Monitor gas pressure over two-week period
Bus Installation
Note:
Need to test each section’s contact resistance prior to bus
assembly
Method of installation - see section
Cleaning of bus parts
Lubrication of bus parts, Contact grease on end that fit into
clam shell, silicone grease on body
Install bus sections.
Note
: optional CTs may be part of this
installation process.
Torque studs to 15 Nm, bolts to 45 Nm and plugs to 30 Nm.
Measure contact resistance between studs, verify consistency
between similar sections
Install boot caps
Ground and confirm shield wire connections for bus sections,
cross bus joints and end bus joints.
Confirm all bus joint covers are installed
Check connections
Check high voltage connections, confirm main bus and cable
connection torques
Check ground connections for all bus, bus joints, cables, cable
connectors and arresters (if furnished)
Check low voltage control cables and wiring for connection,
tightening torque
Check all CT secondary circuits for connection, polarity
Check all VT secondary circuits for connection
Check all fault detecting devices for connection
All unused switching devices must be grounded and locked
out
Confirm all covers have been fitted; all bus joint and cable tee
connectors caps have been installed; all cable compartment
access covers have been installed
Install high voltage cables after busbar HV testing is complete
(
note
: with XGIS, Hi-pot testing with cables installed is
acceptable)
Protective devices
Confirm proper settings and operation of protective relays
Confirm proper settings and operation of Voltage Detection
System devices