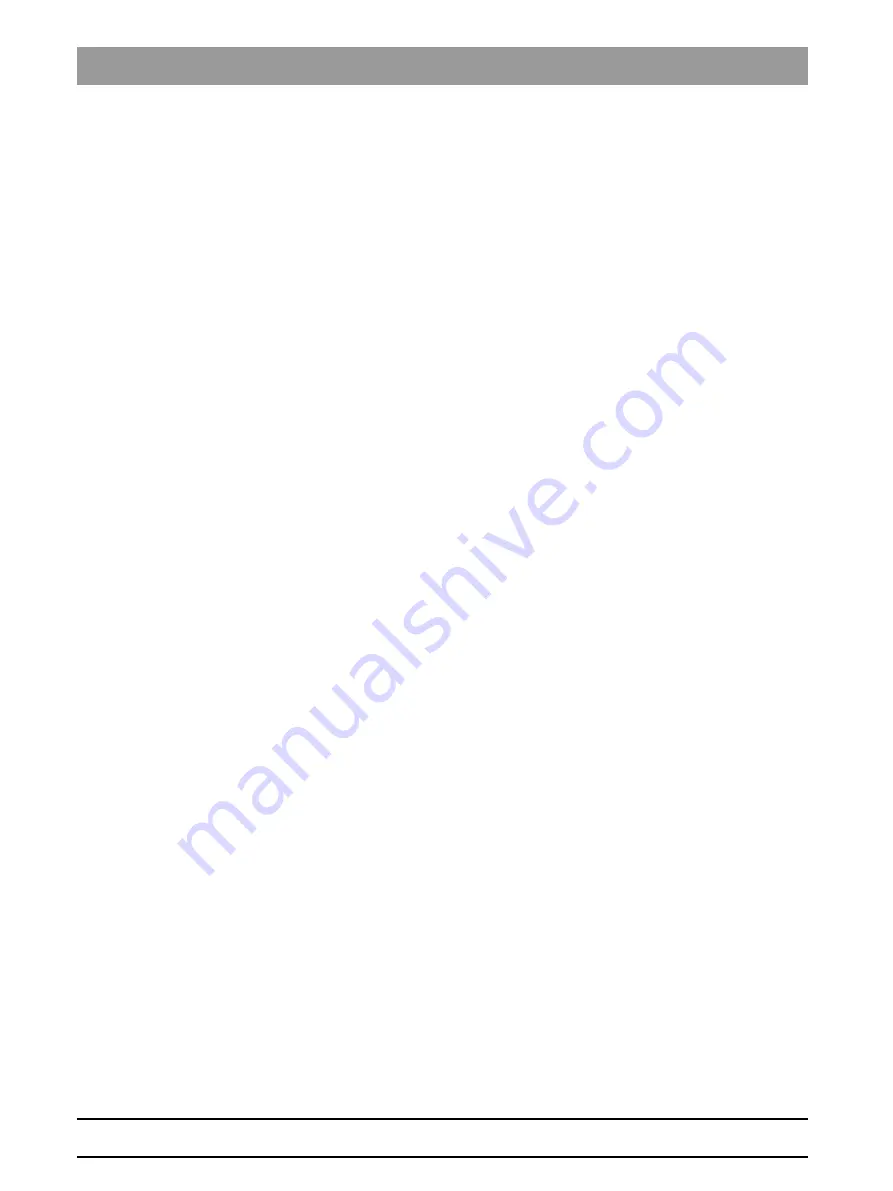
64 78 759 D3608
2
D3608
.
201.01.07
.
02 10.2017
Dear Customer,
Dentsply Sirona
Operating Instructions inLab MC X5
Dear Customer,
Thank you for your purchase of this inLab MC X5
®
unit from Dentsply
Sirona.
This device enables you to produce dental restorations, e.g. from ceramic
material with a natural appearance (CEramic REConstruction).
Improper use and handling can create hazards and cause damage.
Please therefore read and follow these operating instructions carefully.
Always keep them within easy reach.
Also pay attention to the safety instructions to prevent personal injury and
material damage.
Your
inLab MC X5 team