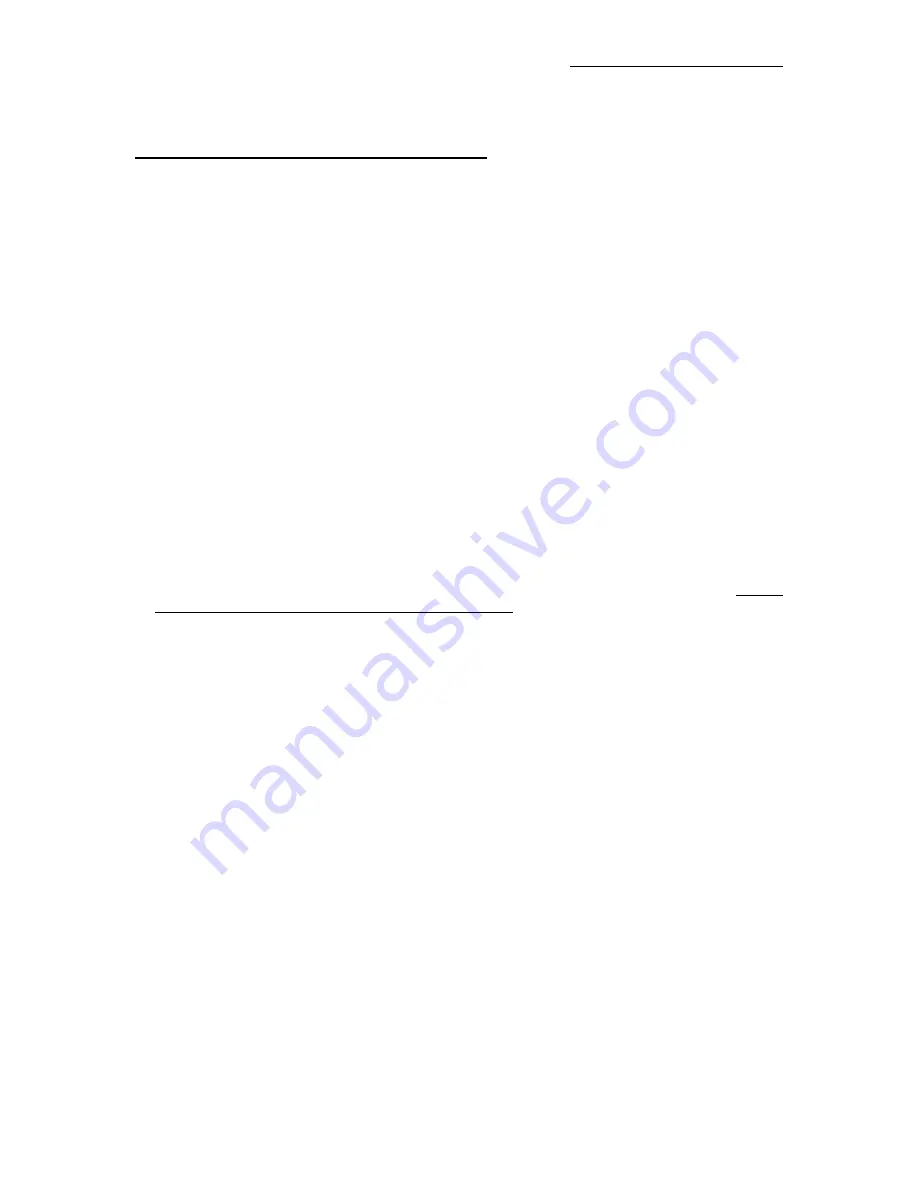
LABELER TYPE SETUP PROCEDURE
6-11
DUAL ACTION TAMP (DAT) SETUP (cont’d)
DAT GENERAL SETUP PROCEDURES
1) The Label Stop must be properly set for the Applicator to work correctly. Adjust the Label Stop Value
to position the label at or slightly back from the Peel Edge.
2) Tamp height should be adjusted so that the label feeds out in contact with the Label Pad. If the Pad is
too high, the label will not land consistently on the Pad. If the Label Pad is too low, the label will
dispense into the back of the Pad and jam. Most of this adjustment is done with the Peel Edge and is
discussed in the Tamp Applicator Setup Section of the Manual. It is important to adjust the Rotary
Actuator so the Label Pad is level with the Applicator.
The Rotary Actuator’s internal stops control
100% of where the swing arm stops – the shocks act as a “buffer” only!
See the Rotary Actuator
Stop Adjustment Guidelines section.
3) Make sure the label is aligned with the Pad so there is no over-hang. To adjust this, move the liner web
in or out by adjusting the Guide Collars and Unwind Disks.
4) Position the Air Assist Tube with the hole(s) centered on the label and pointing approximately ¼”in
from the Label Pad Edge. The air pressure should be set at 20-30 PSI. Press “Jog” to dispense a label.
If the label doesn’t feed out against the Label Pad or the vacuum doesn’t capture it, increase the air
pressure. Continue until the vacuum captures the label.
Warning:
There are other factors that can keep the label from staying on Label Pad. You may need more
vacuum, increased or decreased label dive, or the Air Assist Tube may need to be rotated.
5) Air pressure for the Tamp Slide and Rotary Actuator should start at 40 PSI, the Air Blast at 40-60 PSI,
and the Vacuum Pump at 20 PSI.
6) Air Blast Time is set through the Display and should be set long enough to apply a label firmly to the
product. Setting the time too high results in fewer labels/min a value to start at is 0.06 seconds. The Air
Blast Time applies to both the Swing and Tamp Sequences.
NOTE: To avoid injury, make sure the Applicator is offline for this adjustment!
ROTARY ACTUATOR STOP ADJUSTMENT GUIDELINES
1)
Determine application – Reels-up, Overhead and Above etc. Keep in mind the gravity factor /
weight of the Pad and Manifold as this will be a factor of the supplied air pressure coming from
the Swing Valve Bank regulator – good starting pressure is 40 PSI.
2)
Adjust Airflow Needle Valves, which are located on the side of the longest “tube” of the Rotary
Actuator, with a flat blade screwdriver. Turning the screw CW – decreases the airflow. Turning
the screw CCW – increases the airflow. Typical flow control setting is ½ turn CCW from full
CW.
Note: proper settings = a smooth and controlled cycle!
3)
Proper set up for the 90-degree Swing Tamp.
The Rotary Actuator Internal Stops control
100% of where the Swing Arm Stops – the Shocks act as a “buffer” only!
With proper
amount of air pressure going to the Rotary Actuator, loosen the Retract Jam Nut, which is located
on the end of the longest Rotary Actuator Tube. Use a 3/16” Allen wrench and turn the stop set
screw CW. This action will move the Swing Tamp Arm away from the Tamp Home Shock. The
Tamp Home Shock should protrude from the Stop Coupling by 1/8” – 3/16”. If this is not the case
– make the necessary adjustments. Once this is set, turn the retract setscrew CCW until the Swing
Arm has come to rest against the Home Stop Shock Coupling. Tighten the Jam Nut.
4)
Set the Extend Rotary Stop as per above instructions. You will notice the Extend Shock does not
have a Stop Coupling. This Shock should be adjusted to allow for one half of its travel to be
compressed when the Swing Arm is extended.
Summary of Contents for 360a series
Page 47: ...GENERAL SETUP PROCEDURES 5 1 360a SERIES SETUP PROCEDURES...
Page 70: ...GENENRAL MAINTENANCE 8 1 360a SERIES GENERAL MAINTENANCE PROCEDURES...
Page 102: ...13 1 360 APPLICATOR DRAWINGS 360a SERIES CE MECHANICAL AND ELECTRICAL DRAWINGS...
Page 103: ......
Page 104: ......
Page 105: ......
Page 106: ......
Page 107: ......
Page 108: ......
Page 109: ......
Page 110: ......
Page 111: ......
Page 112: ......
Page 113: ......
Page 114: ......
Page 115: ......
Page 116: ......
Page 117: ......
Page 118: ......
Page 119: ......
Page 120: ......
Page 121: ......
Page 122: ......
Page 123: ......
Page 124: ......
Page 125: ......
Page 126: ......
Page 127: ......
Page 128: ......
Page 129: ......
Page 130: ......
Page 131: ......
Page 132: ......
Page 133: ......
Page 134: ......
Page 135: ......
Page 136: ......
Page 137: ......
Page 138: ......
Page 139: ......
Page 140: ......
Page 141: ......
Page 142: ......
Page 143: ......
Page 144: ......
Page 145: ......
Page 146: ......
Page 147: ......
Page 148: ......
Page 149: ......
Page 150: ......
Page 151: ......
Page 152: ......
Page 153: ......
Page 154: ......
Page 155: ......
Page 156: ......
Page 157: ......
Page 158: ......
Page 159: ......
Page 160: ......
Page 161: ......
Page 162: ......
Page 163: ......
Page 164: ......
Page 165: ......
Page 166: ......
Page 167: ......
Page 168: ......
Page 169: ......
Page 170: ......
Page 171: ......
Page 172: ......
Page 173: ......
Page 174: ......
Page 175: ......
Page 176: ......