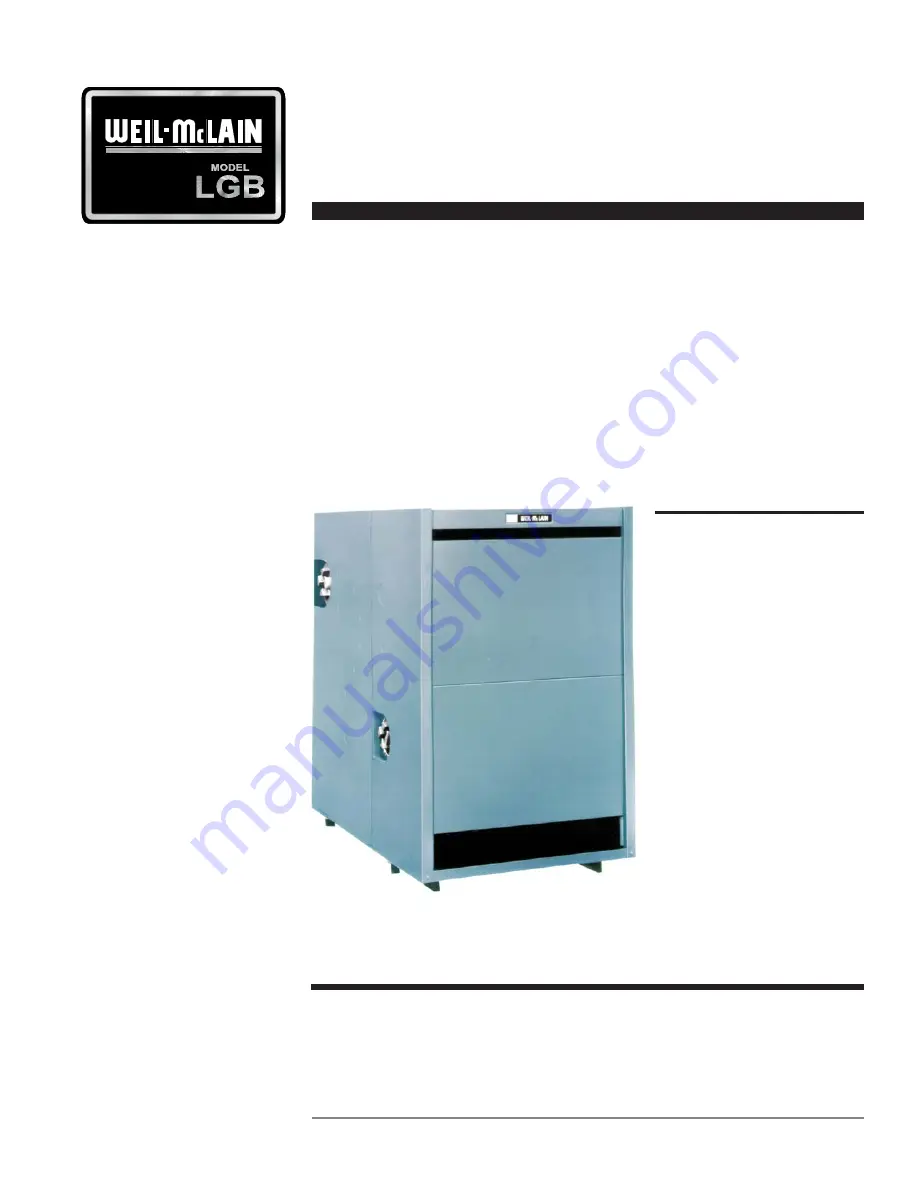
LG
LG
LG
LG
LGB
B
B
B
B
Read all instructions before installing
Installer
Leave all instructions with boiler for future reference.
Any claims for damage or shortage in shipment must be filed
immediately against the transportation company by the consignee.
Owner
Installation and service should be performed by qualified contractor.
Refer to
Control Supplement
for additional information
Gas–Fired Boiler
Boiler Manual
• Installation
• Start-up
• Maintenance
• Parts
Part No. 550-141-186/0703