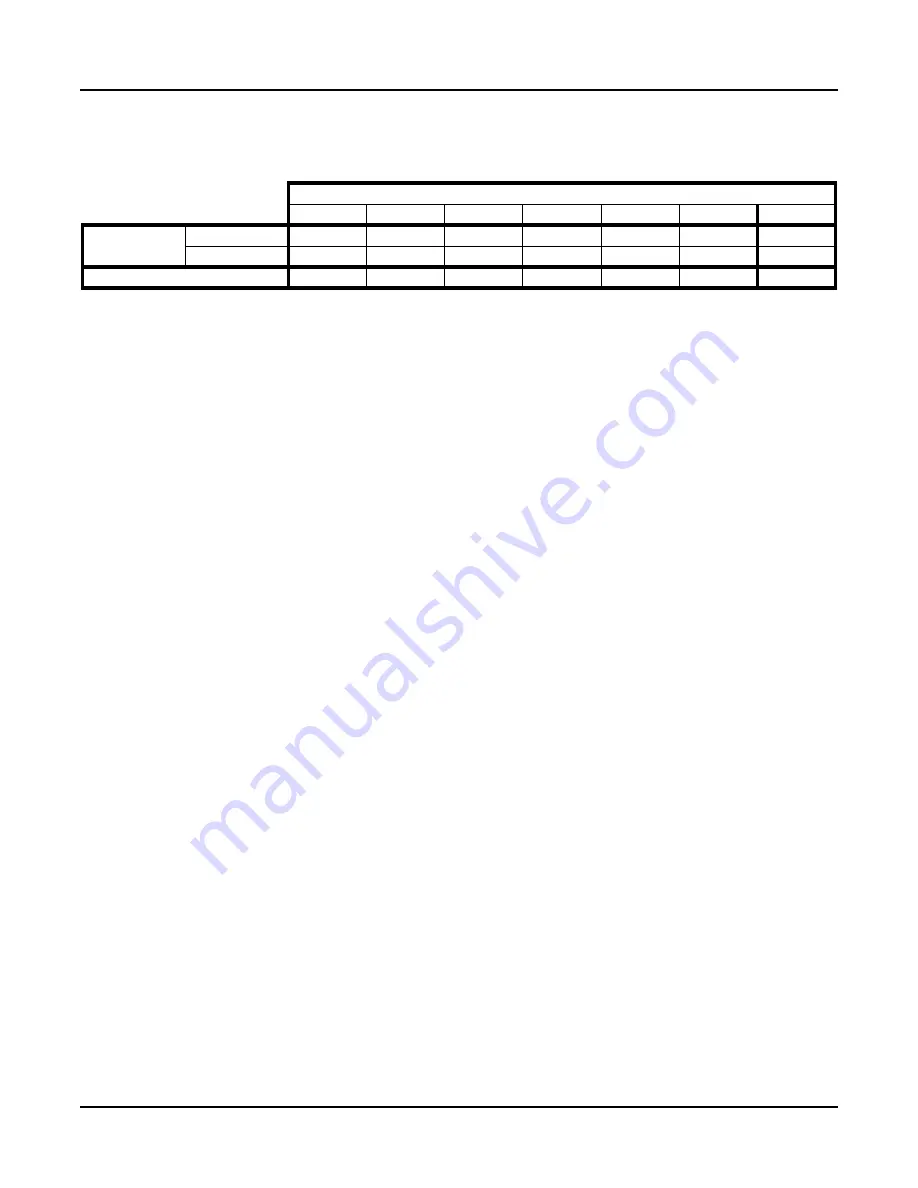
Chapter 4 — Commissioning
Part No. 750-295
4-25
13. After closing the handholes and reinstalling safety or relief valves, fill the boiler and fire it until the water
is heated to at least 180
o
F to drive off any dissolved gases.
4.15-POST START-UP CHECKOUT PROCEDURE
1. After verifying correct water level, fire the boiler in manual low fire.
2. Ensure the control valves will not shut off flow to the boiler.
3. Set high gas pressure switch to 50% higher than operating gas pressure at low fire. Set low gas pressure
switch to 50% lower than operating gas pressure at low fire.
4. Verify the ability of the flame system to detect and respond to a loss of flame. This can be done by
removing the ionization electrode (flame rod) cable. For a successful test the boiler should shut down
and the gas safety shutoff valve close with the display indicating a lockout condition. Reconnect the
ionization cable to the electrode.
5. Adjust gas choke for high fire combustion to desired excess air level (6-7% O2 recommended). Using
offset screw, set low fire O2 same as high fire O2.
6. Check the draft on the outlet stack on each boiler, compare to acceptable limits (-.25 to +.25“ W.C.)
and record in start up form.
7. Switch to automatic operation and monitor flue gas to ensure consistent excess air.
8. Reassemble all panels and covers that were removed and replace any plugs that were removed to check
gas pressure.
9. If boiler is equipped with a High Air Pressure Switch, check switch operation.
10. Verify with customer that softened water is being used and that a proper water treatment program is in
place.
11. Provide instructions to owner and operators on operation, safety and maintenance of the equipment.
4.16-FALCON CONTROL FUNCTIONS AND CUSTOMER INTERFACE
Following is a brief overview of the Falcon control features on ClearFire
®
steam boilers.
• Set Point
• Time-of-Day (TOD) Set Point
• Hysteresis On and Hysteresis Off
• PID modulation control
• Remote Enable and Remote 4-20mA Input
• Remote Modulation
• Remote Set Point
• Configurable pump/auxiliary relay contacts
• Annunciator
• Diagnostics
• Alert/Lockout History
• Trend Analysis
• Modbus communications
Table 4-6 CFH Boiler Water Capacity
Boiler Horsepower
10-15 HP
20-25 HP
30 HP
40 HP
50-60 HP
70 HP
80 HP
Normal water
volume
15# Steam
110 gal
137 gal
204 gal
237 gal
301 gal
457 gal
445 gal
150# Steam
121 gal
149 gal
221 gal
256 gal
323 gal
457 gal
445 gal
Water volume flooded
140 gal
170 gal
260 gal
300 gal
386 gal
559 gal
547 gal
Summary of Contents for ClearFire CFH
Page 14: ...Chapter 1 Introduction 1 8 Part No 750 295 ...
Page 27: ...Chapter 2 Installation Part No 750 295 2 13 Figure 2 10 CFH wiring diagram typical 10 60 HP ...
Page 42: ...Chapter 3 Flue and Combustion Air Venting 3 14 Part No 750 295 ...
Page 90: ......
Page 92: ...Chapter 6 Model CFH Parts 6 2 Part No 750 295 6 1 CONTROL PANEL 10 60 HP ...
Page 93: ...Chapter 6 Model CFH Parts Part No 750 295 6 3 6 1 CONTROL PANEL 70 80 HP ...
Page 100: ...Chapter 6 Model CFH Parts 6 10 Part No 750 295 Standard gas train 30 HP ...
Page 105: ...Chapter 6 Model CFH Parts Part No 750 295 6 15 6 4 2 Gas Train Dual Fuel 30 HP dual fuel ...
Page 106: ...Chapter 6 Model CFH Parts 6 16 Part No 750 295 40 HP dual fuel ...
Page 107: ...Chapter 6 Model CFH Parts Part No 750 295 6 17 50 60 HP dual fuel ...
Page 110: ...Chapter 6 Model CFH Parts 6 20 Part No 750 295 40 HP dual fuel lgp ...
Page 111: ...Chapter 6 Model CFH Parts Part No 750 295 6 21 50 60 HP dual fuel lgp ...
Page 112: ...Chapter 6 Model CFH Parts 6 22 Part No 750 295 6 4 4 Gas Train Propane 30 HP propane ...
Page 113: ...Chapter 6 Model CFH Parts Part No 750 295 6 23 40 HP propane ...
Page 114: ...Chapter 6 Model CFH Parts 6 24 Part No 750 295 50 60 HP propane ...
Page 120: ...e mail info cleaverbrooks com Web Address http www cleaverbrooks com ...