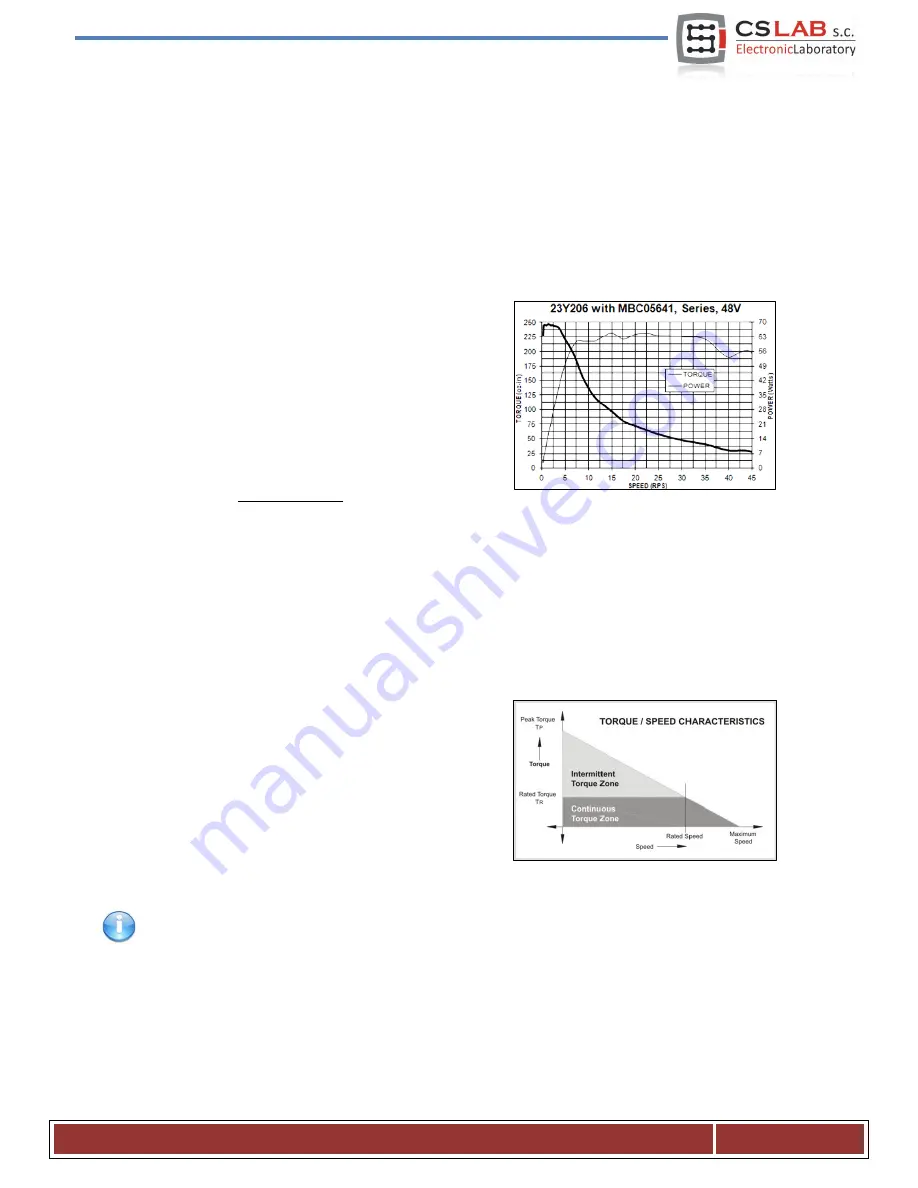
5.
Recommendations and drive selection (motor drives)
Selection of the appropriate motors to the machine is very individual. In this chapter, we briefly describe
the difference between stepper and servomotors. Designers' practice shows there is a dilemma – what
solution should be chosen. Not so long ago – because of high prices of servo drives, in the simpler
machines usually the stepper motors were used. Today, the technological progress and the dissemination
of servo technology causes that building a machine – even like a hobby – it’s worth to consider servo
drives
The most common mistake while decision-making is the
power selection (and torque) of the servo drive. It happens
because we are suggested by torque and holding torque.
The first parameter is usually given with the servo drives
and the second with the stepper motors. Both are usually in
the same unit Nm (Newton – meter).
Do not compare these
parameters when you are choosing servo drive power.
Holding torque in the stepper motors is shaft torque of the
powered motor in standby mode. When the revs are very
low – something about 200 rpm - the torque is almost the same (pictures below), but with increasing revs
the torque, actually the torque on the motor shaft), decreases drastically. It decreases to such low values
that sometimes around 1000 rpm the motor has no power to work itself, not saying about propelling the
machine.
In the simple words: the 3Nm stepper motor, reaches 3Nm torque at very low (200 rpm.) revs, when the
revs increase its power decrease to zero. In the graph above you can see example stepper motor
characteristic.
It is completely different in the servomotors. First, the
torque and the rev speed are nominal. Therefore, the 1Nm/
2000 rpm motor can operate continuously at 2000 rpm and
at this speed provides 1Nm of the torque on the shaft.
Besides the servomotors have another one important
feature: they can be temporarily overloaded. What does it
mean? That the 1Nm motor can temporarily deliver even
2,5-4Nm (depending on the type).
If you are planning to use high-resolution servo drive, the best solution is the professional CSMIO/IP-S
controller, which has faster (4MHz) STEP/DIR outputs. Of course, electronic gear function in the servo
drive can be used but must be noted that high values of electronic gear reduce the resolution and
accuracy of the system.
C S - L a b s . c . – C N C C S M I O / I P - M c o n t r o l l e r
Page 22