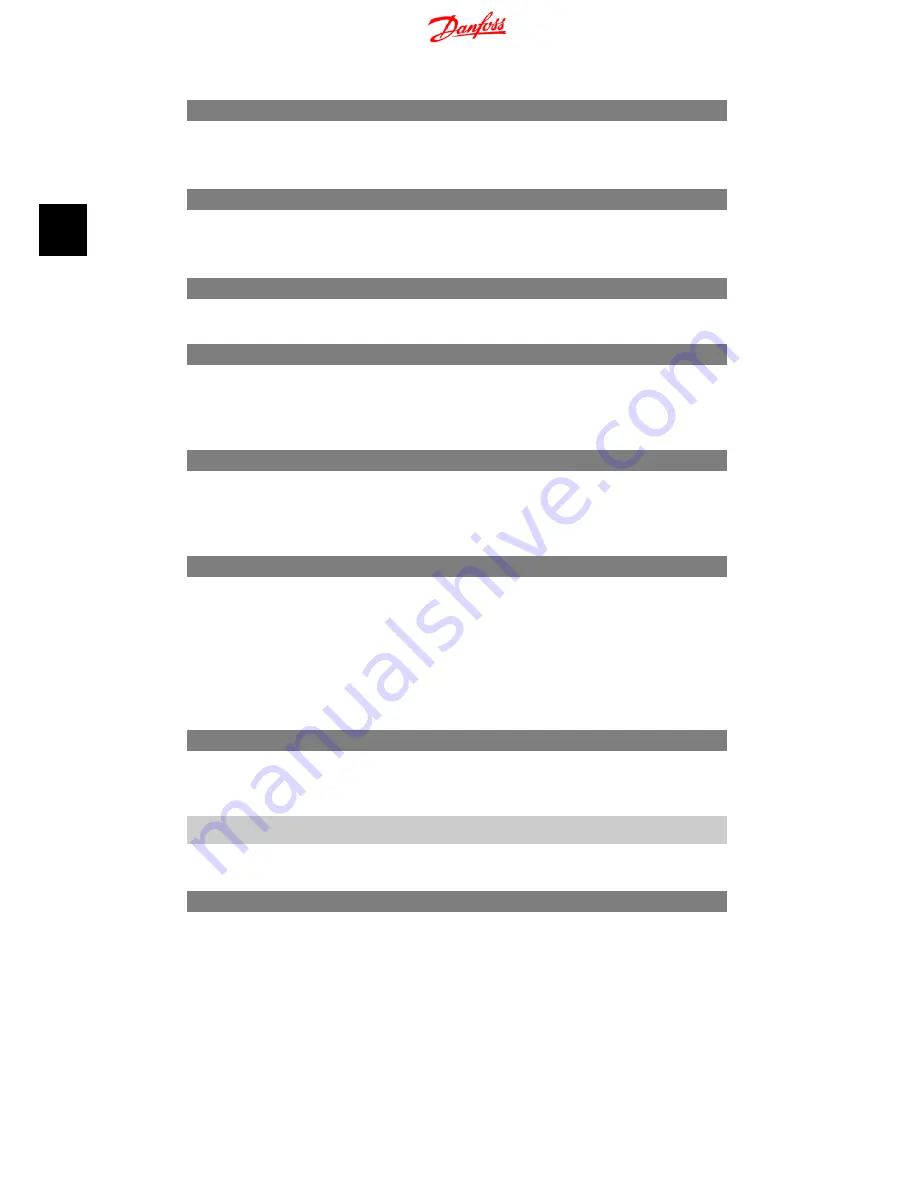
32-62 I-portion of the synchronising controller
Option:
Function:
Setting: see Examples.
32-63 Limitation for I-portion
Option:
Function:
Setting: see Examples.
32-64 Band width for PID controller
Option:
Function:
32-65 Velocity feed forward
Option:
Function:
Setting: see Examples.
32-66 Acceleration feed forward
Option:
Function:
Setting: see Examples.
32-67 Maximum track error
Option:
Function:
Enter here the maximum track error. This is the permitted error
between the calculated position and the feedback position. If
the value is exceeded, the drive stops and displays the error
message: O.ERR_108 “Position error“. The value should be set
higher than the permitted tolerance range ACCURACY in par.
33-13. Input in quad counts.
32-68 Reversing behaviour
Option:
Function:
[0]
means that the slave drive may always reverse, e.g. after over-
shooting the target position.
[1]
the slave drive may only reverse when the master is reversing.
[2]
the slave drive may never reverse.
32-69 PID-sample time
Option:
Function:
The parameter is setting the sample time of the control algo-
rithm. The value should be increased if:
•
The pulse frequency is very low, e.g. 1 to 2 quad
counts per sample time (you need at least 10 to 20
quad counts per sample time).
3. Programming
Syncronising Controller MCO 350 Operating
Instructions
38
MG.33.Q1.02 - VLT
®
is a registered Danfoss trademark
3