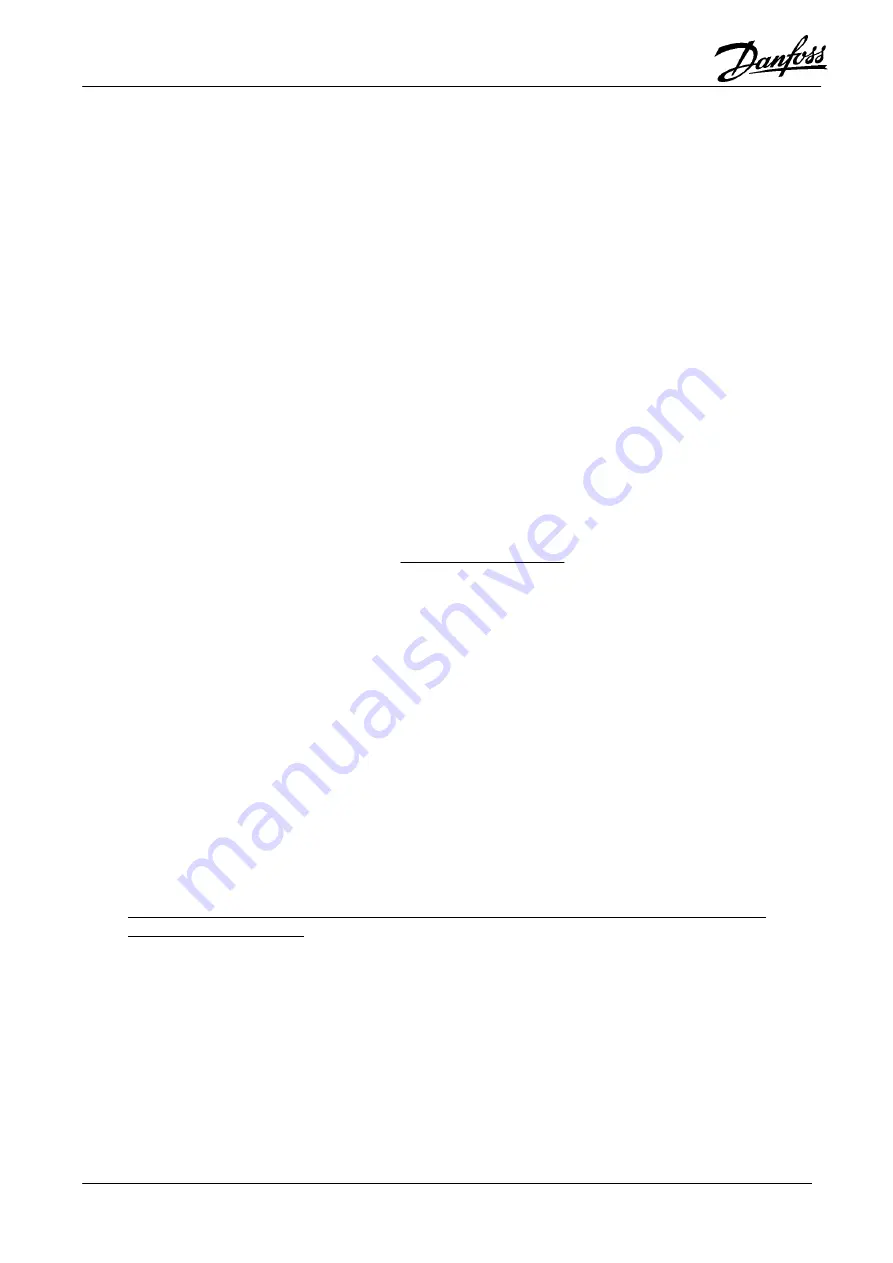
Synchronizing controller
MG.10.N4.02 - VLT is a registered Danfoss trademark
69
Operation and operating functions
After all the values have been set as described, the drive can now be operated normally.
Starting synchronization
Synchronization of the slave is started by means of SyncStart (I1), then the master is started.
This ensures optimum synchronization. The slave drive travels in position synchronization to the
master until both slave and master marker has been detected. The slave accelerates or slows
down, according to the setting of Parameter 732, in order to attain the marker position plus the
set offset. It may happen that the slave drive travels faster than the master does, if the slave
drive needs to catch up with the position.
Stopping synchronization
On opening contact I1 (SyncStart), the slave is stopped at the permitted acceleration.
Fine setting of the position
As soon as the slave drive is in position synchronization to the master, an adjustment of this
position can be made by means of Inputs 32 + 33. This setting is only temporary, i.e. the fine-
setting data are lost as soon as the converter is disconnected from the mains. If the adjustment
data are to be retained, storage must be carried out by activating the Save Input (I4) or by
means of Parameter 710 before switching off the drive.
Note: Offset is related to the master position. Offset related to the slave position can be
calculated as follows:
Offset_slave
=
739
738
*
Parameter
Parameter
Offset
Switching to another gear ratio
During synchronization, a new gear ratio can be selected at Inputs 16 and 17. The gear ratio is
then activated by means of the Switching Input (I2). The slave will then proceed at the permitted
acceleration to this new gear ratio. The offset is related to the first gear ratio after SyncStart.
Therefore a stop and then start must be performed if the offset must relate to the latest gear
ratio it the gear ratio has been changed.
Error procedure
Errors of tracking, over current etc. make the drive stop and the Ready output (O8) is set low.
Reset is done with Input 27 or fieldbus bit 1.9.
Reset is also possible with the [STOP/RESET] key of the local control panel of the drive. This is
only possible if the local stop function is disabled in parameter 014.
Note: You cannot stop the drive via the local control panel if local stop is disabled.
In case the drive has stopped because of earth fault or short-circuit, disconnect the drive from
the mains before you reset!