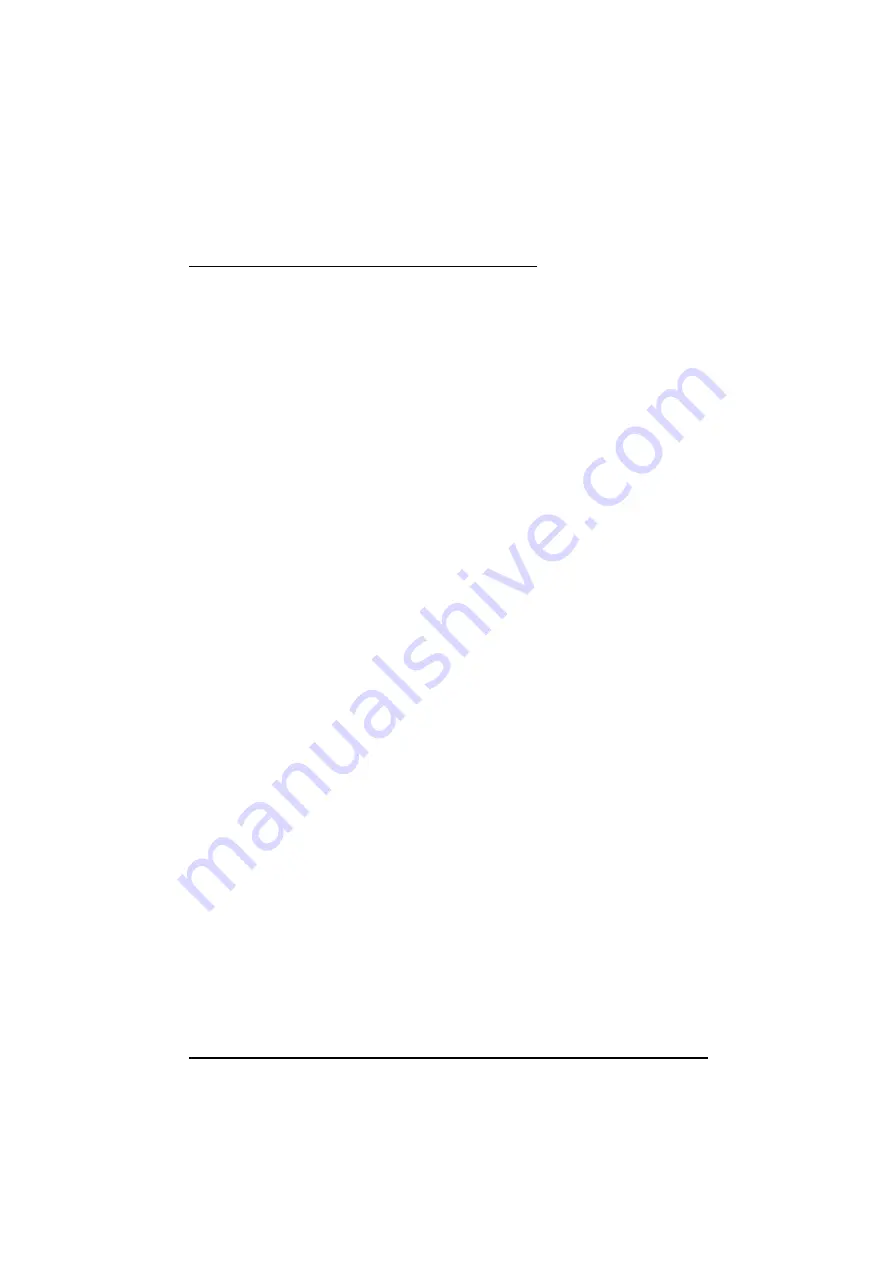
Dinverter
A
User Guide
Issue code: d2au9
42
Compliance with EMC emission standards (Figure 4–9)
General features
1
Single power ground bus-bar, or low-impedance ground terminal.
2
Incoming
AC
supply ground connected to the power ground bus-bar.
3
Connect grounds of any other circuits to the power ground bus-bar.
4
Site ground, if required.
5
Metal back-plate, safety bonded to the power ground bus-bar.
6
System isolator, circuit contactors and fuses/MCB.
7
Alternative position for Drive fuses/MCB.
8
When the motor ground connection is made at the Drive, fit a local
ground bus-bar close to the Drive.
9
Alternative safety ground for the motor.
10
Motor-frame ground connection, if required.
Special features for EMC
11
When the length of the motor cable exceeds 5m (16 feet), the
AC
supply
cable must be shielded (screened) or steel-wire armoured. Bond the shield
or armour to the enclosure using standard cable-gland fixings.
12
Drive heatsink directly grounded to the back-plate using metal
mounting brackets. If plastic mounting brackets are supplied, the
earthing spring must be used for grounding the heatsink. The
back-plate must be unpainted (eg. zinc-plated steel).
13
Mount the RFI filter at the left side of the Drive. Ensure a separation of
5 to 10mm (
1
/
4
to
3
/
8
in) from the Drive. Minimize the length of cables
between the Drive and RFI filter.
14
A shielded (screened) or steel-wire armoured cable must be used to
connect the Drive to the motor. The shield of the cable must be
connected to the motor ground terminal in the Drive by a connection
no longer than 50mm (2 in). The shield must also be bonded to the
back-plate by an un-insulated metal cable clamp. The clamp must be
positioned no further than 100mm (4 in) from the Drive.
15
Connect the shield of the motor cable to the ground terminal of the
motor frame using a link that is as short as possible and not exceeding
50mm (2 in) in length.
16
Do not place sensitive signal circuits in a zone extending 0.3m (12 in) all
around the Drive.
17
If the control circuit 0V is to be grounded, this should be done at the
system controller (eg. PLC) and not at the Drive. This is to avoid
injecting noise currents into the 0V circuit.