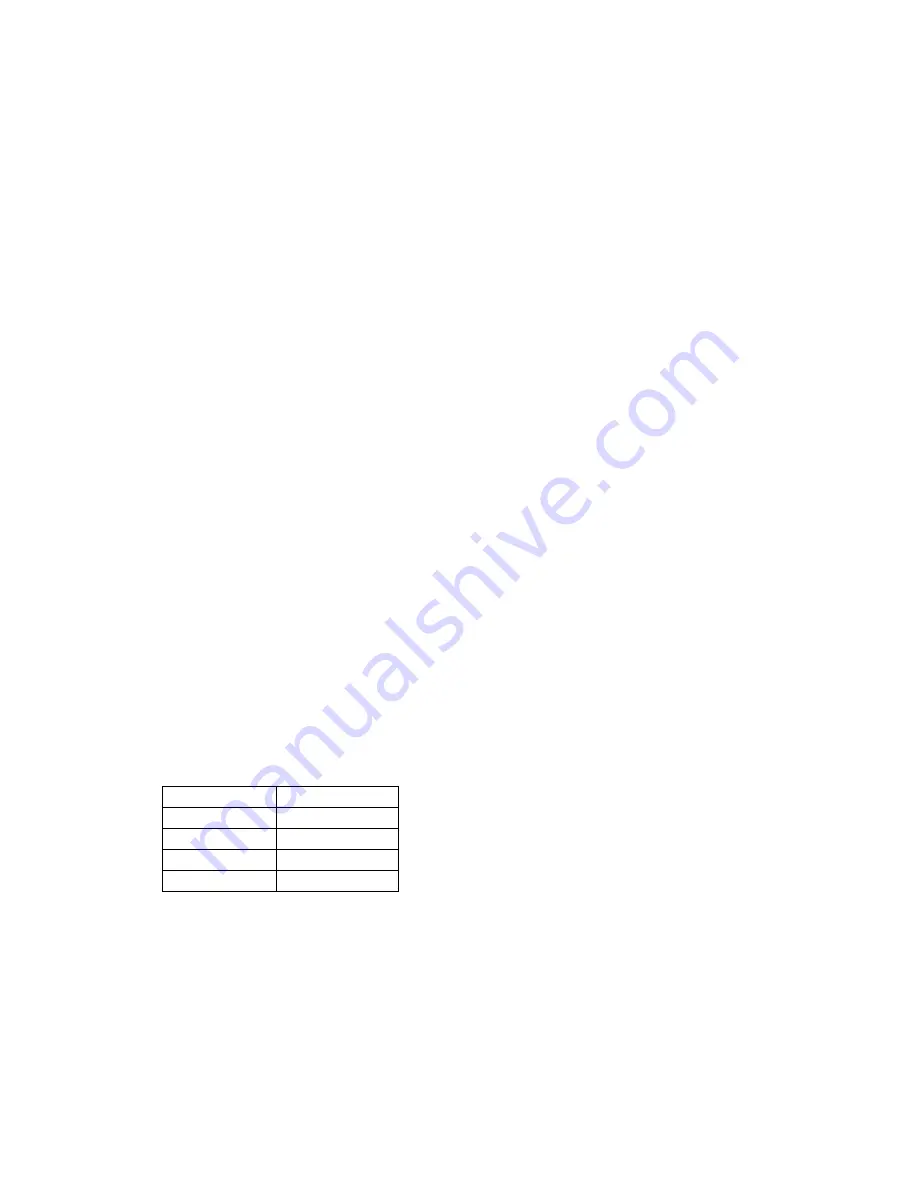
Testing Procedures
The 360a-CE applicator was tested as a merge with the product detect sensor and display attached.
Because of the many configurations and options that are available for this model, there was no way to
test all configurations. The only issue with the different noses will be machine safety. The integration of
an applicator into a product line may cause pinch points or other dangerous situations that will need
guarded. The responsibility for guarding lies with the integrator.
Safety Related Issues to Ensure Compliance
•
End user is responsible for meeting the final protective ground requirements.
•
The power inlet on the back of the applicator is the AC power disconnect. The end user is
responsible for determining and providing a supply disconnect for the system.
•
Voltages greater than 60 volts may be present inside the applicator after a discharge time of 5
seconds.
•
The end user must provide protection concerning power interruptions/restoration, if needed.
•
The end user must provide earth ground fault current protection, if required.
•
The end user will provide any guarding needed after integration of the applicator.
Emergency Stop Actuators
EN/ISO 13850:2015 Clause 4.3.2 requires that an emergency stop device shall be located at each operator
control station, except where the risk assessment indicates that this is not necessary.
Upon reviewing the machine with the manufacture, it was agreed that the risks posed by the labeling
machine itself are not sufficient as to require a dedicated emergency stop pushbutton at the HMI console.
An entanglement test was preformed between the Nip and Drive rollers, and it was found that no
significant pull was exerted on fabric, and that only a mild pinch was exerted on the fingers.
The main machine into which this machine is incorporated should have an emergency stop system that
will remove power and air to the 360a system, thus removing all power to its actuators.
Acoustic Emissions Data
A weighted emission sound pressure levels at workstations do not exceed 70 dB(A).
Measurement Locations:
M1 –In front of label spindle
M2 –Operator’s position when using the HMI
M3 –Rear of machine frame
Location
Level (dB)A
M1
81.9
M2
83.6
M3
79.8
Summary of Contents for 360a series
Page 47: ...GENERAL SETUP PROCEDURES 5 1 360a SERIES SETUP PROCEDURES...
Page 70: ...GENENRAL MAINTENANCE 8 1 360a SERIES GENERAL MAINTENANCE PROCEDURES...
Page 102: ...13 1 360 APPLICATOR DRAWINGS 360a SERIES CE MECHANICAL AND ELECTRICAL DRAWINGS...
Page 103: ......
Page 104: ......
Page 105: ......
Page 106: ......
Page 107: ......
Page 108: ......
Page 109: ......
Page 110: ......
Page 111: ......
Page 112: ......
Page 113: ......
Page 114: ......
Page 115: ......
Page 116: ......
Page 117: ......
Page 118: ......
Page 119: ......
Page 120: ......
Page 121: ......
Page 122: ......
Page 123: ......
Page 124: ......
Page 125: ......
Page 126: ......
Page 127: ......
Page 128: ......
Page 129: ......
Page 130: ......
Page 131: ......
Page 132: ......
Page 133: ......
Page 134: ......
Page 135: ......
Page 136: ......
Page 137: ......
Page 138: ......
Page 139: ......
Page 140: ......
Page 141: ......
Page 142: ......
Page 143: ......
Page 144: ......
Page 145: ......
Page 146: ......
Page 147: ......
Page 148: ......
Page 149: ......
Page 150: ......
Page 151: ......
Page 152: ......
Page 153: ......
Page 154: ......
Page 155: ......
Page 156: ......
Page 157: ......
Page 158: ......
Page 159: ......
Page 160: ......
Page 161: ......
Page 162: ......
Page 163: ......
Page 164: ......
Page 165: ......
Page 166: ......
Page 167: ......
Page 168: ......
Page 169: ......
Page 170: ......
Page 171: ......
Page 172: ......
Page 173: ......
Page 174: ......
Page 175: ......
Page 176: ......