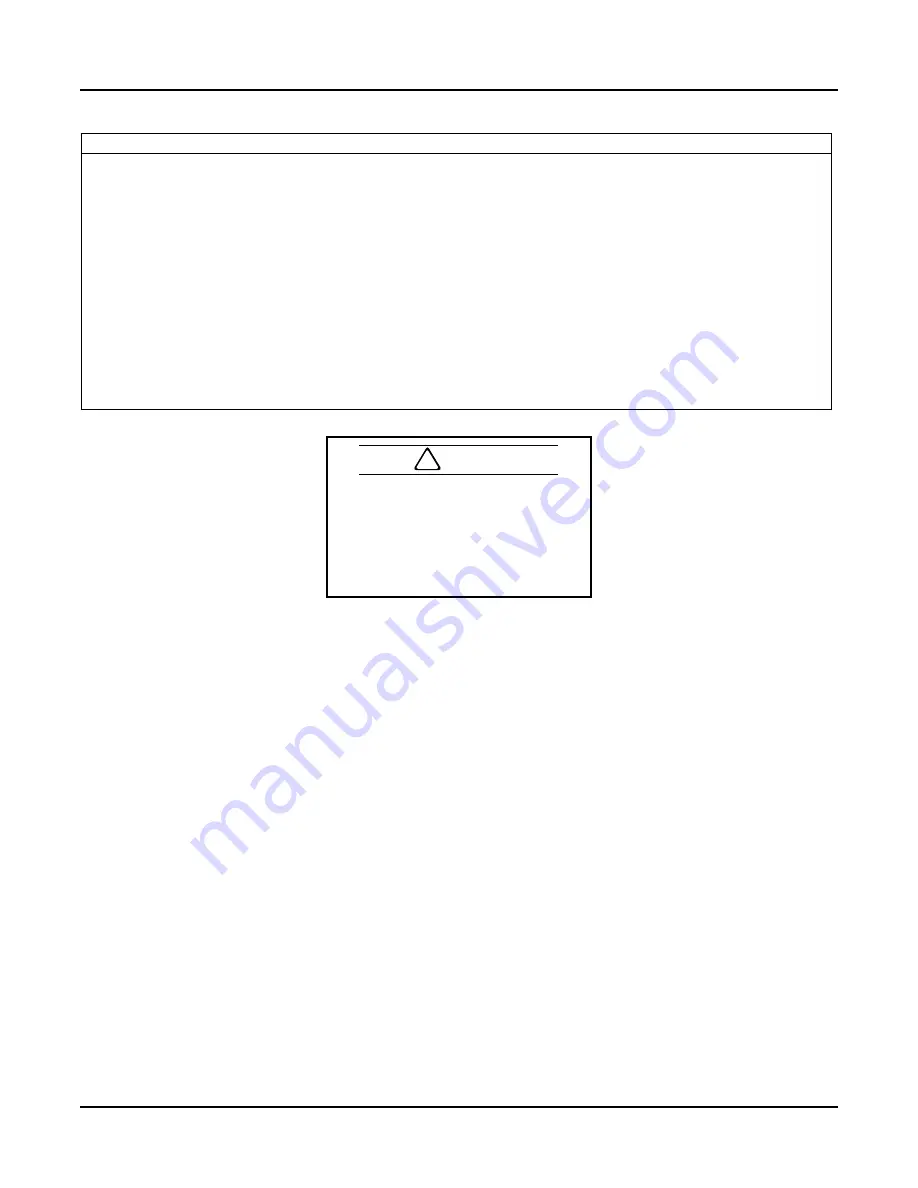
Chapter 5 — Service And Periodic Maintenance
Part No. 750-295
5-3
It is generally recommended that bottom blowdown be performed at least once in every eight-hour period.
Actual frequency may vary depending on water conditions and boiler operating conditions. Consult the
appropriate water treatment personnel regarding blowdown scheduling.
5.3-WATER COLUMN BLOWDOWN
Free flow of water through the water column and gauge glass is essential to obtaining accurate boiler water
level indication and control. It is recommended that the water column and gauge glass be blown down every
shift to remove accumulated solids. Regular blowdown of the water column will help maintain the integrity
of the water level probes and will help to ensure trouble-free operation of the boiler. See
Figure 5-2
for
procedure.
Manual Blowdown Procedure
Blowdown is most effective when the boiler is under a light load, and when the water level is at the Normal Operating Water
Level.
Be sure the blowdown piping is in proper operating condition. Waste should be piped to a point of safe discharge.
1.
Open the quick-opening valve.
2.
Crack the second or downstream valve slightly to allow the lines to warm, then continue opening slowly to its fully open posi-
tion.
The duration of each blowdown should be determined by water analysis. A reduction of water level in the gauge glass by about
1/2” can often serve as a rough guide, but should not replace water analysis procedures.
3.
When blowdown is complete, close the downstream (slow-opening) valve first, as quickly as possible. Then close the quick-
opening valve. Finally, crack the downstream valve slightly, then close it tightly.
Low Pressure Steam:
If the bottom blowdown piping is fitted with a single drain valve only, follow the above procedure, omitting the downstream valve.
!
Caution
During blowdown, do not pump the lever
action valve open and closed. Equipment
damage may result.
Under no circumstances should a blow-
down valve be left open. Never leave the
boiler unattended during blowdown.
Summary of Contents for ClearFire CFH
Page 14: ...Chapter 1 Introduction 1 8 Part No 750 295 ...
Page 27: ...Chapter 2 Installation Part No 750 295 2 13 Figure 2 10 CFH wiring diagram typical 10 60 HP ...
Page 42: ...Chapter 3 Flue and Combustion Air Venting 3 14 Part No 750 295 ...
Page 90: ......
Page 92: ...Chapter 6 Model CFH Parts 6 2 Part No 750 295 6 1 CONTROL PANEL 10 60 HP ...
Page 93: ...Chapter 6 Model CFH Parts Part No 750 295 6 3 6 1 CONTROL PANEL 70 80 HP ...
Page 100: ...Chapter 6 Model CFH Parts 6 10 Part No 750 295 Standard gas train 30 HP ...
Page 105: ...Chapter 6 Model CFH Parts Part No 750 295 6 15 6 4 2 Gas Train Dual Fuel 30 HP dual fuel ...
Page 106: ...Chapter 6 Model CFH Parts 6 16 Part No 750 295 40 HP dual fuel ...
Page 107: ...Chapter 6 Model CFH Parts Part No 750 295 6 17 50 60 HP dual fuel ...
Page 110: ...Chapter 6 Model CFH Parts 6 20 Part No 750 295 40 HP dual fuel lgp ...
Page 111: ...Chapter 6 Model CFH Parts Part No 750 295 6 21 50 60 HP dual fuel lgp ...
Page 112: ...Chapter 6 Model CFH Parts 6 22 Part No 750 295 6 4 4 Gas Train Propane 30 HP propane ...
Page 113: ...Chapter 6 Model CFH Parts Part No 750 295 6 23 40 HP propane ...
Page 114: ...Chapter 6 Model CFH Parts 6 24 Part No 750 295 50 60 HP propane ...
Page 120: ...e mail info cleaverbrooks com Web Address http www cleaverbrooks com ...