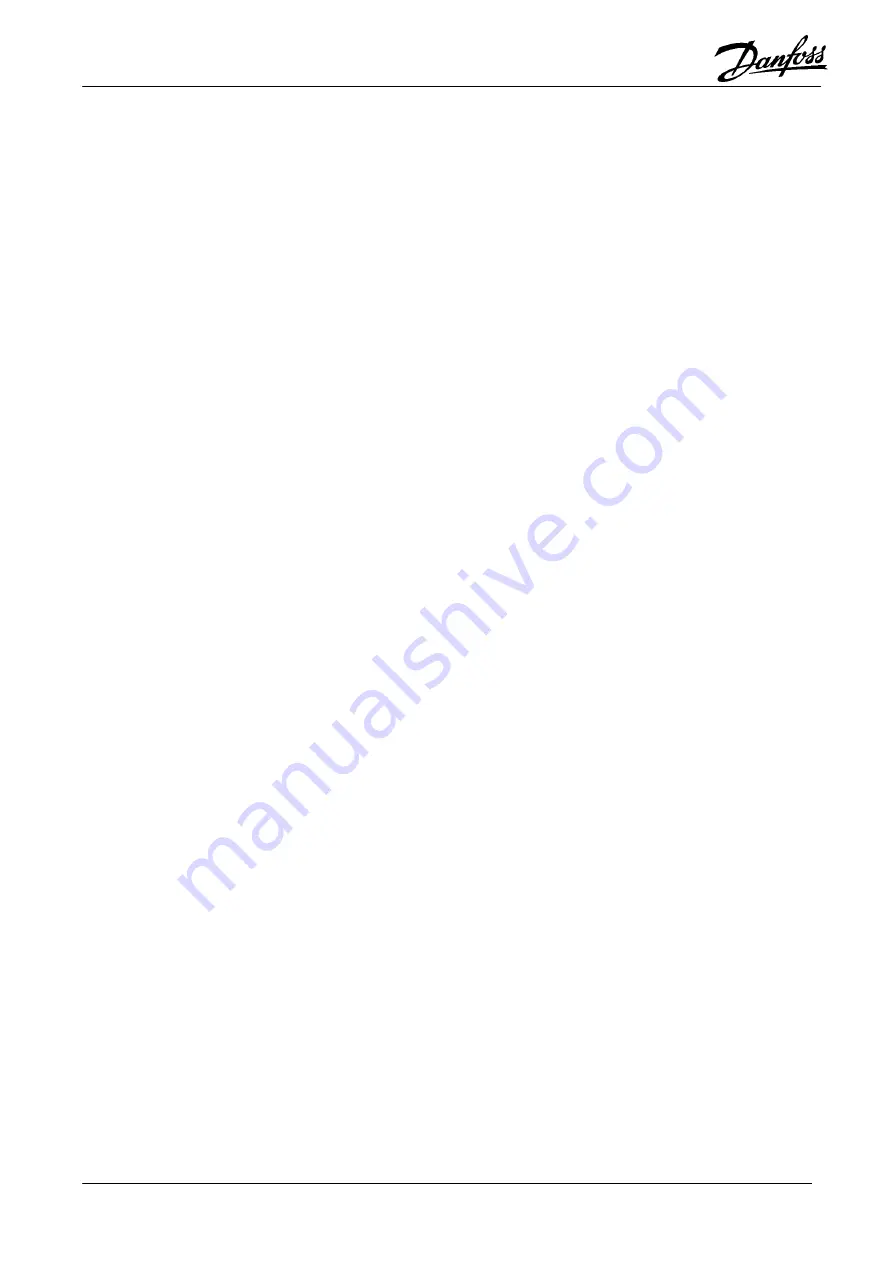
Synchronizing controller
MG.10.N4.02 - VLT is a registered Danfoss trademark
45
How to optimize the controller:
Synchronization is obtained via two main elements of the controller: Velocity feed forward and
the PID controller.
NOTE: Before starting the optimizing procedures it is important to select the right type of
synchronization in parameter 728, in this example it must be “0” for velocity synchronization.
Please always have the necessary degree of accuracy in mind, you could go on optimizing for a
long time, but it might not be necessary to have a 100% accuracy in the application you are
dealing with.
First step is to optimize velocity feed forward this can be done via the automatic calculation
function:
Velocity feed forward calculation is activated by setting parameter 729 to “1”, remember to
make the required parameter settings according to the description of par. 729 before starting
the calculation. The calculation is done when the value of par. 729 returns to “0”.
Velocity feed forward can also be optimized manually by the following procedure:
1. Set parameter 706 PID bandwidth to “0”.
2. Set parameter 719 maximum track error to a high value (e.g. 1,000,000).
3. Set parameter 707 velocity feed forward to 100.
4. Start test-run with virtual master with a known velocity via input 3 = 1.
5. Increase parameter 707 while watching master and slave velocity (press
[DISPLAY/STATUS] to get the velocity readouts). You have found the optimal velocity
feed forward when slave velocity is approximately equal to the master velocity.
6. Stop test-run by input 3 = 0.
7. Reset parameter 719 to the original value.
8. Reset parameter 706 to 1000.
Second step is to optimize the PID controller, a good starting point can be found be means of
the automatic calculation function:
By setting parameter 729 to “2” velocity feed forward calculation is activated as well as
calculation of PID sample time and P/D factors, remember to make the required parameter
settings according to the description of par. 729 before starting the calculation. The
calculation is done when the value of par. 729 returns to “0”.
Using the test run functions can optimize the PID factors further:
There is two types of test run available: Positioning where the slave drive moves a specific
distance and Synchronizing with virtual master where the slave follows the virtual master in
position or speed. Generally it is better to use test run with virtual master as that comes
closer to the operating conditions in synchronizing mode (program 2).
For test run with positioning the following parameters must be set:
Parameter 725 Test run speed: Record the speed as a percentage of the maximum speed
of parameter 716.
Parameter 726 Test run acceleration: record the acceleration time in per cent. 100% is
minimum acceleration. 50% is half as fast as minimum acceleration, the
ramp time will thus be twice as long.
Parameter 727 Test run distance: Record the distance (quad counts) for the drive to run
during optimization.