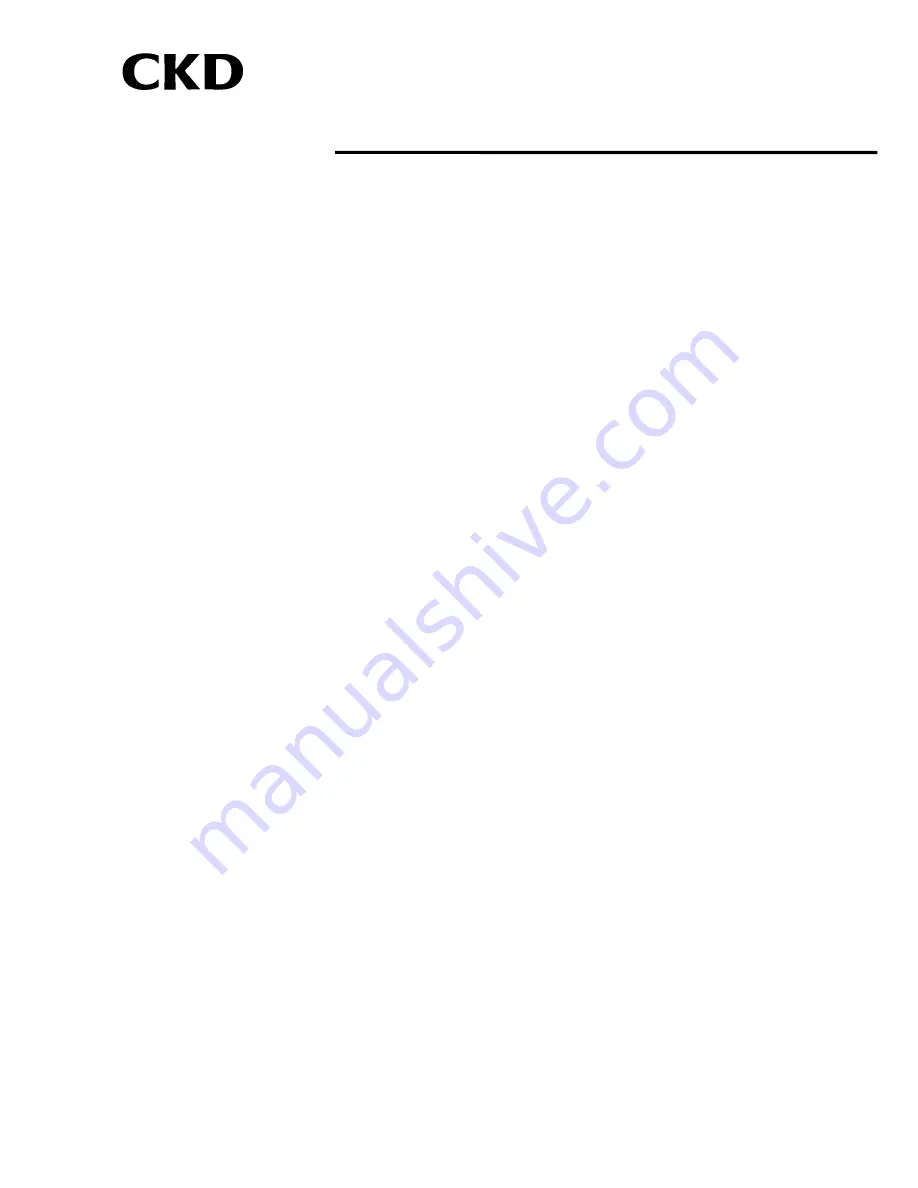
SM−431049-A
INSTRUCTION MANUAL
ELECTRIC ACTUATOR
ESSD Series (Rod Type)
ELCR Series (Table Type)
●
Be sure to read this Instruction Manual thoroughly
before operating the product.
●
In particular, make sure to carefully read and
understand all descriptions related to safety.
●
Keep this Instruction Manual in a safe and
convenient place where it can be quickly taken
out and read whenever necessary.
CKD Corporation
Edition № 4
Summary of Contents for ELCR Series
Page 56: ...MEMO...