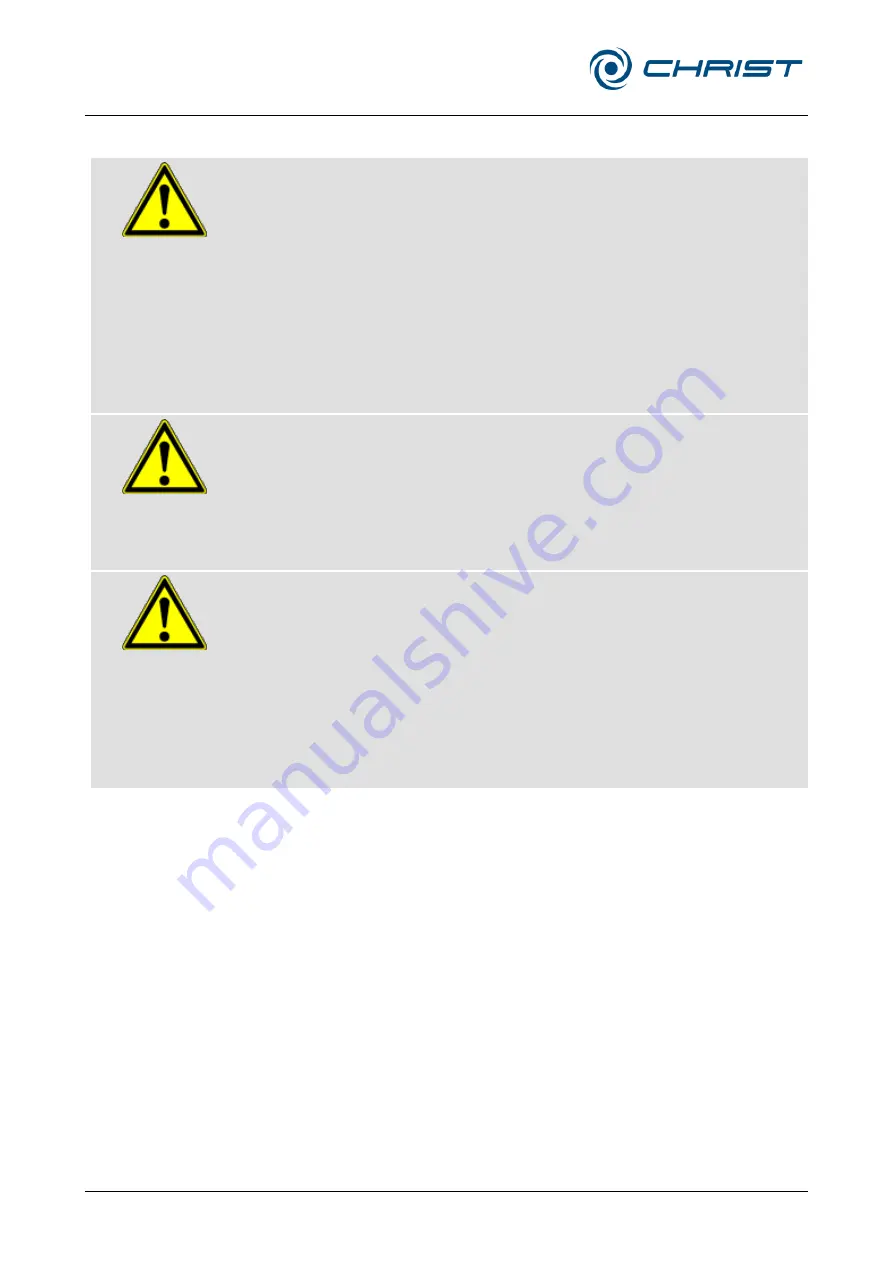
Freeze-dryer Epsilon 2-10D LSCplus
8 Maintenance and service
126 / 161
Version 07/2022, Rev. 3.0 of 20/07/2022
• sb
Translation of the original operating manual
8.1.9
Refrigeration system
DANGER
Risk of suffocation caused by the refrigerant
When work is performed on the refrigeration system of the freeze-dryer,
refrigerant may escape in the liquid or gas state and under high pressure.
Gaseous refrigerant is heavier than air and high concentration levels of it
may collect on the floor or in pits.
There is a risk of suffocation in the case of high concentration levels.
Possible symptoms are paralysis and unconsciousness. Affected persons
do not notice the fact that they suffocate.
• Only qualified persons are authorised to perform work on the
refrigeration system of the freeze-dryer!
• Ensure good aeration/extraction when working on the refrigeration
system!
WARNING
Risk of cold burns or frostbite caused by the refrigerant
When work is performed on the refrigeration system of the freeze-dryer,
refrigerant may escape in the liquid or gas state and under high pressure.
In the case of skin contact with liquid refrigerant, cold burns or frostbite
may result.
• Only qualified persons are authorised to perform work on the
refrigeration system of the freeze-dryer!
DANGER
Risk of explosion due to refrigerants
The natural refrigerants used are highly flammable and can form an
explosive mixture if their concentration in the ambient air is sufficiently
high.
There is an explosion hazard.
• Work on the refrigeration system of the freeze-dryer must only be
carried out by qualified specialist personnel who have been trained to
handle flammable refrigerants!
• Ensure good ventilation and make sure that no ignition sources (e.g.
soldering iron, welding equipment) are present!
The refrigerant circuit is a closed system. Only certified and qualified
persons are authorised to perform work on the refrigeration system!
8.1.10 Heat transfer medium system
The filling level of the heat transfer medium for the temperature control of
the shelves can be checked via the sight glass (position see chapter 2.1.1 -
"Functional and operating elements"). This check is performed only once
per month. Even in the case of several years of use, the heat transfer
medium usually does not need to be topped up.
The circulation pump for the heat transfer medium is maintenance-free.