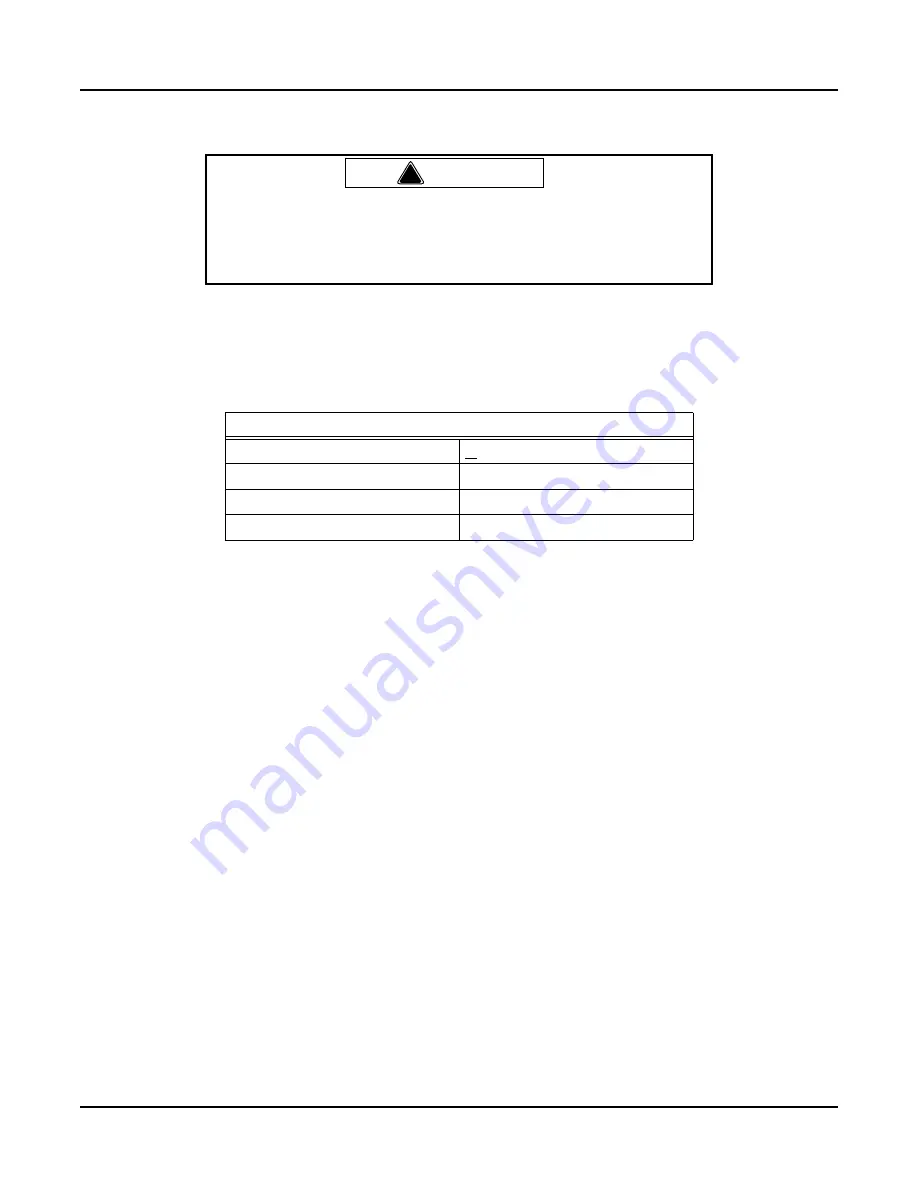
Chapter 4 — Commissioning
4-2
Part No. 750-295
4.1-OPERATING CONDITIONS
• The installation site should be as free as possible from vibration, dust, and corrosive media
• The controllers should be located as far as possible from sources of electromagnetic fields, such as
frequency converters or high-voltage ignition transformers
• Control panel must be connected to earth ground.
4.2-FILLING BOILER
Open the vent valve and fill the boiler slowly to allow entrapped air to escape. Do not close the vent valve
until water is visible in the gauge glass. Check to ensure that no leaks appear at any pipe connections and
correct if water leaks are noticed.
Note: If hydrostatic testing is required on site, use water at 70 deg F. Remove the safety valve prior to
testing and replace when finished.
4.3-CONTROL SETPOINTS
Preliminary settings of the burner/boiler controls are necessary for the initial starting of the boiler. After the
burner has been properly set, minor adjustments to these controls may be necessary for the particular
installation. For initial starting, set the following controls accordingly:
• Operating and High Limit Controls - Set the dial @ maximum.
• Combustion Air Proving Switch - Set the dial @ minimum.
• Low Gas Pressure Switch - Set the dial @ minimum.
• High Gas Pressure Switch - Set the dial @ maximum.
Depress all manual reset buttons for all controls prior to starting.
Boiler room ambient conditions
Relative humidity
< 85-90%
Ambient temperature range
0
o
C to 50
o
C / 32
o
F to 122
o
F
Storage temperature range
-20
o
C to 60
o
C / -4
o
F to 140
o
F
Combustion Air Temperature
0
o
C to 50
o
C / 32
o
F to 122
o
F
!
Warning
When using direct vent combustion in cold climates, special care must
be taken to observe combustion air temperature limits.
Failure to
follow this precaution may lead to equipment damage or unsafe
operation.
Summary of Contents for ClearFire CFH
Page 14: ...Chapter 1 Introduction 1 8 Part No 750 295 ...
Page 27: ...Chapter 2 Installation Part No 750 295 2 13 Figure 2 10 CFH wiring diagram typical 10 60 HP ...
Page 42: ...Chapter 3 Flue and Combustion Air Venting 3 14 Part No 750 295 ...
Page 90: ......
Page 92: ...Chapter 6 Model CFH Parts 6 2 Part No 750 295 6 1 CONTROL PANEL 10 60 HP ...
Page 93: ...Chapter 6 Model CFH Parts Part No 750 295 6 3 6 1 CONTROL PANEL 70 80 HP ...
Page 100: ...Chapter 6 Model CFH Parts 6 10 Part No 750 295 Standard gas train 30 HP ...
Page 105: ...Chapter 6 Model CFH Parts Part No 750 295 6 15 6 4 2 Gas Train Dual Fuel 30 HP dual fuel ...
Page 106: ...Chapter 6 Model CFH Parts 6 16 Part No 750 295 40 HP dual fuel ...
Page 107: ...Chapter 6 Model CFH Parts Part No 750 295 6 17 50 60 HP dual fuel ...
Page 110: ...Chapter 6 Model CFH Parts 6 20 Part No 750 295 40 HP dual fuel lgp ...
Page 111: ...Chapter 6 Model CFH Parts Part No 750 295 6 21 50 60 HP dual fuel lgp ...
Page 112: ...Chapter 6 Model CFH Parts 6 22 Part No 750 295 6 4 4 Gas Train Propane 30 HP propane ...
Page 113: ...Chapter 6 Model CFH Parts Part No 750 295 6 23 40 HP propane ...
Page 114: ...Chapter 6 Model CFH Parts 6 24 Part No 750 295 50 60 HP propane ...
Page 120: ...e mail info cleaverbrooks com Web Address http www cleaverbrooks com ...