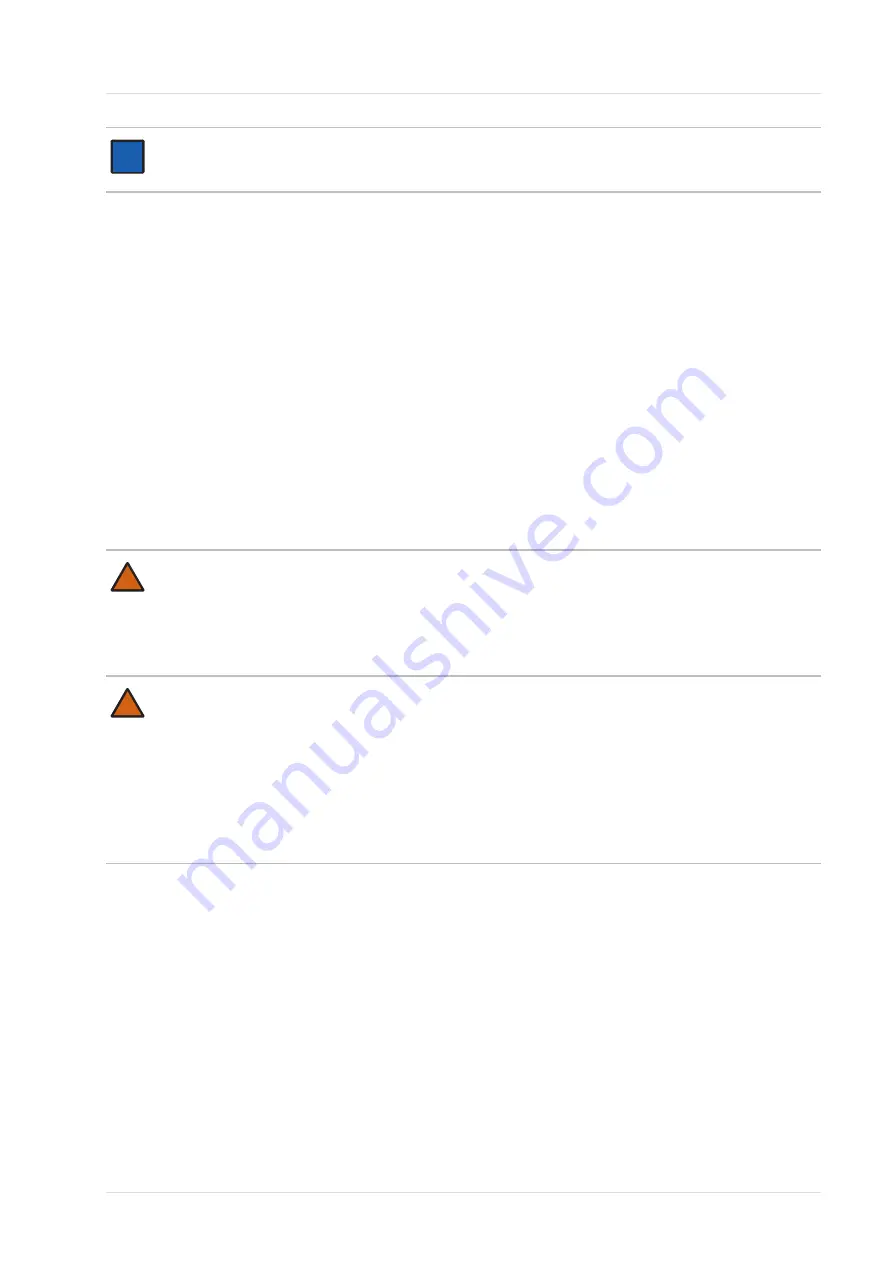
Safety-related information
Edition 03 / 69 06 898
2
FTS 8000
1.2.3
Notes on using these operating instructions
Emphases in the text have the following meanings:
•
Points and requirements for operating procedures are labeled with bullet points.
1. Handling instructions are labeled with numbers.
Results of instructions are shown in italics.
Displays on the system are given in "quotation marks."
Item numbers (Item) of figures and illustrations are numbered consecutively in these
operating instructions.
1.3
Intended use
This system is used solely for the following purpose:
•
Controlled simulation of fire events with practical fire department exercises and other
emergency responders.
1.4
Limitation of the intended use
Any use other than that described in the "Intended use" chapter should be regarded as
incorrect use. Especially the following points are not permitted:
•
Using the system with other mock-ups than with the mock-ups supplied.
•
Accessing the system without wearing the personal protective equipment (PPE)
required for the respective tasks and dangers.
Otherwise, the safe operation of the system is at risk.
i
i
NOTICE
Additional information on using the system.
!
WARNING
Risk of fatal injury in the event of changes to the system
Modifications and rebuilding of the system performed without written consent of the
manufacturer are prohibited. Dräger accepts no liability for personal injury or material
damage arising as a result of unauthorized modifications.
!
WARNING
The system’s design, the corresponding customer documentation and the signs and
labeling in the facility all presume that the facility is only used by experts who know the
basic functions of the system.
The instructions on operation and the notices labeled Warning, Danger and Caution are
restricted primarily to the special features of the system.
These operating instructions contain no notices on dangers that can be presumed to be
known to firefighters and rescue teams.