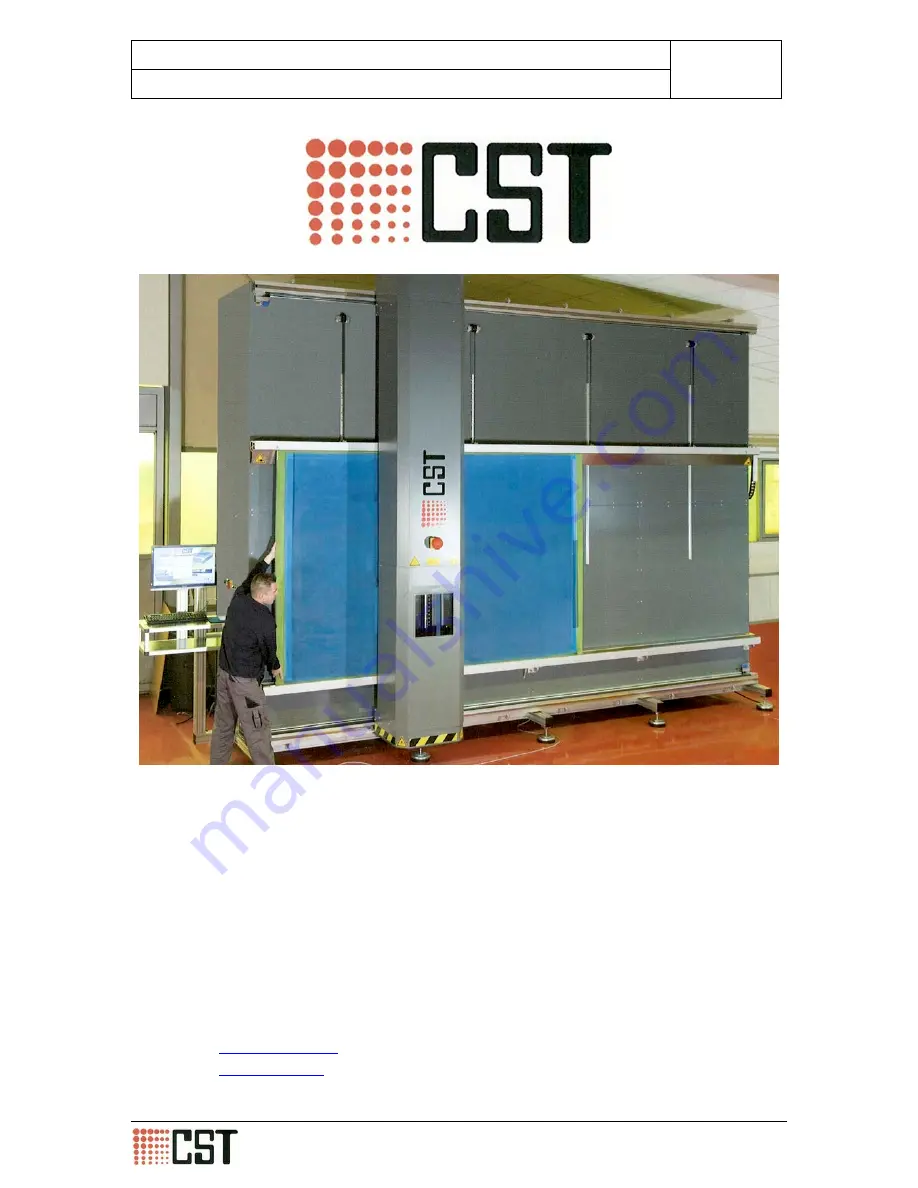
INSTRUCTION MANUAL
Effective date:
30.09.2013
Digital Light Engraver DLE
ORIGINAL INSTRUCTION MANUAL
CST GmbH
Königsberger Straße 117
47809 Krefeld - Germany
Telephone: +49 2151 1592260
Fax:
+49 2151 520329
Email:
CST GmbH
Königsberger Straße 117
47809 Krefeld - Germany
Page 1 of 69
Betriebsanleitung DLE-AF 01.0 engl.docx