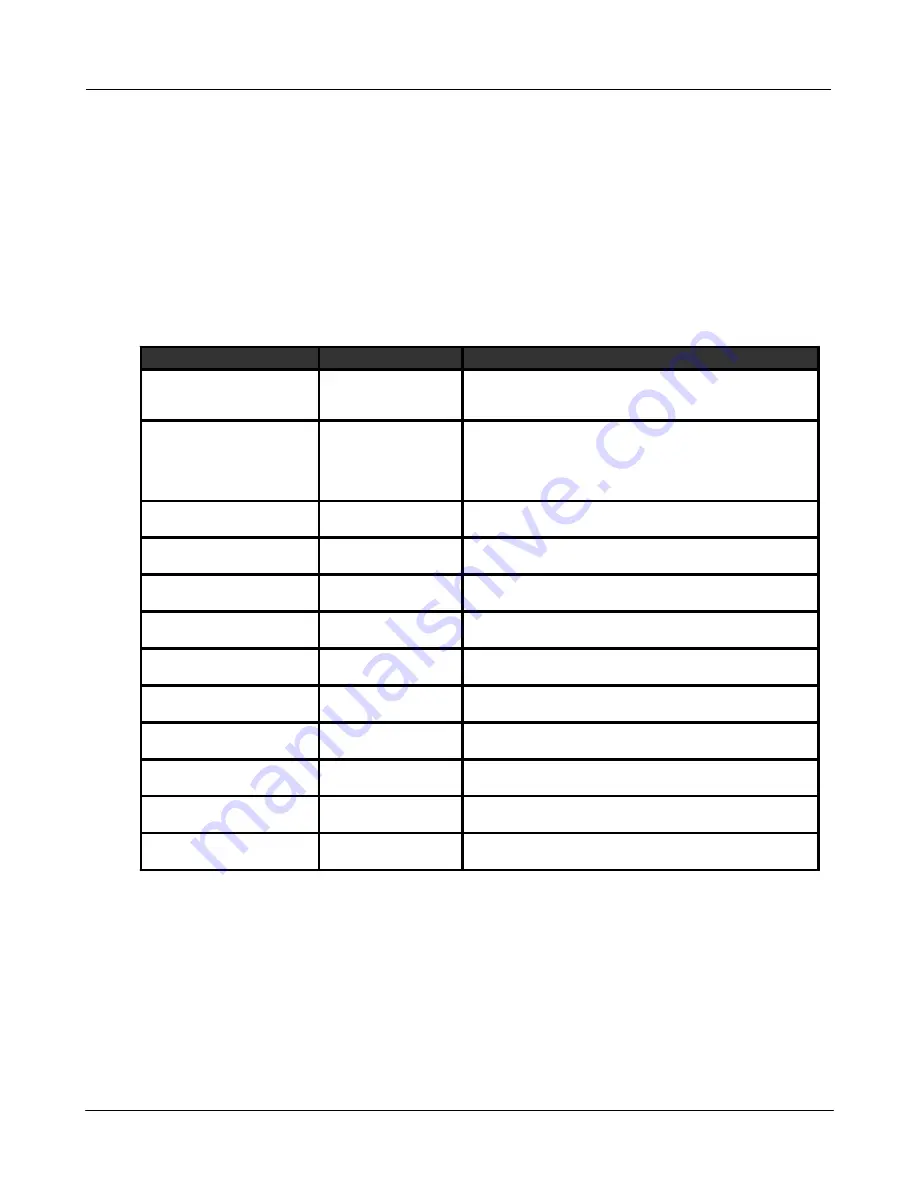
Settings
65
© 2017 DynaGen Technologies Inc
TOUGH Series Manual
4.8.3
Process Control
The Process Control feature has two different control methods: Main-In and Main-Out. The Main-In maintains a reservoir level by
controlling the flow of fluid into the reservoir. The Main-Out maintains a reservoir level by controlling the flow of fluid from the
reservoir. It does this by regulation the speed of the engine over the J1939 CAN bus.
The controller reads the sensor value from selected Auxiliary Sensor input (1~5), compares the input value with the set-point, and
then, based on an algorithm, increments or decrements the speed (RPM) by a certain amount to maintain the desired set-point
outside of the dead-band area. Control pauses inside the dead-band area. If the sensor input goes beyond a minimum or maximum
value, the algorithm will pause and the RPM will be maintained at a minimum or maximum value.
The algorithm is a fuzzy logic type control with a dead band and a minimum / maximum saturation. The user sets the
aggressiveness of the control with the
Gain
setting and the response time of the control with the
Delay
setting.
(Other Config > Process Control menu)
Name
Range
Description
Closed Loop > System (Control
Type)
Disabled
Main-In (Maintain In)
Main-Out (Maintain Out)
Main-In controls the level when pumping fluid into a reservoir.
Main-Out controls the level while pumping fluid out of the reservoir.
Closed Loop > Sensor In
(Sensor Input)
AUX-1
AUX-2
AUX-3
AUX-4
AUX-5 (Transducer)
The Auxiliary Sensor Input function that is providing feedback on
the reservoir level. Aux-5 refers to the Transducer under the
Application menu.
Closed Loop > Delay
1 ~ 30 s in 0.1 s
increments
The sampling time of the control algorithm.
Closed Loop > Gain
1 ~ 30 in 0.1 increments
The amount to increment or decrement the RPM when the sensed
value is outside of the dead-band.
Setpoints > Main-In (Maintain In
Setpoint)
1 ~ 900 in 0.1 increments The level set-point to attempt to maintain. Only applies if System
is set to In-Keep.
Setpoints > Main-Out (Maintain
Out Setpoint)
1 ~ 900 in 0.1 increments The level set-point to attempt to maintain. Only applies if System
is set to Out-Keep
Setpoints > D (High
Deadband)
1 ~ 30 in 0.1 increments
The high limit of the dead-band.
Setpoints > Deadband- (Low
Deadband)
1 ~ 30 in 0.1 increments
The low limit of the dead-band.
Thresholds > High Edge (High
Limit)
1 ~ 900, 0.1 increments
The high saturation. The maximum level at which the RPM control
is fixed.
Thresholds > Low Edge (Low
Limit)
1 ~ 900, 0.1 increments
The low saturation. The minimum level at which the RPM control is
fixed.
Thresholds > Max RPM (Max
Limit RPM)
500 ~ 4000 RPM in 1
RPM increments
The fixed RPM that should be used when the level rises above the
High Edge.
Thresholds > Min RPM (Low
Limit RPM)
500 ~ 4000 RPM in 1
RPM increments
The fixed RPM that should be used when the level falls below the
Low Edge.
Summary of Contents for TG410
Page 4: ...3 2017 DynaGen Technologies Inc TOUGH Series Manual User Guide ...
Page 11: ...Installation 10 2017 DynaGen Technologies Inc TOUGH Series Manual 2 3 Wiring Harnesses ...
Page 12: ...Installation 11 2017 DynaGen Technologies Inc TOUGH Series Manual 2 4 Typical Wiring Diagram ...
Page 17: ...Installation 16 2017 DynaGen Technologies Inc TOUGH Series Manual ...
Page 20: ...Installation 19 2017 DynaGen Technologies Inc TOUGH Series Manual ...
Page 22: ...Installation 21 2017 DynaGen Technologies Inc TOUGH Series Manual ...
Page 40: ...Settings 39 2017 DynaGen Technologies Inc TOUGH Series Manual ...