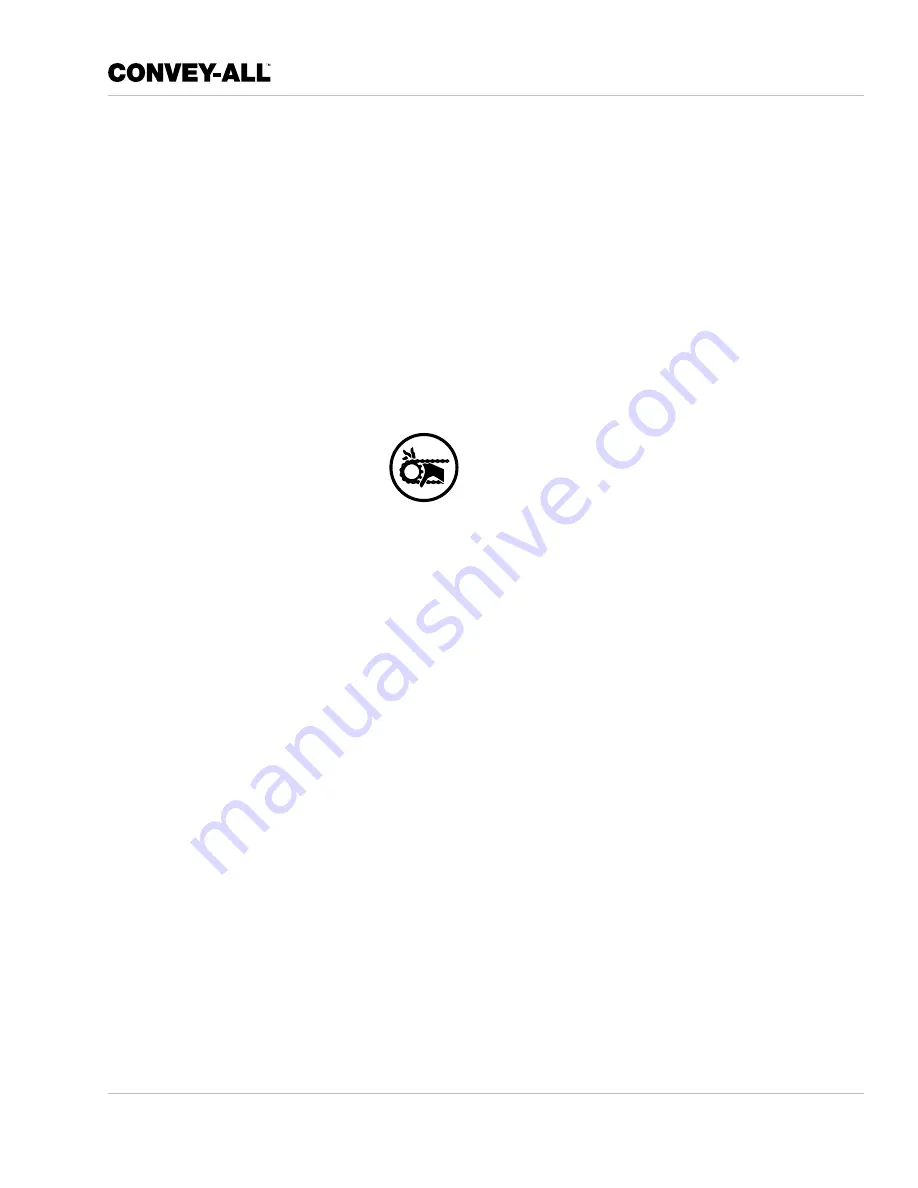
Operator’s Manual: 2200-TL Series Conveyor
Revised 09.2018
2-3
2.3 EQUIPMENT SAFETY GUIDELINES
• Safety of the operator and bystanders is one of the
main concerns in designing and developing this
conveyor. However, every year many accidents
occur which could have been avoided by a few
seconds of thought and a more careful approach
to handling equipment.
• Do not allow personnel to operate this unit until they
have read this manual. They must have a thorough
understanding of all the safety precautions.
Review the safety instructions with all personnel
annually.
• In order to provide a better view, some
images in this manual may show an
assembly with a safety guards removed.
Equipment should never be operated in
this condition. Keep all guards in place.
If removal becomes necessary for
repairs, replace the guard prior to use.
• This equipment is dangerous to children and
people unfamiliar with its operation.
The operator must be responsible, properly trained
and physically able. You should be familiar with
farm machinery in general.
• Never exceed the limits of a piece of machinery.
If its ability to do a job, or to do so safely, is in
question - DON’T TRY IT.
• Do not modify the equipment in any way.
Unauthorized modification result in serious injury
or death and may impair the function and life of the
equipment.
• The design and configuration of this conveyor
includes safety decals and equipment. They need
to be clean, readable or in good, working condition.
2.4 SAFETY DECALS
• Keep safety decals clean and legible at all times.
• Replace safety decals that are missing or have
become illegible.
• Replaced parts that displayed a safety decal
should also display the current decal.
• All safety decals have a part number in the lower
right hand corner. Use this part number when
ordering replacements.
• Safety decals are available from your
authorized distributor, dealer or directly from
Convey-All Industries Inc.
2.4.1 How to Install Safety Decals:
1. Be sure that the installation area is clean and dry.
2. Ensure temperature is above 50°F (10°C).
3. Determine exact position before you remove the
backing paper.
4. Remove the smallest portion of the split backing
paper.
5. Align the sign over the specified area and carefully
press the small portion with the exposed sticky
backing in place.
6. Slowly peel back the remaining paper and
carefully smooth the remaining portion of the
sign in place.
7. Small air pockets can be pierced with a pin and
smoothed out using the piece of sign backing
paper.
Summary of Contents for 2245-TL
Page 1: ...TRANSLOADING CONVEYOR Models 2245 TL 2252 5 TL OPERATOR S MANUAL...
Page 4: ...This page intentionally left blank...
Page 8: ...Operator s Manual 2200 TL Series Conveyor 1 2 10 2015 This page intentionally left blank...
Page 48: ...Operator s Manual 2200 TL Series Conveyor 4 14 10 2015 This page intentionally left blank...
Page 54: ...Operator s Manual 2200 TL Series Conveyor 6 2 10 2015 This page intentionally left blank...