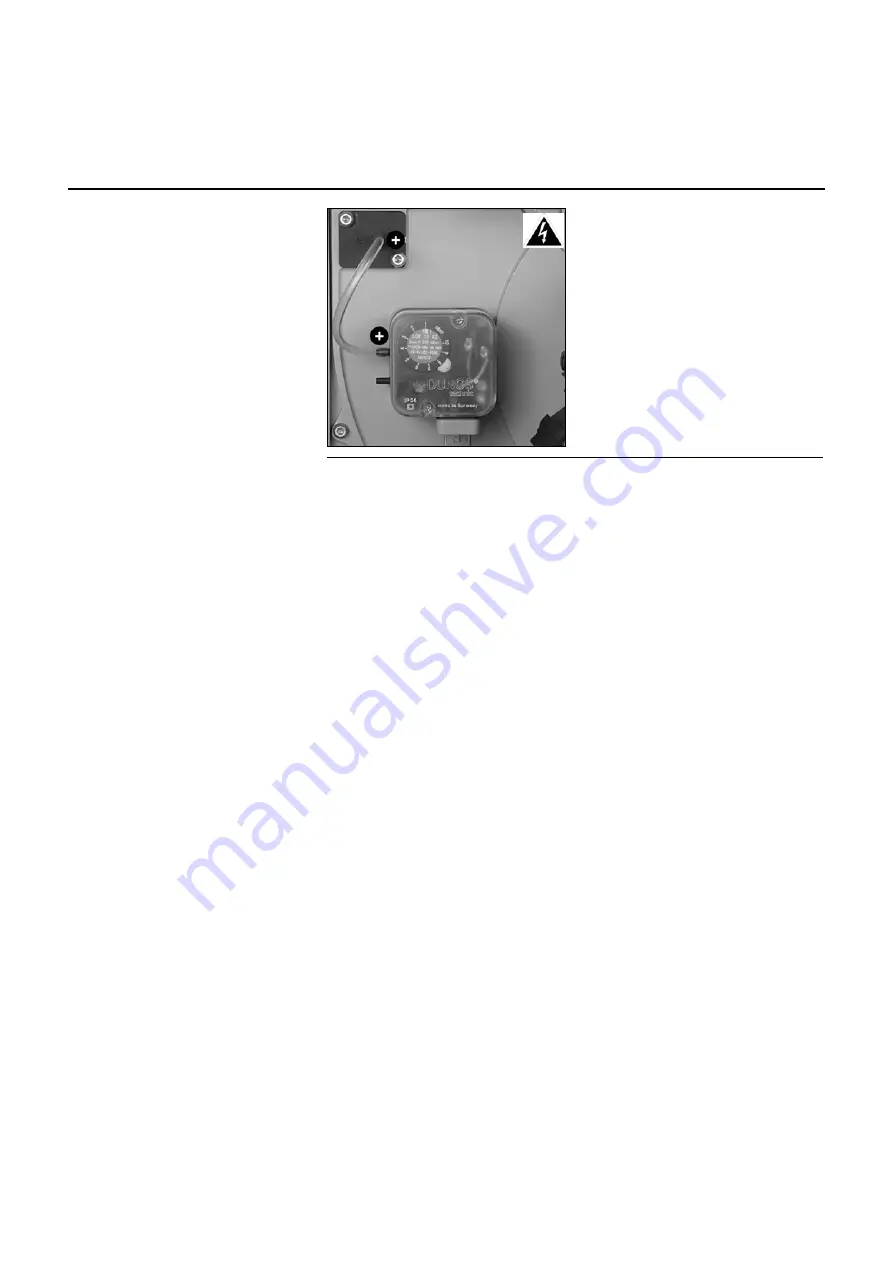
03/2008 - Art. Nr. 13 013 477C
6
Setting air pressure switch
• Check flexible hose connection
(pressure take-off
+
to pressure switch
+
). The other pressure take-off must
remain open.
• Remove transparent cover. Unit
includes a
↑ | ↓
index and graduated
mobile disk.
• Provisionally set switch to the
minimum value shown on graduated
disk.
Start-up
Preliminary check-up and leakage test
Setting air pressure switch
Burner start up simultaneously involves
starting up installation by the fitter or his
representative; only they can guarantee
boiler house compliance with currently
accepted practices and regulations in
force.
The fitter must first be in possession of a
“ certificate of gas fuel conformity ”
issued either by the approved body or
distributor and also have leak-tested and
drained pipework upstream from the ball
valve.
Preliminary checks
• Check the following:
- nominal available voltage and
electrical frequency and compare
them with values found on
identification plate,
- polarity between phase and neutral
- previously tested earth wire
connection,
- lack of potential between neutral and
earth,
- motor rotation direction
- thermal relay
only in manual (H)
position and intensity setting.
• Cut off electrical supply.
• Make sure there is no current.
• Close fuel valve.
• Read boiler and regulator
manufacturer service instructions.
• Check the following:
- boiler is full of pressurized water,
- circulator(s) work(s),
- mixing valve(s) open,
- combustion air supply to the boiler
house and combustion product
exhaust pipe are working correctly
and compatible with burner capacity
and fuel,
- draught operator working correctly
on exhaust pipe,
- electrical protection equipment
outside burner are present,
calibrated and set,
- boiler regulator circuit is set.
- gas type and distribution pressure
are suited to the burner.
Leakage test
• Connect manometer upstream from
the gas train.
• Open and close the ball valve.
• Check supply pressure and its
long-term stability.
• Use a purpose designed foam to
check tightness of gas train
connections, including external filter.
No leakage should be detected
.
• Drain pipework downstream from the
ball valve whilst taking care to protect
the gas valve intake.
• Reclose drain valve, remove
manometer, close pressure take-off.
Summary of Contents for C120 GX507/8
Page 40: ...03 2008 Art Nr 13 013 477C 40 1 pF VGD SKP 180 SKP 3 SKP 180 F D...
Page 42: ...03 2008 Art Nr 13 013 477C 42...
Page 44: ...03 2008 Art Nr 13 013 477C 44 5 1 1 6 F 5 6 5 0 5 3 1 3 6 5 6 3 0 3...
Page 54: ...03 2008 Art Nr 13 013 477C 54 D 1 RTC 2 J1 1 RTC 1 pF 2...