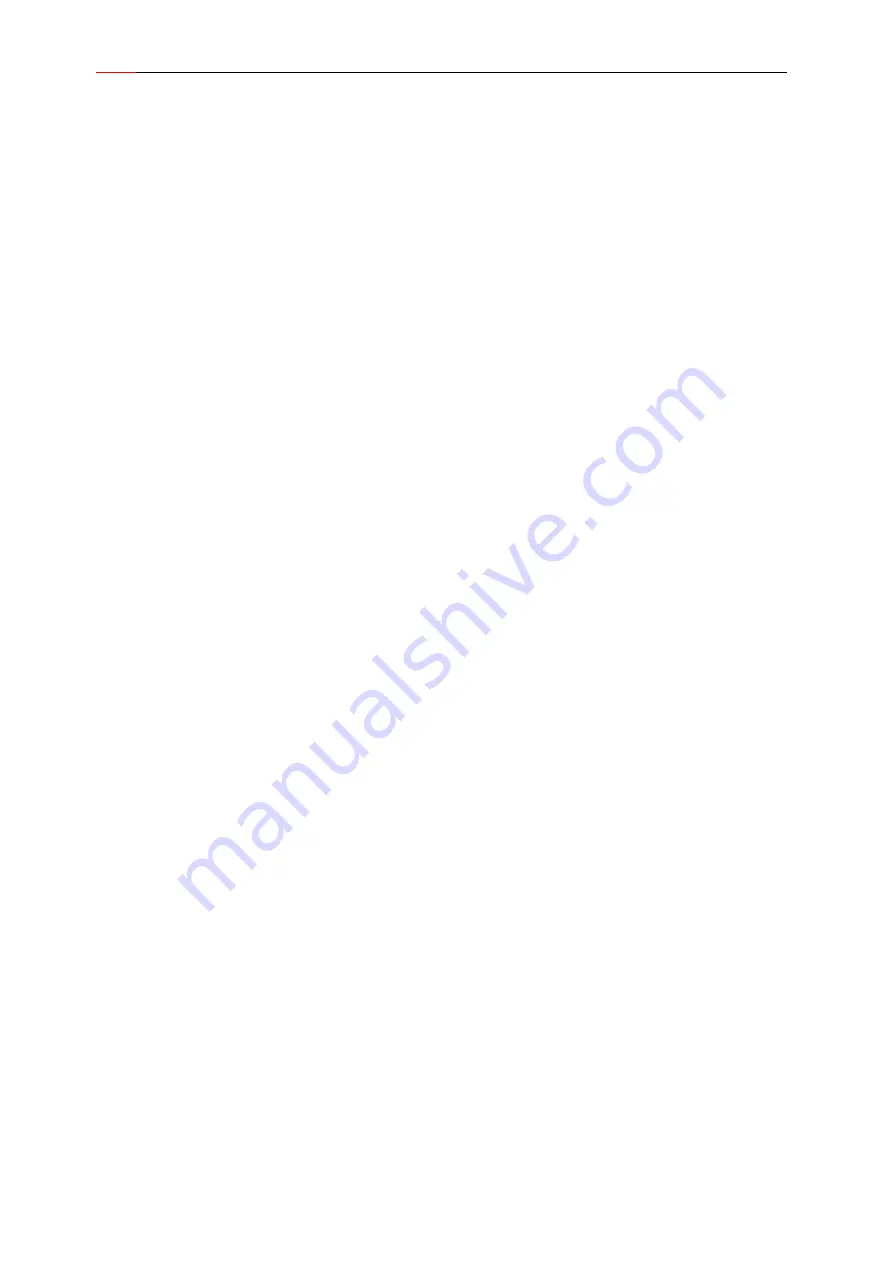
Cynko
Met
N-233
1
CynkoMet Sp. z o.o.
ul. Fabryczna 7W
16-
020 Czarna Białostocka
phone (085) 710 24 56
MANURE SPREADER
series
N-235
Type: 1, 2, 6, 7, 8
INSTRUCTIONS FOR USE AND OPERATION
Identification of the machine
Symbol/Type:
N-
235/……………..…..
Serial number:
…………………………….
The serial number is stamped on the nameplate and on the front beam of
the upper frame of the machine. The rating plate is riveted to the front
beam of the upper frame.
When buying the machine, check the conformity of the serial numbers
stamped on the spreader with the serial number written in the warranty
card, in the sales documents and in the instruction manual.
NOTE!
The manufacturer reserves the right to introduce, in the manufactured
machines, structural alterations facilitating servicing and improving the
quality of their work. The information on significant design changes are
communicated to the user by means of enclosed information (annexes).
Summary of Contents for N-235 Series
Page 33: ...CynkoMet N 233 33 2 1 2 4 5 3A 3B ...
Page 59: ...CynkoMet N 233 59 Figure 12 Mounted guard ...
Page 64: ...CynkoMet N 233 64 ...
Page 79: ...CynkoMet N 233 79 PARTS CATALOGUE ...
Page 81: ...CynkoMet N 233 81 Tab 1 ...
Page 83: ...CynkoMet N 233 83 Table 2 Walls 500 Model N 233 4 ...
Page 86: ...CynkoMet N 233 86 ...
Page 88: ...CynkoMet N 233 88 ...
Page 94: ...CynkoMet N 233 94 Table 9 Conveyor drive ...
Page 96: ...CynkoMet N 233 96 ...
Page 100: ...CynkoMet N 233 100 Table 11 Adapter A2HS ...
Page 102: ...CynkoMet N 233 102 Table 12 Spreader of adapter A2HS ...
Page 104: ...CynkoMet N 233 104 Table 13 Adapter A4VS P ...
Page 106: ...CynkoMet N 233 106 Table 14 A4VS P drum ...
Page 108: ...CynkoMet N 233 108 Table 15 Conveyor ...
Page 110: ...CynkoMet N 233 110 Table 16 Electrical installation ...
Page 111: ...CynkoMet N 233 111 ...
Page 113: ...CynkoMet N 233 113 Table 17 1 hose pneumatic brake system ...
Page 115: ...CynkoMet N 233 115 Table 18 Hydraulic wall ...
Page 117: ...CynkoMet N 233 117 Table 19 Hydraulic installation for wall ...
Page 118: ...CynkoMet N 233 118 ...
Page 120: ...CynkoMet N 233 120 Table 20 Drum guard set ...
Page 122: ...CynkoMet N 233 122 NOTES NOTES ...
Page 123: ...CynkoMet N 233 123 NOTES ...
Page 124: ...CynkoMet N 233 124 ...