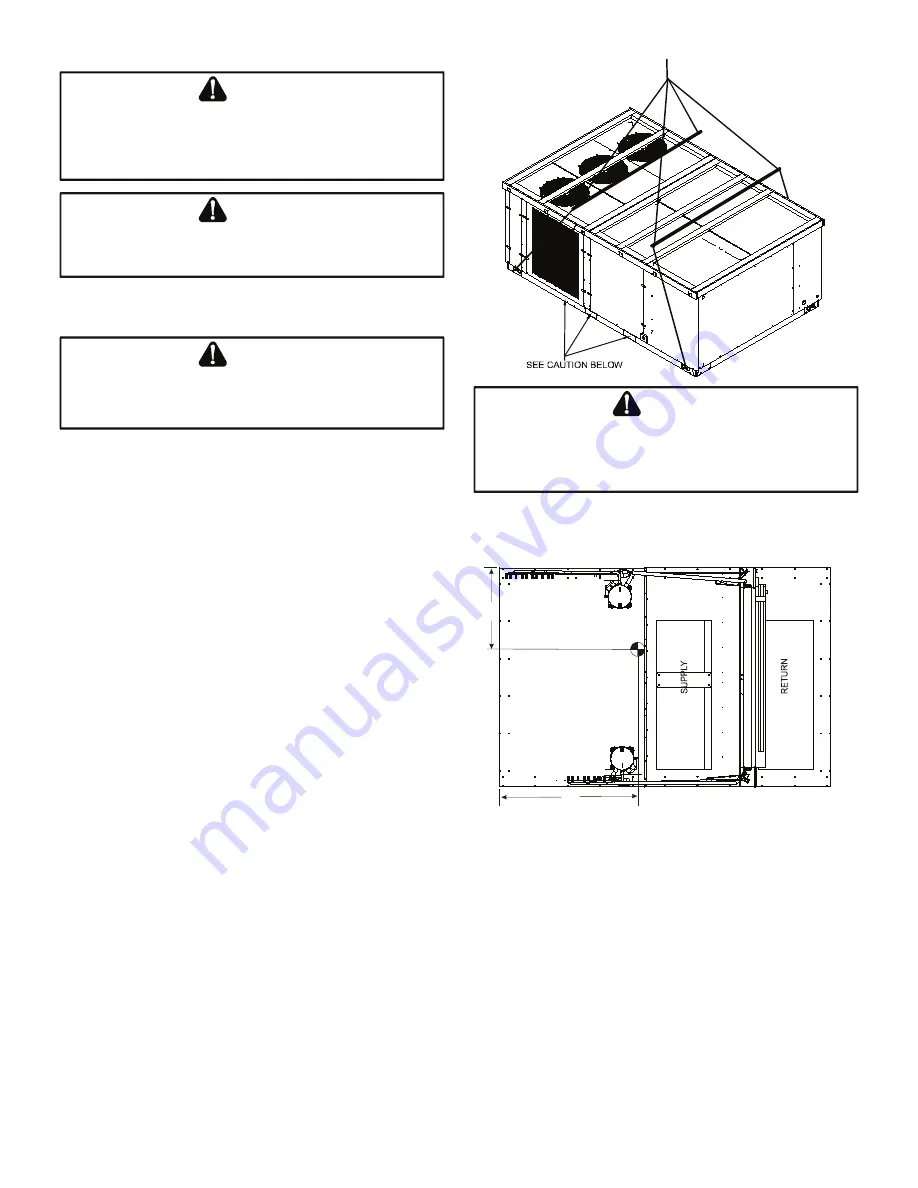
7
RIGGING DETAILS
T
O
PREVENT
PROPERTY
DAMAGE
,
THE
UNIT
SHOULD
REMAIN
IN
AN
UPRIGHT
POSITION
DURING
ALL
RIGGING
AND
MOVING
OPERATIONS
.
T
O
FACILITATE
LIFTING
AND
MOVING
WHEN
A
CRANE
IS
USED
,
PLACE
THE
UNIT
IN
AN
ADEQUATE
CABLE
SLING
.
WARNING
D
O
NOT
LIFT
UNITS
TWO
AT
A
TIME
. P
ROVISIONS
FOR
FORKS
HAVE
BEEN
INCLUDED
IN
THE
UNIT
BASE
FRAME
. M
INIMUM
FORK
LENGTH
IS
72”
TO
PREVENT
DAMAGE
TO
THE
UNIT
.
CAUTION
Provisions for forks have been included in the unit base frame. No
other fork locations are approved.
T
O
PREVENT
POSSIBLE
EQUIPMENT
DAMAGE
,
PROPERTY
DAMAGE
,
PERSONAL
INJURY
OR
DEATH
,
THE
FOLLOWING
BULLET
POINTS
MUST
BE
OBSERVED
WHEN
INSTALLING
THE
UNIT
.
WARNING
• Unit must be lifted by the four lifting holes located at the
base frame corners.
• Lifting cables should be attached to the unit with shackles.
• The distance between the crane hook and the top of the
unit must not be less than 60”.
• Two spreader bars must span over the unit to prevent
damage to the cabinet by the lift cables. Spreader bars
must be of sufficient length so that cables do not come
in contact with the unit during transport. Remove wood
struts mounted beneath unit base frame before setting unit
on roof curb. These struts are intended to protect unit
base frame from fork lift damage. Removal is accomplished
by extracting the sheet metal retainers and pulling the
struts through the base of the unit. Refer to rigging label
on the unit.
Important:
If using bottom discharge with roof curb, ductwork
should be attached to the curb prior to installing the unit. Ductwork
dimensions are shown in Roof Curb Installation Instructions.
Refer to the Roof Curb Installation Instructions for proper curb
installation. Curbing must be installed in compliance with the Na-
tional Roofing Contractors Association Manual.
Lower unit carefully onto roof mounting curb. While rigging unit,
center of gravity will cause condenser end to be lower than supply
air end.
W
HEN
UNIT
IS
SUSPENDED
,
BOARDS
AND
SHIPPING
BRACE
WILL
DROP
WHEN
SCREWS
ARE
REMOVED
. T
O
PREVENT
PERSONAL
INJURY
, STAND CLEAR.
R
EMOVE
FORK
HOLE
BRACKETS
,
BOARDS
AND
SHIPPING
BRACE
FROM
BOTTOM
OF
UNIT
BEFORE
PLACING
UNIT
ONTO
CURB
.
CAUTION
To assist in determining rigging requirements, unit weights are
shown as follows:
COMPRESSOR 1
COMPRESSOR 2
CG
EV
AP
O
R
AT
O
R
C
O
IL
S
A
B
C
X
D
Y
CORNER & CENTER OF GRAVITY LOCATIONS