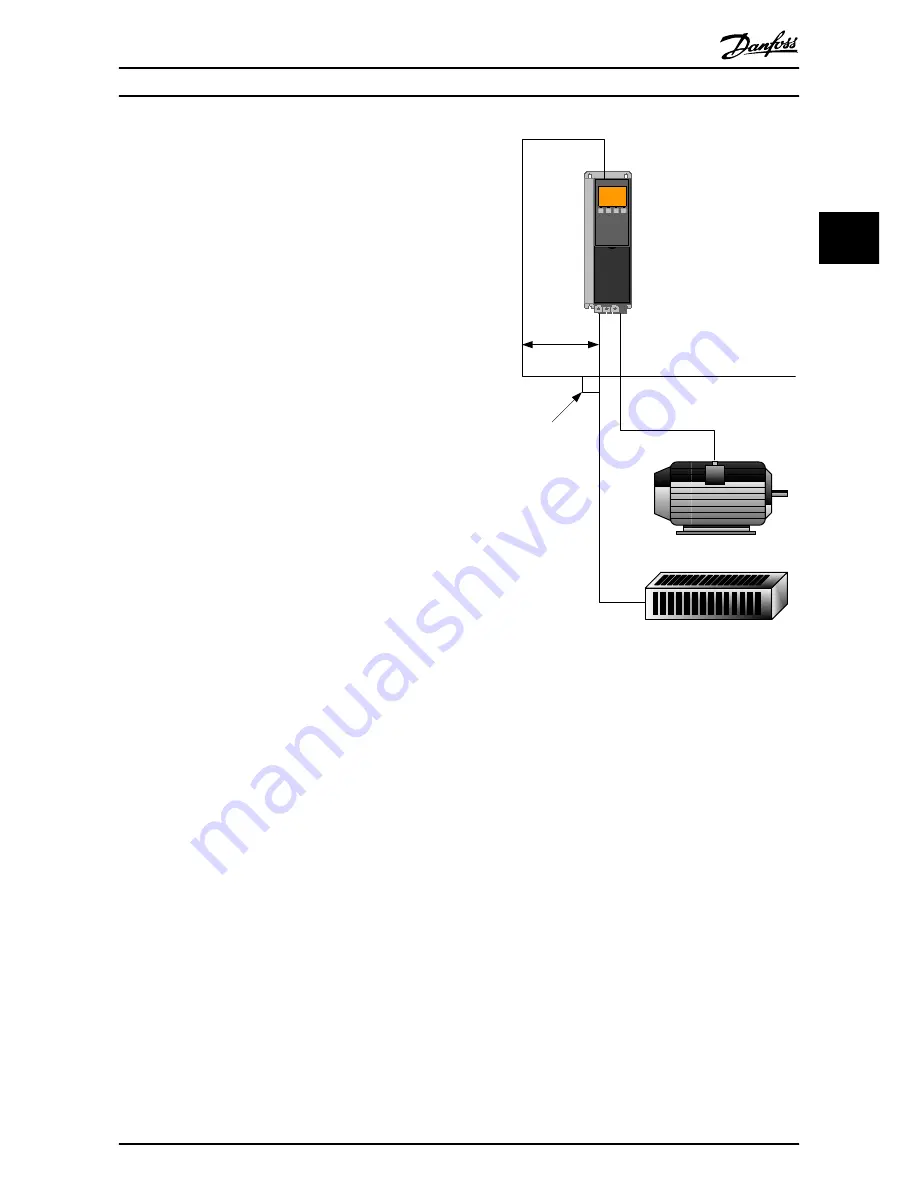
recommended, especially where cables run in
parallel, over long distances, or if drives with a
bigger power size is installed. More information
can be found in the norm IEC 61000-5-2:1997.
4.
When crossing of cables is unavoidable, the
Ethernet cable must cross motor and brake
resistor cables at an angle of 90
°
.
5.
Always observe relevant national and local
regulations, for example regarding protective
earth connection.
NOTE
In a line topology all frequency converters must be
powered, either by mains or by their 24 V DC option cards,
for the built-in POWERLINK slave controller to work.
2.1.6 EMC Precautions
To achieve interference-free operation of the Ethernet,
observe the following EMC precautions. Additional EMC
information is available in the
VLT
®
AutomationDrive Design
Guide.
NOTE
The correct handling of the shield of the motor cable is
vital for the overall performance of the system. If the rules
are not followed it can lead to loss of the control and
malfunction of the system.
NOTE
Always observe relevant national and local regulations, for
example regarding protective earth connection.
The Ethernet communication cable must be kept away
from motor and brake resistor cables to avoid coupling of
high frequency noise between the cables. When crossing is
unavoidable, the Ethernet cable must cross motor and
brake resistor cables at an angle of 90
°
.
min. 200 mm
90 ° crossing
Ethernet Cable
130BA908.11
Illustration 2.5 Correct Crossing of Ethernet Cable
How to Install
MCA 123 POWERLINK Operating Instructions
MG92C102 - VLT
®
is a registered Danfoss trademark
9
2
2