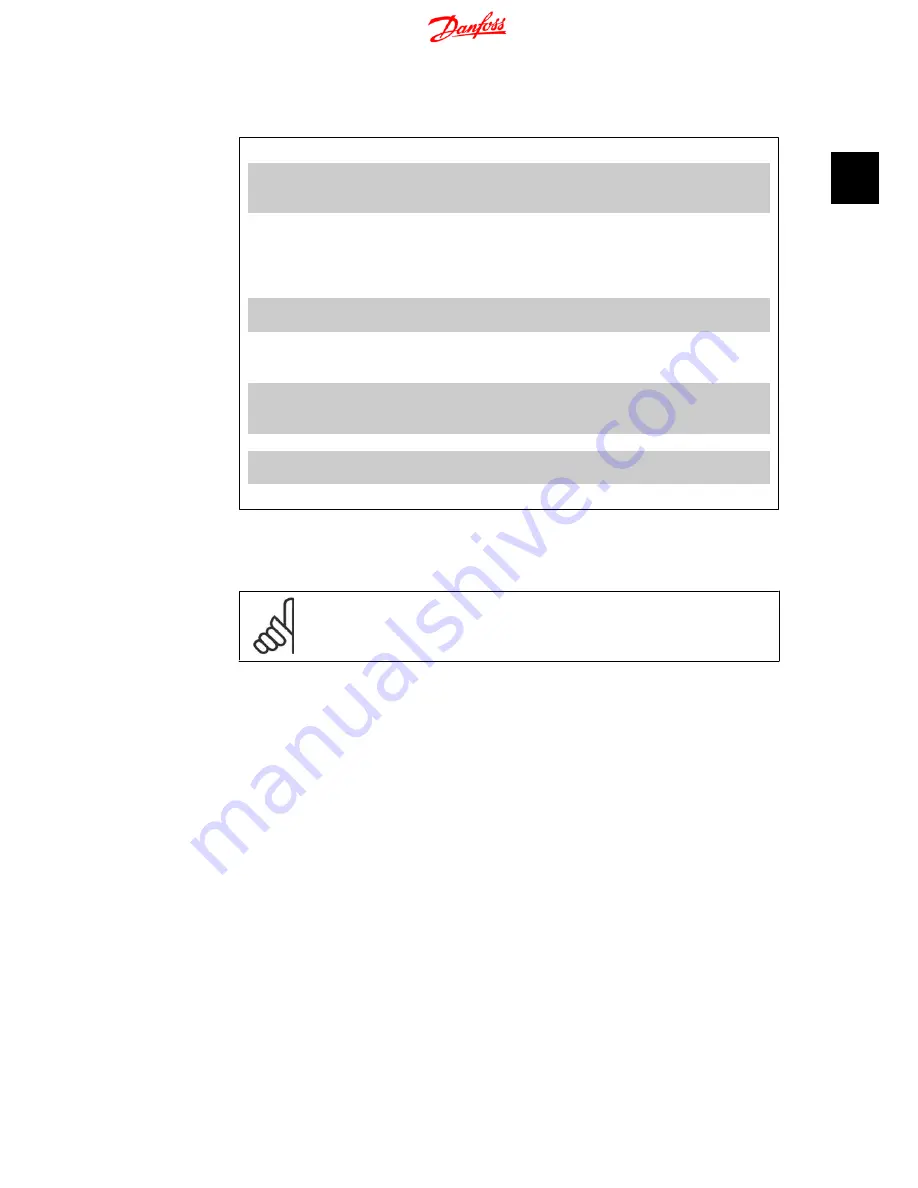
2.7.3. MCO 350 Terminal X59
I/O Number Designation
Description
1
O1 - READY
Ready, i.e. for the number of marker signals that were
specified in Parameter 3325, the slave drive has run
within the tolerance (Accuracy).
2
O2 - FAULT
Fault, i.e. for the number of marker signals that were
specified in Parameter 3324, the slave drive has run out-
side the tolerance (Accuracy). OR when the number of
marker signals have been missing when marker monitor
is activated in parameter 1923.
3
O3 - ACCURACY
The drive runs within the tolerance specified in Param-
eter 3313.
4
O4 - Brake control
This output can be used to control a mechanical brake.
“0” means that the brake must be closed (braking) “1”
means that the brake must be open (not braking)
5
O5 - Saving
This output stays high while saving is in progress. The
saving is initiated by Parameter 1900, Input 4 or fieldbus
bit 4.
6
O6 - Drive running
Signal “1” when the drive is running.
7
O7 - Home reached If the data value “1” was chosen in Parameter 3300, this
output shows “1” when homing is completed.
8
O8 - Ready, no error The synchronising controller is ready for operation.
2.8. Description of Fieldbus Interface
NB!
This section is only relevant if the VLT is equipped with a Field bus interface (option)
as well as the synchronising controller.
The synchronising controller can be controlled via the digital/analogue inputs or via field bus. The
control source can be selected individually for test-run and synchronising in the parameters 1919
(test-run) and 1920 (synchronising). There can only be one control source at a time meaning that
the digital/analogue inputs are inactive when Field bus is selected as control source and visa versa.
The only exception is input 27, which is always stop/enable also when Field bus is selected as
control source. In synchronising mode three signals are only available as digital inputs even when
Field bus is selected as control source that is the marker signals for marker synchronisation and
the Home switch. This is because these signals are too time-critical for Field bus control. Status
signals are always available on the digital/analogue outputs but they are only available via Field
bus when Field bus is selected as control source.
2.8.1. Data Layout
Control and status signals are transferred via the so-called process data channel (PCD) of the
various fieldbus interfaces. The telegram structure and the available number of data words de-
pends on the Fieldbus used, please refer to the manual of the Fieldbus option in use for further
details. The below example is based on the layout of a PROFIBUS telegram, the so-called PPO:
Example using PROFIBUS PPO type 5:
Syncronising Controller MCO 350 Operating
Instructions
2. Introduction
MG.33.Q1.02 - VLT
®
is a registered Danfoss trademark
23
2