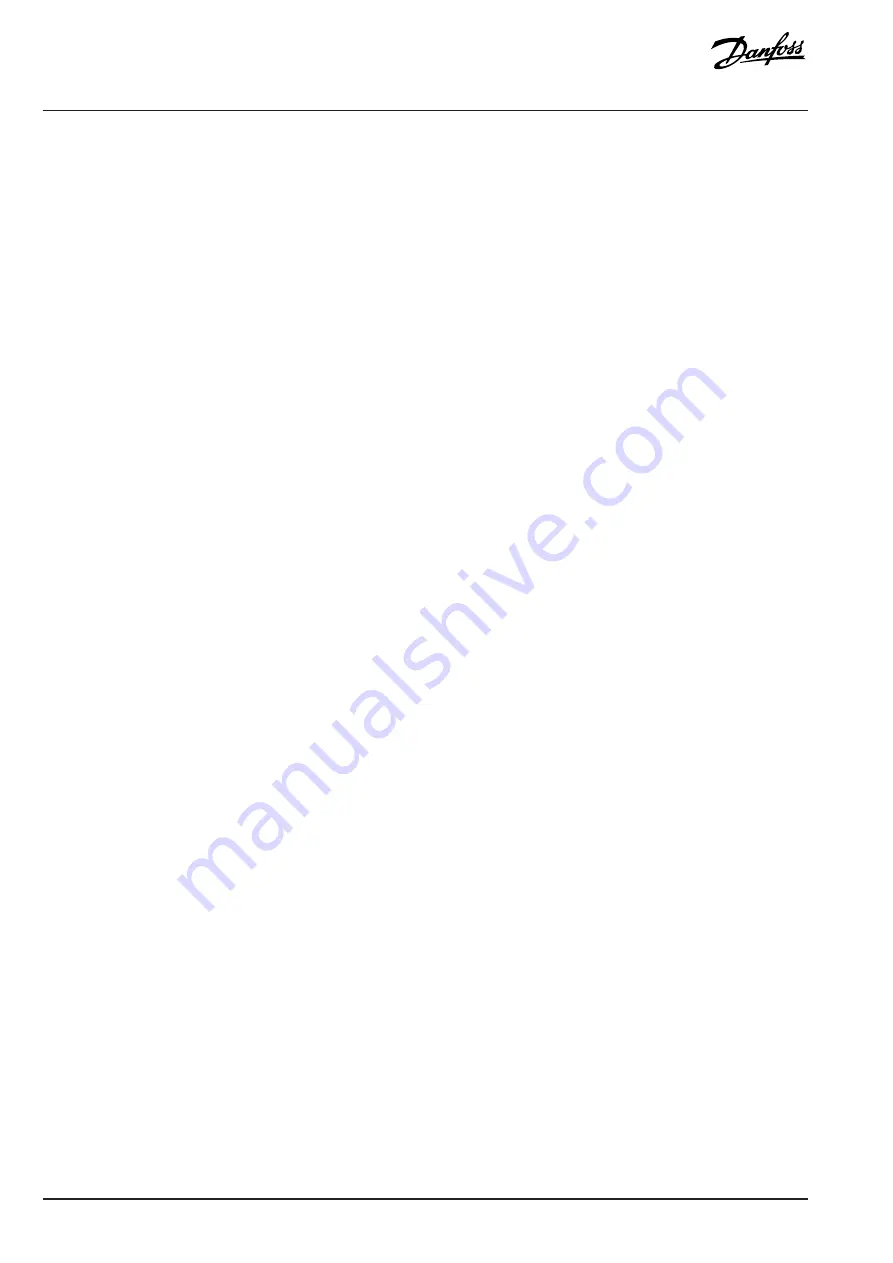
Process controller
The process controller can control a process, for example, in a system where a constant pressure, flow, or temperature is needed.
Feedback from the application is connected to the drive, providing the actual output value. The controller ensures that the output is
matching the reference provided by controlling the motor speed. The reference source and the feedback signals are converted and
scaled to the actual values controlled.
Speed controller
The open-loop speed control provides accurate control of the motors rotational speed.
In open-loop mode (without external feedback signal of the speed), there is no need for external sensors. The open-loop speed control
makes installation and commissioning easier, and eliminates the risk of defective sensors.
Torque controller
A built-in torque controller provides optimized control of torque and supports open-loop control.
2.3
IO Control and Readouts
Depending on the hardware configuration of the drive, digital and analog inputs, digital and analog outputs, and relay outputs are
available. The I/Os can be configured and used to control the application from the drive.
All I/Os can be used as remote I/O nodes, as they are all addressed by the fieldbus of the drive.
2.4
Motor Control Features
2.4.1
Motor Control Features Overview
The motor control covers a wide range of applications, control from the most basic applications to applications requiring high-
performance motor control.
2.4.2
Motor Types
The drive supports standard available motors like:
l
Induction motors
l
Permanent magnet motors
2.4.3
Load Characterstics
Different load characteristics are supported to match the actual application needs:
l
Variable torque:
Typical load characteristic of fans and centrifugal pumps, where the load is proportional to the square of the speed.
l
Constant torque:
Load characteristic used in machinery where torque is needed across the full speed range. Typical application
examples are conveyors, extruders, decanters, compressors, and winches.
2.4.4
Motor Control Principle
Different control principles can be selected to control the motor, matching the application needs:
l
U/f control for special control
l
VVC+ control for the general-purpose application needs
2.4.5
Motor Nameplate and Catalog
Typical motor data for the actual drive are preset from factory, allowing operation of most motors. During commissioning, actual motor
data are entered in the settings of the drive, optimizing the motor control.
16
| Danfoss A/S © 2024.03 AB413939445838en-000301 / 130R1254
Application Guide | iC2-Micro Frequency Converters
Summary of Contents for iC2
Page 1: ...iC2 Micro Frequency Converters Application Guide drives danfoss com...
Page 2: ......
Page 291: ......