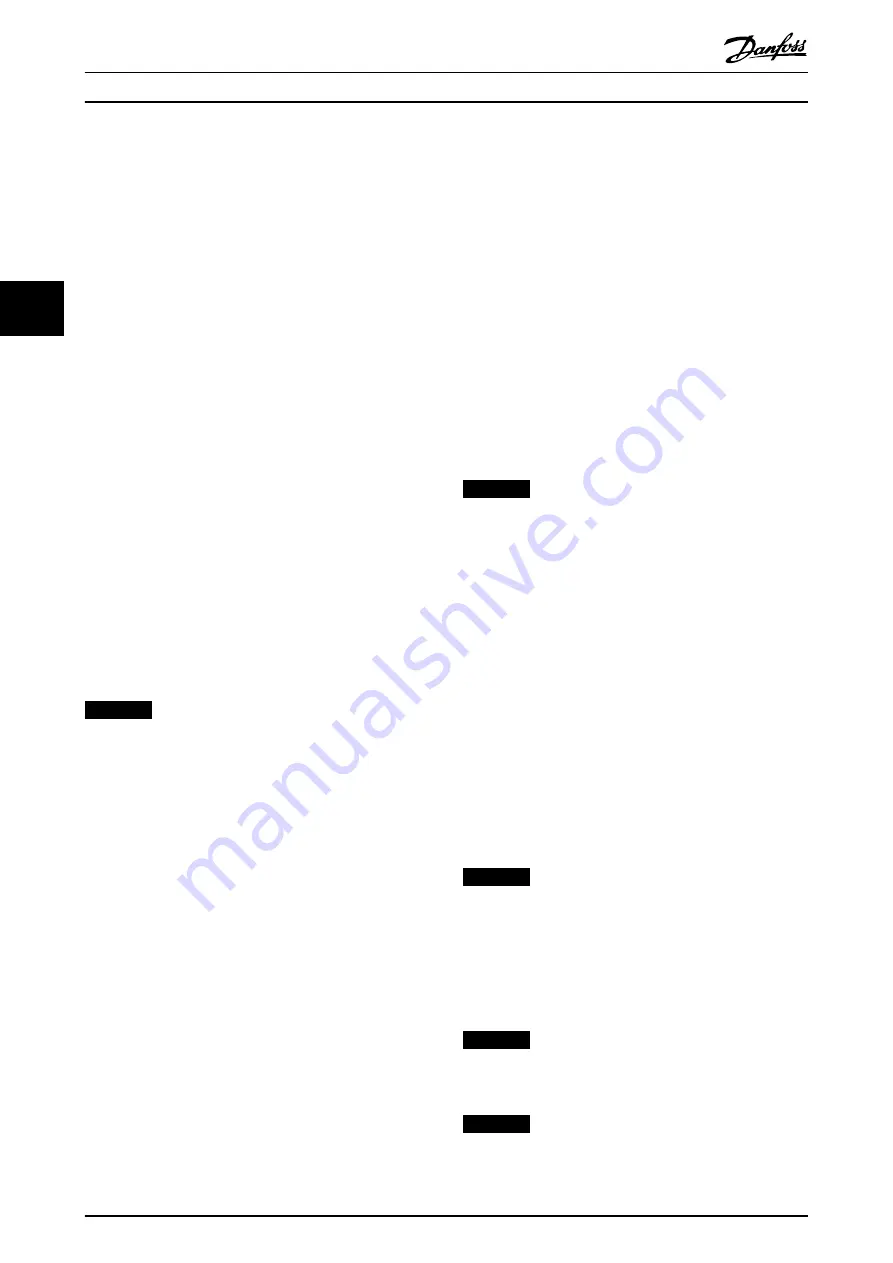
4 Product Features
4.1 Automated Operational Features
These features are active as soon as the frequency
converter is operating. They require no programming or
set up. Understanding that these features are present can
optimise a system design and possibly avoid introducing
redundant components or functionality.
The frequency converter has a range of built-in protection
functions to protect itself and the motor it is running.
4.1.1 Short Circuit Protection
Motor (phase-phase)
The frequency converter is protected against short circuits
on the motor-side by current measurement in each of the
3 motor phases or in the DC-link. A short circuit between 2
output phases causes an overcurrent in the inverter. The
inverter is turned off when the short circuit current
exceeds the permitted value (Alarm 16 Trip Lock).
Mains side
A frequency converter that works correctly limits the
current it can draw from the supply. Still, it is
recommended to use fuses and/or circuit breakers on the
supply side as protection in case of component break-
down inside the frequency converter (first fault). See
for more information.
NOTICE
This is mandatory to ensure compliance with IEC 60364
for CE or NEC 2009 for UL.
Brake resistor
The frequency converter is protected from a short-circuit in
the brake resistor.
Load sharing
To protect the DC bus against short-circuits and the
frequency converters from overload, install DC-fuses in
series with the load sharing terminals of all connected
units. See
for more information.
4.1.2 Overvoltage Protection
Motor-generated overvoltage
The voltage in the intermediate circuit is increased when
the motor acts as a generator. This occurs in following
cases:
•
The load drives the motor (at constant output
frequency from the frequency converter), ie. the
load generates energy.
•
During deceleration (ramp-down) if the moment
of inertia is high, the friction is low and the ramp-
down time is too short for the energy to be
dissipated as a loss in the frequency converter,
the motor and the installation.
•
Incorrect slip compensation setting may cause
higher DC-link voltage.
•
Back-EMF from PM motor operation. If coasted at
high RPM, the PM motor back-EMF may
potentially exceed the maximum voltage
tolerance of the frequency converter and cause
damage. To help prevent this, the value of
4-19 Max Output Frequency
is automatically
limited based on an internal calculation based on
the value of
1-40 Back EMF at 1000 RPM
,
1-25 Motor Nominal Speed
and
1-39 Motor Poles
.
NOTICE
To avoid that the motor overspeeds (e.g. due to
excessive windmilling effects), equip the frequency
converter with a brake resistor.
The overvoltage can handled either via using a brake
function (
2-10 Brake Function
) and/or using overvoltage
control (
2-17 Over-voltage Control
).
Brake functions
Connect a brake resistor for dissipation of surplus brake
energy. Connecting a brake resistor allows a higher DC-link
voltage during braking.
AC brake is an alternative to improve breaking without
using a brake resistor. This function controls an over-
magnetisation of the motor when running generatoric. This
function can improve the OVC. Increasing the electrical
losses in the motor allows the OVC function to increase
the breaking torque without exceeding the overvoltage
limit.
NOTICE
AC brake is not as effective as dynamic breaking with a
resistor.
Over Voltage Control (OVC)
OVC reduces the risk of the frequency converter tripping
due to an overvoltage on the DC-link. This is managed by
automatically extending the ramp-down time.
NOTICE
OVC can be activated for PM motor with all control core,
PM VVC
+
, Flux OL and Flux CL for PM Motors.
NOTICE
Do not enable OVC in hoisting applications.
Product Features
VLT
®
AutomationDrive FC 301/FC 302 Design Guide, 0.25-75 kW
36
MG33BF02 - Rev. 2013-12-20
4
4