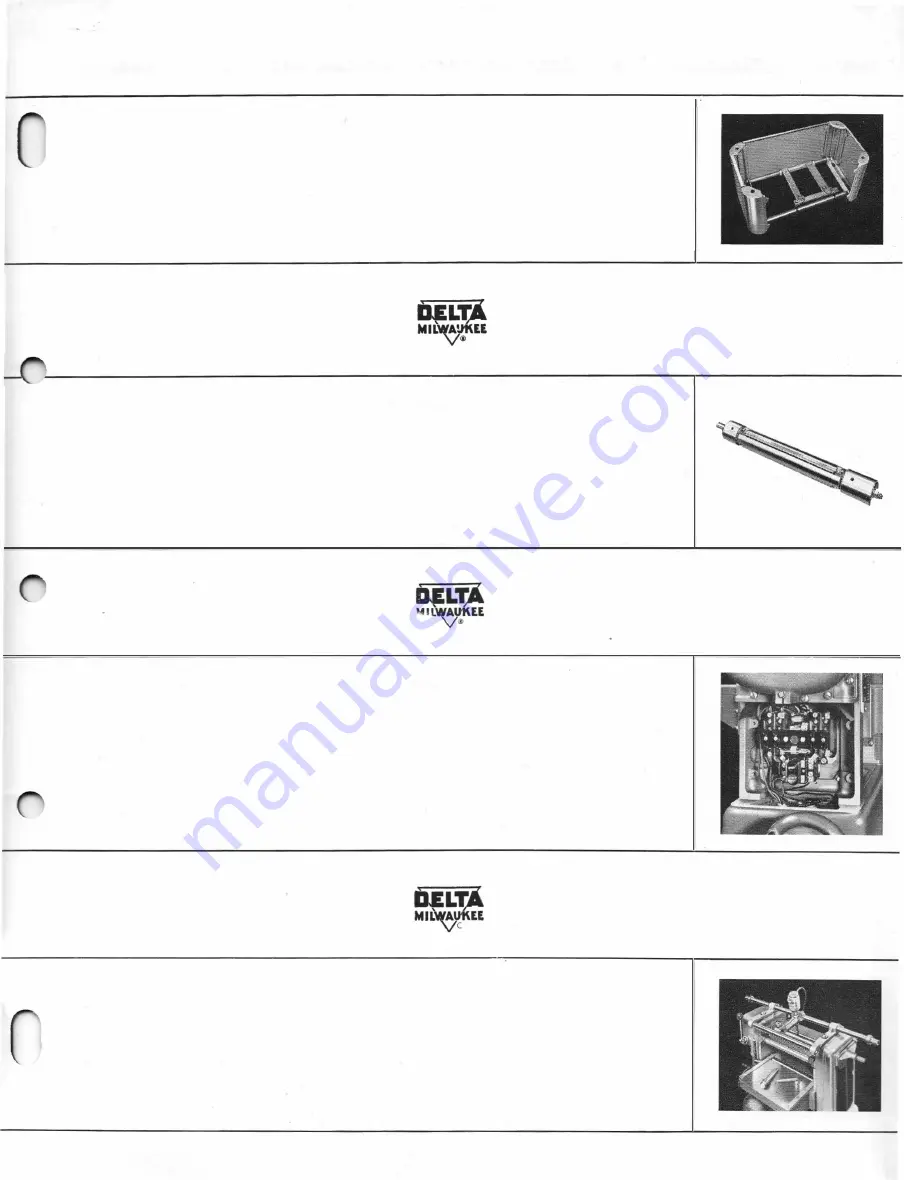
.
ACCESSORIES AND ATTACHMENTS FOR T H E DELTA 1 3xS" THICK NESS PLANER
SUB - BASE ASSEMBLY
The sub-base assembly consists of four
fine grey cast iron legs which have been
sturdily designed to carry the weight of
the machine. It also consists of a front,
rear and two end panels which are made
from No.
16
gauge sheet steel. This design
not only presents an assembly with mod
ern lines, but also permits accessibility to
all sides of the sub-base for adjusting the
motor and its mounting bracket.
No.
22- 1 02- Sub-Base Assembly.
SAFETY CUTTER HEAD
The durable solid stress-proof steel cutter
head body will give long trouble-free oper
ation. The cutter head is extremely safe in
operation since its knife blades are posi
tively locked in its body. Each knife blade
can be easily adj usted by means of spe-
cial collar adjusting screws which engage
a slot in each end of the knife blade.
PLR-68 -R-Cutter Head, complete with a
matched set of
3
high-speed steel knife
blades, ball bearings and bearing hous
ings, and Hi-Speed worm.
ELECTRICAL STARTERS
Magnetic starters are available with start
and stop-reset push buttons. All electrical
starters available for this machine are open
type (without box enclosure) , operate on
AC current and are for either single or
3
phase motors only.
Please specify the motor horsepower,
phase, voltage, amperage and frequency
when ordering an electrical starter.
No.
49-386 - Magnetic starter for 220 volt
operation, open type (without box en
closure) . with heater coils.
No.
49-387-Magnetic starter for
440
volt
operation, open type (without box en
closure) . with heater coils.
GRINDING ATTACHMENT
The grinding attachment is used to sharp
en the knife blades in the cutter head, or
remove large nicks in the edges of the
knife blades, or grind a new cutting angle
on the knife blades.
This attachment can be easily mounted
to the top of the Delta planer. Included
with this attachment is a positive type
indexing mechanism which permits grind
ing the exact angle on each knife blade
in the cutter head.
No.
22- 1 06 - Grinding Attachment.
23
Summary of Contents for Milwaukee PM-1738
Page 1: ...13x5 INCH DELTA MILWAUKEE 7 7 1M rJ6fiUAKJ PM 1738 ...
Page 2: ......
Page 27: ......
Page 28: ......