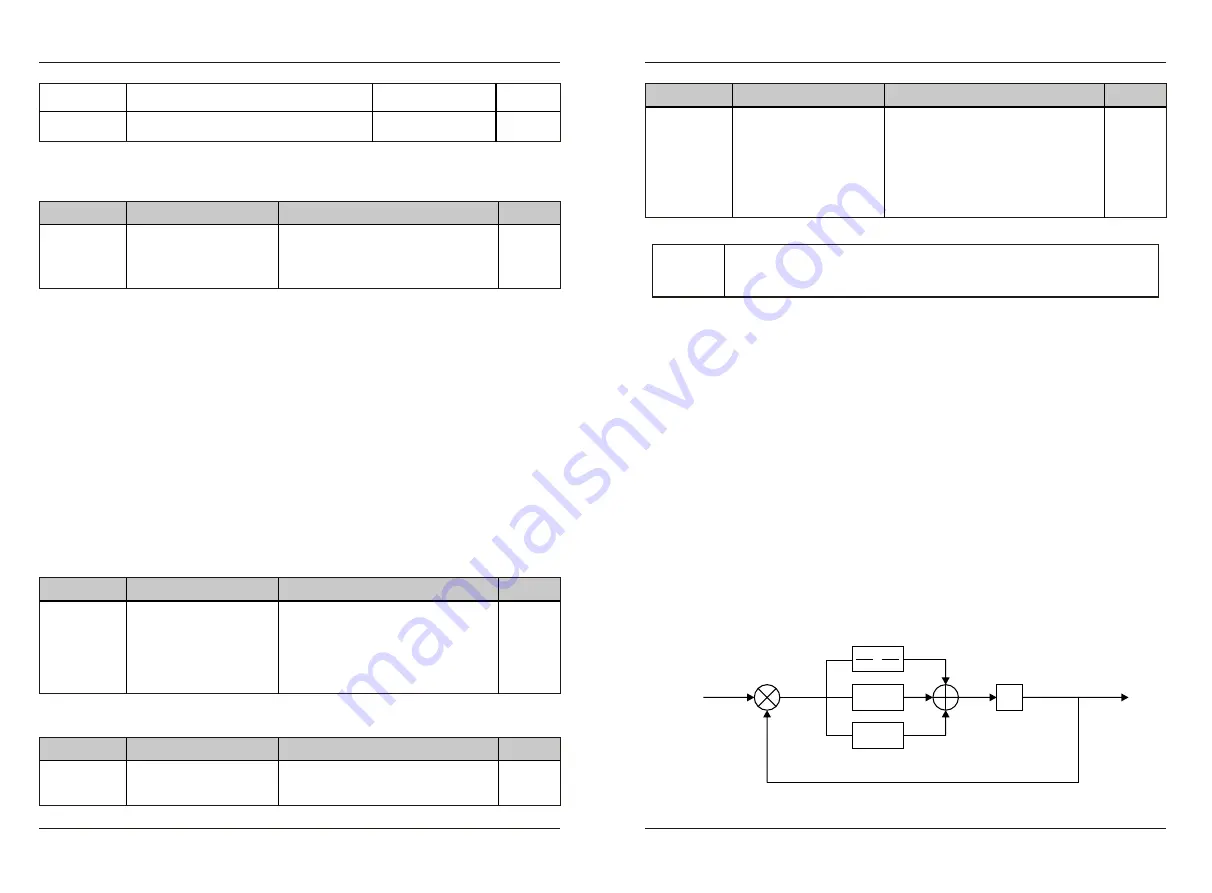
EC590
Function parameters description
EC590
Function parameters description
-
49
-
-
50
-
FC-48
Running time of simple PLC reference 15
0.0s (h)
0.0s (h) to 6553.5s (h)
FC-49
Acceleration/deceleration time of simple PLC
reference 15
0
0 to 3
FC-16 determines the simple PLC running mode.
Function Code
Parameter Name
Default
FC-16
Simple PLC
running mode
Setting Range
0
0: Stop after running one cycle
1: Keep final values after running one cycle
2: Repeat after running one cycle
FC-16 = 0: Stop after running one cycle
The AC drive stops after running one cycle, and will not start until it receives a new RUN com
-
mand.
FC-16 = 1: Keep final values after running one cycle
The AC drive keeps final running frequency and direction after running one cycle.
FC-16 = 2: Repeat after running one cycle
The
AC drive automatically starts another cycle after running one cycle, and will not stop until
receiving stop command.
●
●
●
FC-17 determines whether the running data is retentive at power down or at stop.
If retentive, the running data is memorized at power down or at stop and the AC drive will con
-
tinue to run from the memorized data at next power-on.
If not retentive, the AC drive runs from the first simple PLC reference at next power-on.
Function Code
Parameter Name
Default
FC-17
Simple PLC retentive
selection
Setting Range
00
BIT0:Retentive at power down
0: Not retentive
1: Retentive
BIT1
:
Retentive at stop
0: Not retentive at stop
1
:
Retentive
at
stop
FC-50 sets running time unit in simple PLC mode. FC-51 selects the setting channel of reference 0.
Function Code
Parameter Name
Default
FC-50
Time unit of simple PLC
running
Setting Range
0
0: s (second)
1: h (hour)
Function Code
Parameter Name
Default
FC-51
Reference 0 source
Setting Range
0
0: Set by FC-00
1: AI1 2: AI2
3: Keyboard potentiometer
4: Pulse reference 5: PID
6: Set by preset frequency (F0-08),
modified via terminal UP/YWN
Note
Simple PLC can be either frequency reference setting channel or voltage
reference setting channel for V/F separation.
PID ReferenceThe PID (Propor In Derivative) function uses system feedback for
closed-loop control of variables such as flow, pressure, temperature, and so on.
The purpose of PID control is to keep the drive output as close as possible to a desired reference
via PID adjustment.
Proportional gain (Kp1)
A large value tends to reduce present error, but too large setting will cause system oscillation.
Integral time (Ti1)
The shorter the integral time is, the faster the error will be predicted. But too short setting will
cause overshoot or system oscillation.
Derivative time (Td1)The longer the derivative time is, the faster the system will respond to the
error. But too longer setting will cause vibration.
●
●
■
●
T
arget
amount
Amount of feedback
PID output control
amount
1
Td*s+1
1
1
Ti
S
P
+
-