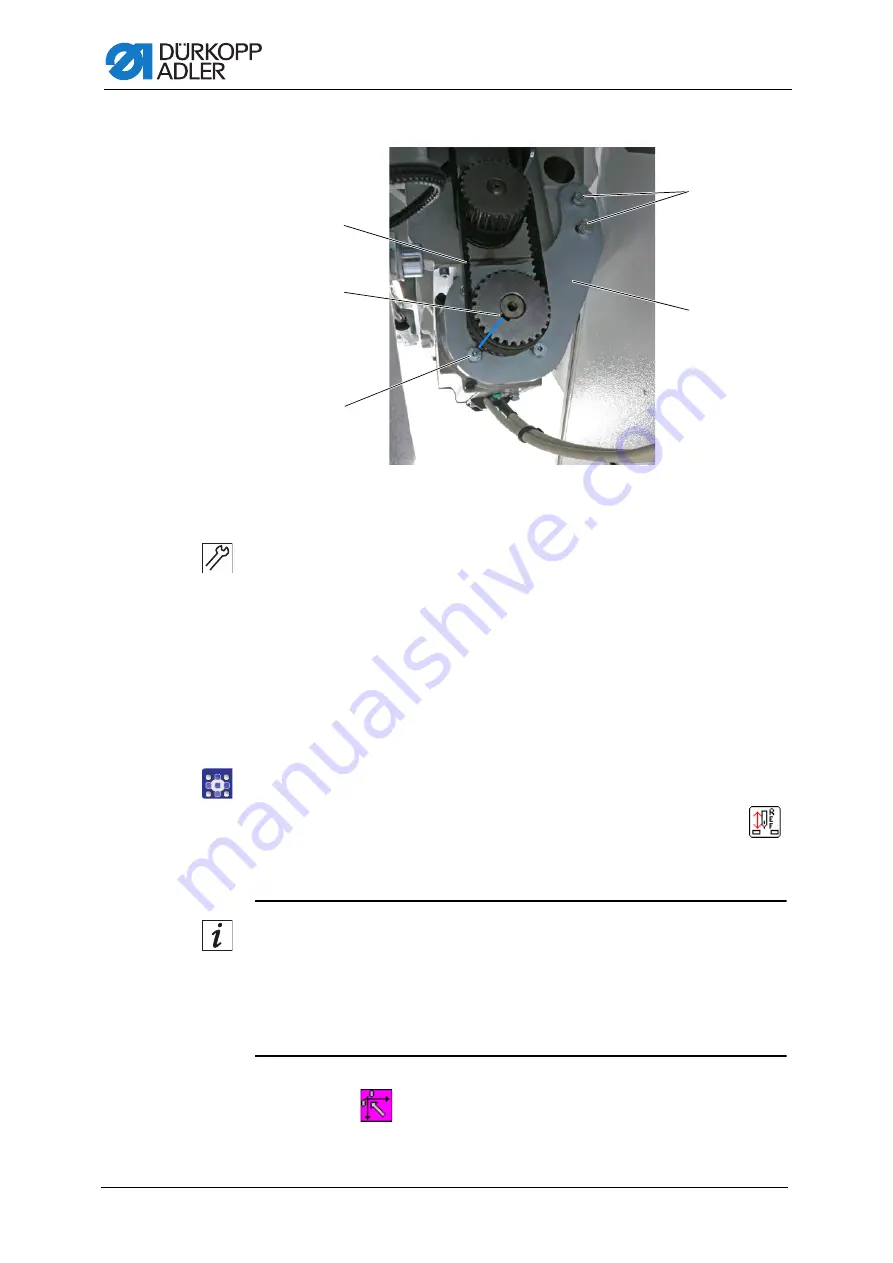
Changing the sewing motor
100
Service Instructions 755 A/756 A - 00.0 - 02/2019
Fig. 105: Changing the sewing motor (3)
16. Place the toothed belt (3) such that the spring groove (7) points to
the screw (8).
17. Tension the toothed belt (3).
To do so, turn the sewing motor holder (5) down until the toothed belt (3)
is tensioned.
18. Tighten the screws (4).
19. Switch on the machine.
The sewing motor moves to its internal reference position.
The handwheel automatically adjusts to the value that corresponds
to the sewing motor position.
20. Correct the sewing motor position.
To do so, open the menu
Service > Machine test > Test
sewing motor > Adjust sewing motor
and press the button
.
21. Adjust the value such that the handwheel will subsequently be set
to the 40° position.
Correction example
The handwheel will be set to the 45° when the machine is switched on.
Consequently, the sewing motor must be corrected by a value of 5°
to reach a position of 40°.
The value that must be entered is +5 as the drive shaft rotates in
the opposite direction of the handwheel marking.
22. Press the
button.
The machine performs a reference run.
23. Check the handwheel position and readjust it if necessary.
(3)
- Toothed belt
(4)
- Screws
(5)
- Sewing motor holder
(7)
- Spring groove
(8)
- Screw
⑤
④
③
⑦
⑧
Summary of Contents for 755 A
Page 1: ...755 A 756 A Service Instructions...
Page 8: ...Table of Contents 6 Service Instructions 755 A 756 A 00 0 02 2019...
Page 12: ...About these instructions 10 Service Instructions 755 A 756 A 00 0 02 2019...
Page 116: ...Folder 114 Service Instructions 755 A 756 A 00 0 02 2019...
Page 124: ...Transport carriage 122 Service Instructions 755 A 756 A 00 0 02 2019...
Page 138: ...Transport clamps 136 Service Instructions 755 A 756 A 00 0 02 2019...
Page 200: ...Light barriers 198 Service Instructions 755 A 756 A 00 0 02 2019...
Page 222: ...Endless zipper feed optional 220 Service Instructions 755 A 756 A 00 0 02 2019...
Page 238: ...Additional equipment 236 Service Instructions 755 A 756 A 00 0 02 2019...
Page 266: ...Stacker 264 Service Instructions 755 A 756 A 00 0 02 2019...
Page 438: ...Programming 436 Service Instructions 755 A 756 A 00 0 02 2019...
Page 450: ...Decommissioning 448 Service Instructions 755 A 756 A 00 0 02 2019...
Page 452: ...Disposal 450 Service Instructions 755 A 756 A 00 0 02 2019...
Page 472: ...Technical data 470 Service Instructions 755 A 756 A 00 0 02 2019...
Page 496: ...Appendix 494 Service Instructions 755 A 756 A 00 0 02 2019...
Page 497: ......