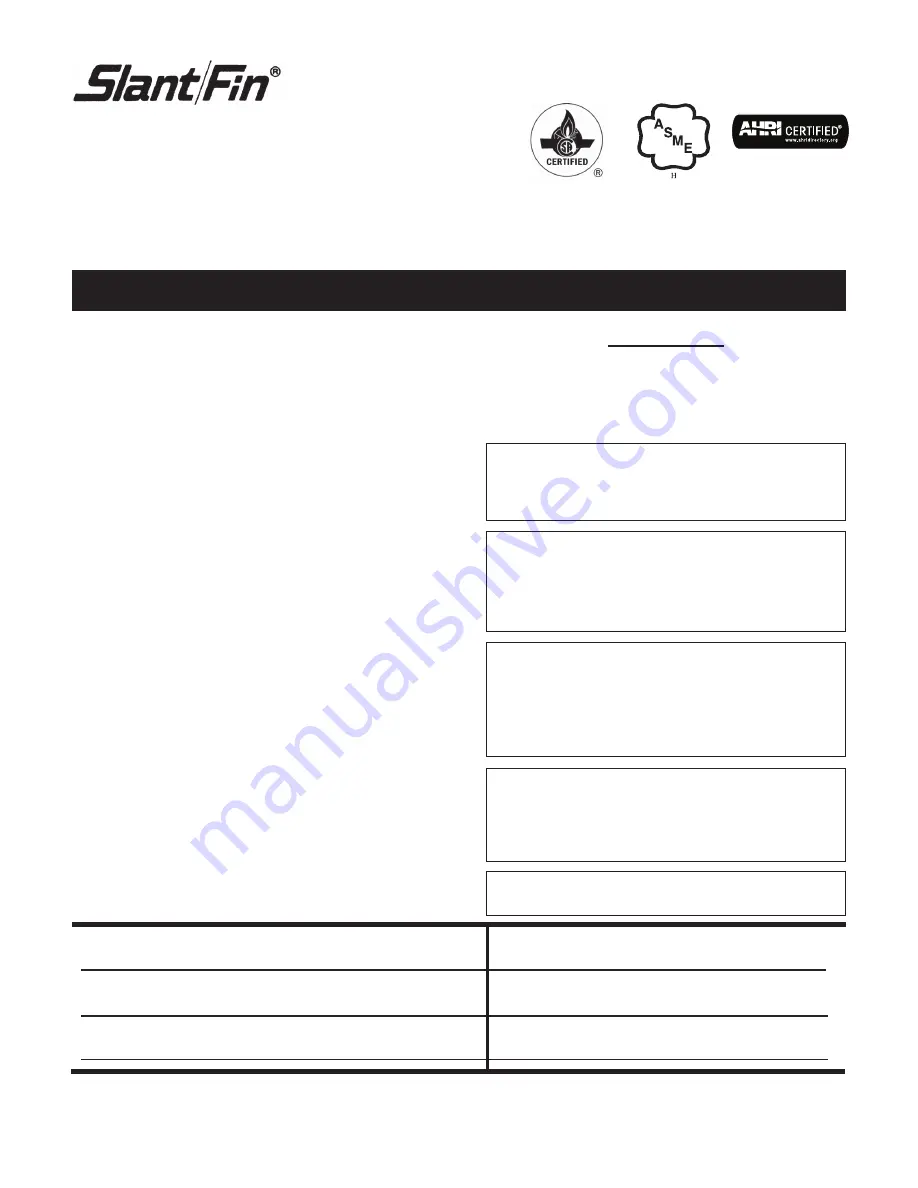
CONTENTS . . . . . . . . . . . . . . . . . . . . . . . . . . . . . . . . . . . PAGE
Dimensions. . . . . . . . . . . . . . . . . . . . . . . . . . . . . . . . . . . . . . 2,3
Installation Requirements
Boiler Location . . . . . . . . . . . . . . . . . . . . . . . . . . . . . . . . . . 3
Boiler Foundation. . . . . . . . . . . . . . . . . . . . . . . . . . . . . . . . 3
Chimney Requirements . . . . . . . . . . . . . . . . . . . . . . . . . . . 4
Minimum Clearance . . . . . . . . . . . . . . . . . . . . . . . . . . . . . . 4
Draft Hood . . . . . . . . . . . . . . . . . . . . . . . . . . . . . . . . . . . . . 4
Vent Piping . . . . . . . . . . . . . . . . . . . . . . . . . . . . . . . . . . . . . 4
Vent Damper Installation. . . . . . . . . . . . . . . . . . . . . . . . . 5,6
Electrical Controls and Wiring . . . . . . . . . . . . . . . . . . . . 7–9
Pump or Valve Zoning of Water Boilers. . . . . . . . . . . . . 8–9
Sequence of Operations . . . . . . . . . . . . . . . . . . . . . . . . . 10
Boiler Water Temperature Conrol . . . . . . . . . . . . . . . 11–12
Gas Piping . . . . . . . . . . . . . . . . . . . . . . . . . . . . . . . . . . . . 13
Boiler Room Air Supply and Ventilation . . . . . . . . . . . . . 13
Water Piping at Boiler . . . . . . . . . . . . . . . . . . . . . . . . . . . 14
Operating Instructions
Filling and Venting Water Systems . . . . . . . . . . . . . . . . . 14
Initial Start, Safety and Lighting Instructions. . . . . . . . . . 14
Burner Adjustment, Checking Gas Input. . . . . . . . . . . . . 15
Care and Maintenance
General Maintenance. . . . . . . . . . . . . . . . . . . . . . . . . . . . 16
Water Level Check . . . . . . . . . . . . . . . . . . . . . . . . . . . . . . 16
Annual Inspection and Cleaning . . . . . . . . . . . . . . . . . . . 16
Safety Check for Control Systems. . . . . . . . . . . . . . . . . . 16
Protection from Freezing/Water Treatment . . . . . . . . . . . 17
Keeping Area Clear . . . . . . . . . . . . . . . . . . . . . . . . . . . . . 17
Troubleshooting Guide . . . . . . . . . . . . . . . . . . . . . . . . . . . . . 18
Replacement Parts . . . . . . . . . . . . . . . . . . . . . . . . . . . . . . . . 19
Appendix A & B . . . . . . . . . . . . . . . . . . . . . . . . . . . . . . . . . . . 19
Appendix C, D & E . . . . . . . . . . . . . . . . . . . . . . . . . . . . . . . . 20
Printed in Canada 1014
Publication No. SE-41
Part No. 46-0569
Revision C
HOT WATER MODELS SE-70 THROUGH SE-245
INSTALLATION AND OPERATING INSTRUCTIONS
GAS-FIRED CAST-IRON BOILERS FOR NATURAL AND L.P. PROPANE GASES
SENTINEL
™
IMPORTANT
READ ALL OF THE FOLLOWING
WARNINGS AND STATEMENTS
BEFORE READING THE
INSTALLATION INSTRUCTIONS
The installation must conform to the requirements of the
authority having jurisdiction or, in the absence of such
requirements, to the National Fuel Gas Code, ANSI Z2231
latest edition or CSA B 149.1 latest edition
for natural gas
and propane
. The installation must also conform to the
additional requirements in this Slant/Fin Instruction Book.
In addition, where required by the authority having juris dic -
tion, the installation must conform to American Society of
Mechanical Engineers Safety Code for Controls and Safety
Devices for Automatically Fired Boilers, No. CSD-1 or
CSA B
149.1 latest edition for natural gas and propane
. If there is
any conflict in the above requirements, then the more
stringent requirement will apply.
This manual must be left with owner and should be hung
on or adjacent to the boiler for reference.
WARNING
This boiler, gas piping and accessories must be installed,
connected, serviced and repaired by a trained, experienced
service technician, familiar with all precautions required for
gas-fired equipment and licensed or otherwise qualified, in
compliance with the authority having jurisdiction.
Heating Contractor
Address
Phone Number
Boiler Model Number
Boiler Serial Number
Installation Date
WARNING
SEE "WARNING" ON PAGE 4
FOR LIQUEFIED PETROLEUM (L.P.)
PROPANE GAS-FIRED BOILERS