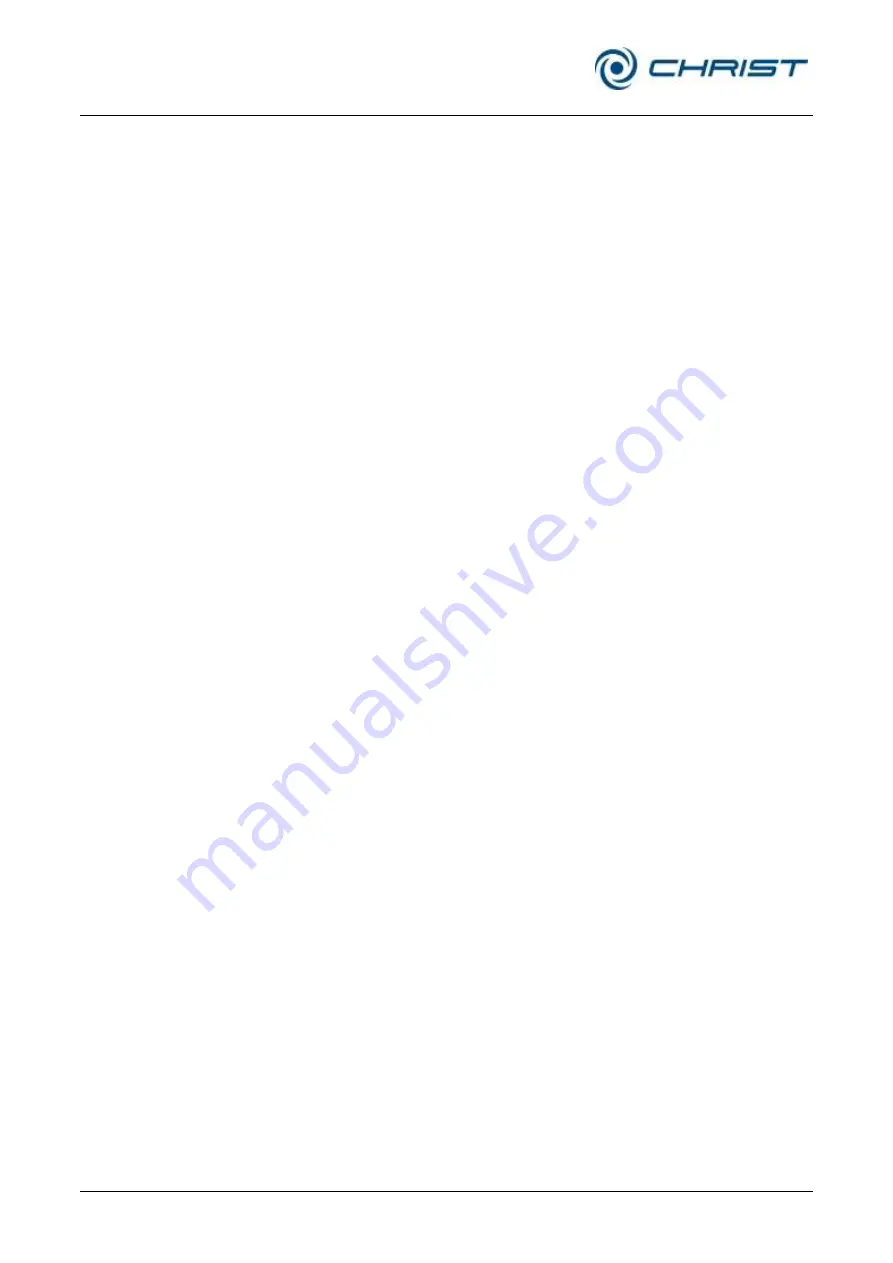
Rotational Vacuum Concentrator RVC 2-18 CDplus
HCl resistant version
Table of contents
6 / 84
Version 04/2012, Rev. 2.3 of 03/07/2017
• sb
Translation of the original operating manual
BASIC: Withdrawal of the vapours by a vacuum pump .............................................. 29
STANDARD: Condensation of the vapours in a glass cooling trap ............................. 30
PROFESSIONAL: Condensation of the vapours in a cooling trap
PROFESSIONAL TWIN: Condensation of the vapours in a cooling trap
Changing the set values for the manual mode ................................................... 45