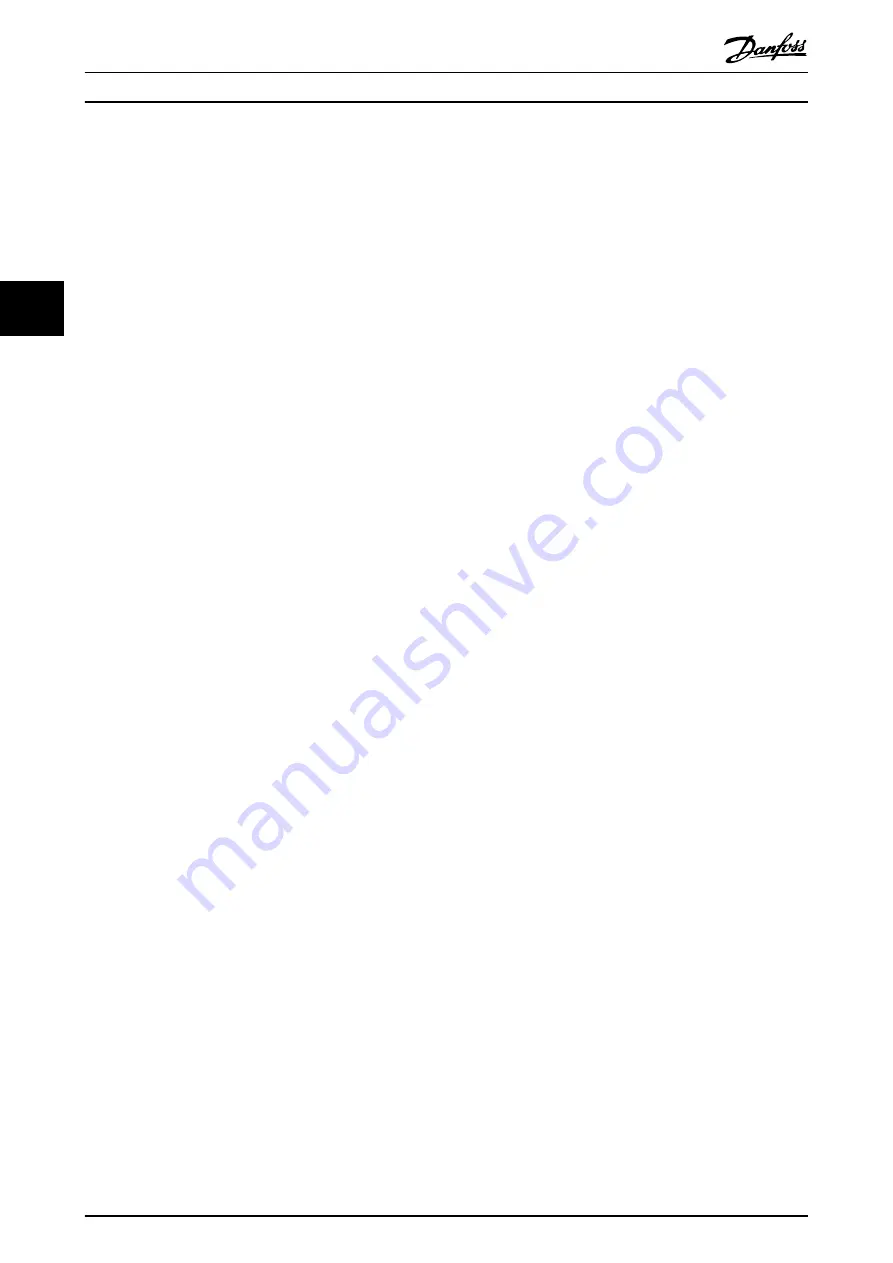
frequency converter makes control decisions by comparing
the two signals to optimise system performance.
4.2.5 Automatic Restart
The frequency converter can be programmed to automat-
ically restart the motor after a minor trip, such as
momentary power loss or fluctuation. This feature
eliminates the need for manual resetting and enhances
automated operation for remotely controlled systems. The
number of restart attempts as well as the duration
between attempts can be limited.
4.2.6 Flying Start
Flying start allows the frequency converter to synchronise
with an operating motor rotating at up to full speed, in
either direction. This prevents trips due to overcurrent
draw. It minimises mechanical stress to the system since
the motor receives no abrupt change in speed when the
frequency converter starts.
4.2.7 Full Torque at Reduced Speed
The frequency converter follows a variable V/Hz curve to
provide full motor torque even at reduced speeds. Full
output torque can coincide with the maximum designed
operating speed of the motor. This is unlike variable
torque converters that provide reduced motor torque at
low speed, or constant torque converters that provide
excess voltage, heat and motor noise at less than full
speed.
4.2.8 Frequency Bypass
In some applications, the system may have operational
speeds that create a mechanical resonance. This can
generate excessive noise and possibly damage mechanical
components in the system. The frequency converter has 4
programmable bypass-frequency bandwidths. These allow
the motor to step over speeds which induce system
resonance.
4.2.9 Motor Preheat
To preheat a motor in a cold or damp environment, a
small amount of DC current can be trickled continuously
into the motor to protect it from condensation and a cold
start. This can eliminate the need for a space heater.
4.2.10 4 Programmable Set-ups
The frequency converter has 4 set-ups which can be
independently programmed. Using multi-setup, it is
possible to switch between independently programmed
functions activated by digital inputs or a serial command.
Independent set-ups are used, for example, to change
references, or for day/night or summer/winter operation, or
to control multiple motors. The active set-up is displayed
on the LCP.
Set-up data can be copied from frequency converter to
frequency converter by downloading the information from
the removable LCP.
4.2.11 Dynamic Braking
Dynamic Brake is established by:
•
Resistor brake
A brake IGBT keeps the overvoltage under a
certain threshold by directing the brake energy
from the motor to the connected brake resistor
(
2-10 Brake Function
= [1]).
•
AC brake
The brake energy is distributed in the motor by
changing the loss conditions in the motor. The
AC brake function cannot be used in applications
with high cycling frequency since this overheats
the motor (
2-10 Brake Function
= [2]).
•
DC brake
An over-modulated DC current added to the AC
current works as an eddy current brake (
2-02 DC
Braking Time
≠
0 s ).
4.2.12 Open Loop Mechanical Brake
Control
Parameters for controlling operation of an electro-
magnetic (mechanical) brake, typically required in hoisting
applications.
To control a mechanical brake, a relay output (relay 01 or
relay 02) or a programmed digital output (terminal 27 or
29) is required. Normally, this output must be closed
during periods when the frequency converter is unable to
‘hold’ the motor, e.g. due to an excessive load. Select
[32]
Mechanical Brake Control
for applications with an electro-
magnetic brake in
5-40 Function Relay
,
5-30 Terminal 27
Digital Output
, or
5-31 Terminal 29 Digital Output
. When
selecting
[32] Mechanical brake control
, the mechanical
brake is closed from start up until the output current is
above the level selected in
2-20 Release Brake Current
.
During stop, the mechanical brake activates when the
speed drops below the level specified in
2-21 Activate
Brake Speed [RPM]
. If the frequency converter enters an
alarm condition or an overcurrent or overvoltage situation,
the mechanical brake immediately cuts in. This is also the
case during Safe Torque Off.
Product Features
VLT
®
AutomationDrive FC 301/FC 302 Design Guide, 0.25-75 kW
40
MG33BF02 - Rev. 2013-12-20
4
4