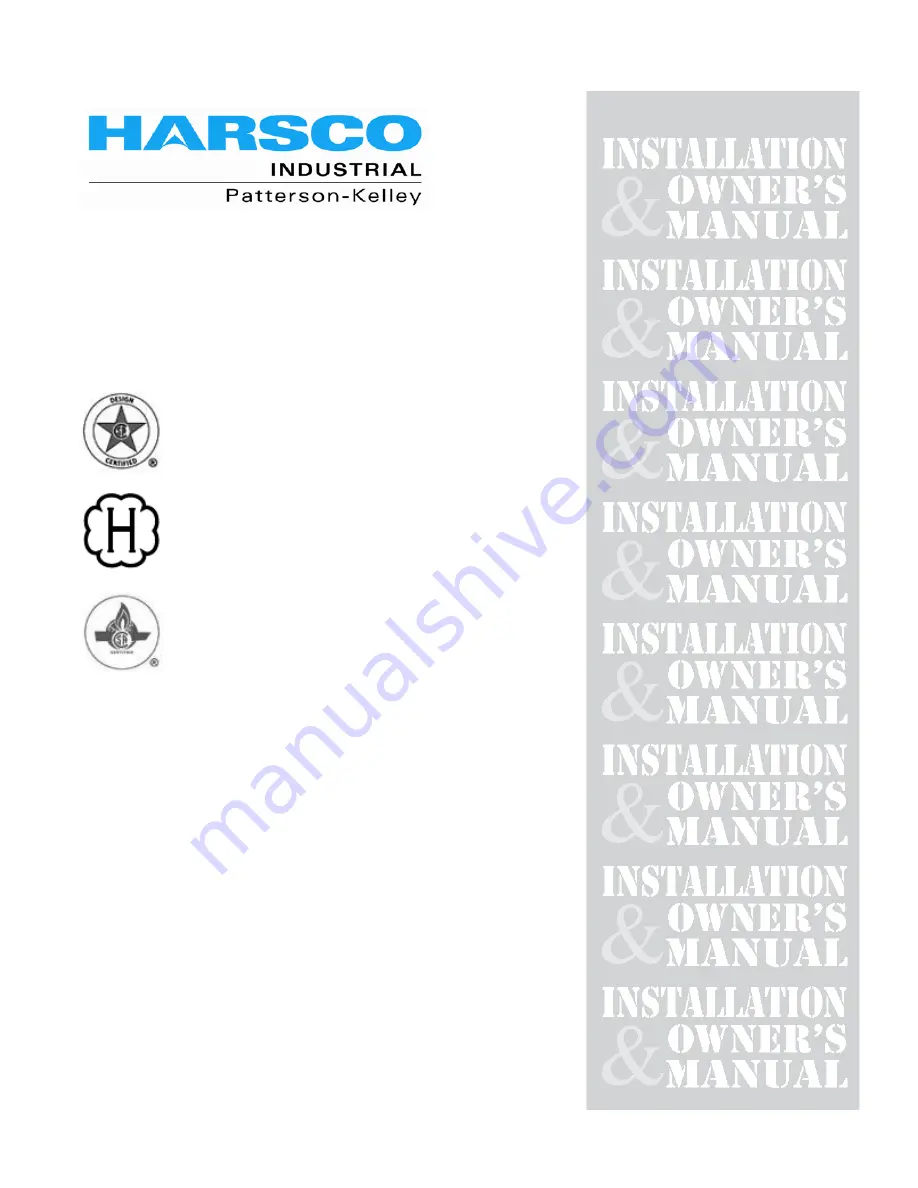
© 2010 Harsco Industrial, Patterson-Kelley
Printed: 7/1/2013
MACH
®
GAS-FIRED BOILER
C750-C900-C1050
Model #:_______
Serial #______________________
Start-Up Date:
_______________________
Harsco Industrial, Patterson-Kelley
100 Burson Street,
East Stroudsburg, PA 18301
Telephone: (570) 476-7261
Facsimile: (570) 476-7247
www.harscopk.com
MACH
®
C750-C900-C1050
Rev. 1.05 (07/01/2013)
C.S.A. Design-Certified
Complies with ANSI Z21.13/CSA 4.9
Gas-Fired Low Pressure Steam and Hot Water
Boilers
ASME Code, Section IV
Certified by Harsco Industrial, Patterson-Kelley
C.S.A. Design-Certified
Complies with ANSI Z21.13/CSA 4.9
Gas-Fired Low Pressure Steam and Hot Water
Boilers
1004905947