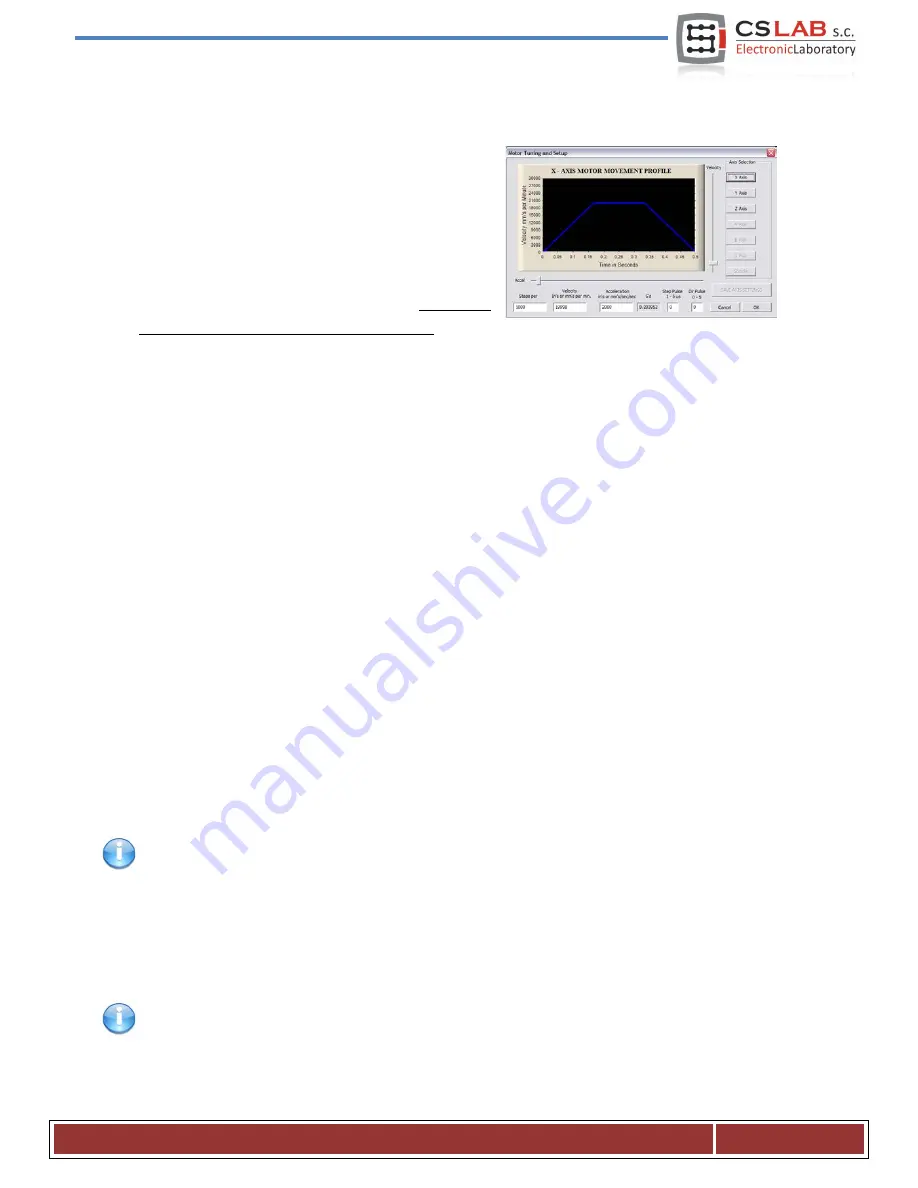
10.7
Configuration of the resolution, speed and acceleration of the axes
Before starting the work, it is necessary to set correctly
the resolution (called scaling) of the axis and to set their
max. speed and accelerations -in the Mach3 program -
„Config/Motor Tuning” menu. In the window, first select
the axis you want to configure, next enter the parameters
and click on „SAVE AXIS SETTINGS”. Now you can select
and set the next axis. If we forget to click on „SAVE AXIS
SETTINGS” all entered changes will not be saved.
For the correct axis scaling you must know the number of steps per unit (millimeter, inch or degree).
To understand how to calculate it, look at the example below:
•
The servomotor powers the line axis with 10000 rpm encoder.
•
The servo drive is configured without a multiplier and electronic gear, so 10000 STEP pulses
cause a 1 rev of the motor.
•
To transfer the drive there was used a ball screw - pitch
10mm
.
•
No ratio between the motor and the screw.
There are 10000 pulses per motor revolution and feed rate is 10mm per revolution. Dividing this value
10000 pulses/10mm we get 1000 pulse = 1mm movement, which we enter into the “Steps Per” box in the
configuration window.
In the „Velocity”, we set the axis speed. If we are using the millimeters as an unit then the speed is shown
in mm/min, if we use degrees - degree/min, if inch - inch/min. Max. speed value is very individual it
depends what motors, drives etc. were used. For the first tests, we recommend entering relatively small
value such as 2000mm/min, in case something goes wrong, we would always have enough time to press
the emergency stop E-STOP.
In the „Acceleration” area, we define the acceleration for the axis. At the beginning, we recommend to
enter something about 500mm/sec/sec. Later you can set this parameter experimentally by observing the
machine working.
Remember that after finished edition for each axis you should click on „SAVE AXIS SETTINGS”. Do the
configuration in the following order:
Open the „Motor Tuning” window
Select the axis („Axis Selection”)
Enter the parameters
”SAVE
AXIS SETTINGS”
Select the next axis
etc. Click „OK” and close the window.
„Step pulse” and „dir pulse” areas do not matter for CSMIO/IP-M. They are used to control via the LPT port
and they define the width and the STEP/DIR pulse time. The CSMIO/IP-M controller provides the signal
with the 50% duty cycle and STEP to DIR delay (10 us), which is the most optimal variant.
C S - L a b s . c . – C N C C S M I O / I P - M c o n t r o l l e r
Page 44