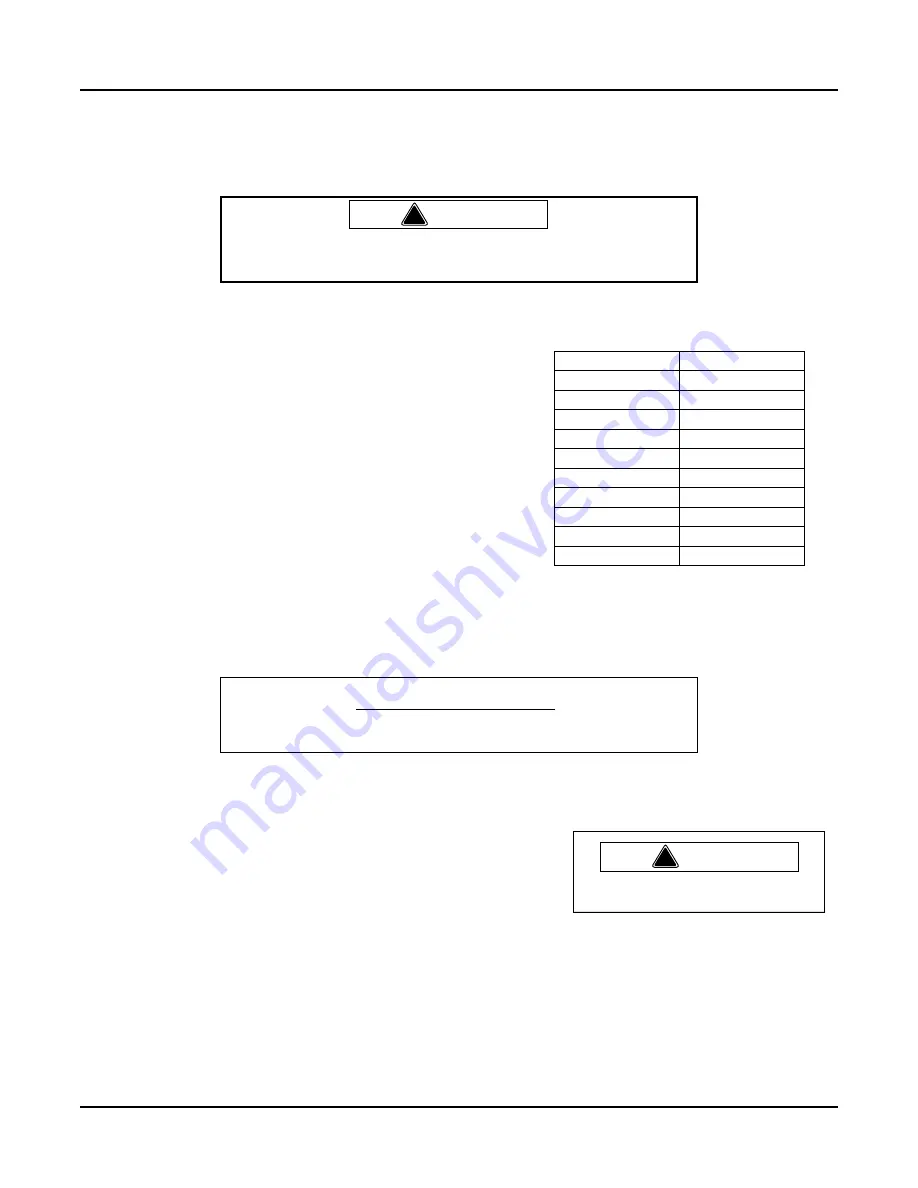
Chapter 2 — Installation
2-4
Part No. 750-295
Because of the variables involved, no single boiler compound can be considered a cure-all; nor is it
advisable to experiment with homemade treating methods. A sound treatment program should include a
periodic analysis of the water in the system.
The internal or waterside surfaces of the pressure vessel
should be inspected at regular intervals for evidence of
corrosion, pitting, contamination, or accumulations of foreign
matter. If any of these conditions are detected, contact your
local Cleaver-Brooks authorized representative for advice on
corrective action. It is recommended that a properly sized
water meter be installed in the raw water makeup line to
accurately determine the amount of raw water admitted to the
boiler.
Surface blow-off is available for steam boilers. This option
allows removal of surface water impurities through a
blowdown line located at the normal operating water level of
the boiler. If allowed to accumulate, surface impurities may
impede steam release and could cause foaming, leading to
priming and carryover in the steam lines.
An optional chemical feed system can be used to introduce
controlled amounts of feedwater treatment chemicals into the boiler.
Refer to
Table 2-1
CFH
water quality guidelines
.
Consult with factory for Reverse Osmosis (RO) applications.
2.4-BOILER ROOM / BOILER CLEARANCES
The boiler room must comply with all building codes and
regulations. An adequate supply of combustion air and sufficient
ventilation are required for safe operation. If the optional direct vent
combustion air kit is not used, ventilation must be provided to meet
applicable regulations for air supply.
Clean combustion air is required for optimum efficiency and boiler operation (minimum combustion air 10
cfm per boiler horsepower). Dust and airborne contaminants will adversely effect burner performance.
If conditions dictate, a serviceable filter must be placed at the burner inlet to eliminate airborne
contamination to the burner.
If a direct vent air intake is used, the intake and flue venting should be terminated so as to prevent rain,
snow, dust, or debris from entering the intake piping.
Notice
Corrosion and sludge deposits in old systems must be removed
prior to installation of a new boiler.
!
Warning
Inadequate or improper water treatment will shorten the life
of the boiler, and could result in a hazardous condition.
Table 2-1
CFH water quality guidelines
QUANTITY
LIMITS
Oxygen
<0.005 ppm
CO2
0 ppm
Hardness
<2.0 ppm
Suspended Solids
<300 ppm
pH
8.5 - 10.5
Sulfite
>50 ppm
Fe
<0.1 ppm
Silica
<150 ppm
Total Alkalinity
<700 ppm
Dissolved Solids
<3,000 ppm
!
Warning
The boiler must not be installed
on combustible flooring.
Summary of Contents for ClearFire CFH
Page 14: ...Chapter 1 Introduction 1 8 Part No 750 295 ...
Page 27: ...Chapter 2 Installation Part No 750 295 2 13 Figure 2 10 CFH wiring diagram typical 10 60 HP ...
Page 42: ...Chapter 3 Flue and Combustion Air Venting 3 14 Part No 750 295 ...
Page 90: ......
Page 92: ...Chapter 6 Model CFH Parts 6 2 Part No 750 295 6 1 CONTROL PANEL 10 60 HP ...
Page 93: ...Chapter 6 Model CFH Parts Part No 750 295 6 3 6 1 CONTROL PANEL 70 80 HP ...
Page 100: ...Chapter 6 Model CFH Parts 6 10 Part No 750 295 Standard gas train 30 HP ...
Page 105: ...Chapter 6 Model CFH Parts Part No 750 295 6 15 6 4 2 Gas Train Dual Fuel 30 HP dual fuel ...
Page 106: ...Chapter 6 Model CFH Parts 6 16 Part No 750 295 40 HP dual fuel ...
Page 107: ...Chapter 6 Model CFH Parts Part No 750 295 6 17 50 60 HP dual fuel ...
Page 110: ...Chapter 6 Model CFH Parts 6 20 Part No 750 295 40 HP dual fuel lgp ...
Page 111: ...Chapter 6 Model CFH Parts Part No 750 295 6 21 50 60 HP dual fuel lgp ...
Page 112: ...Chapter 6 Model CFH Parts 6 22 Part No 750 295 6 4 4 Gas Train Propane 30 HP propane ...
Page 113: ...Chapter 6 Model CFH Parts Part No 750 295 6 23 40 HP propane ...
Page 114: ...Chapter 6 Model CFH Parts 6 24 Part No 750 295 50 60 HP propane ...
Page 120: ...e mail info cleaverbrooks com Web Address http www cleaverbrooks com ...