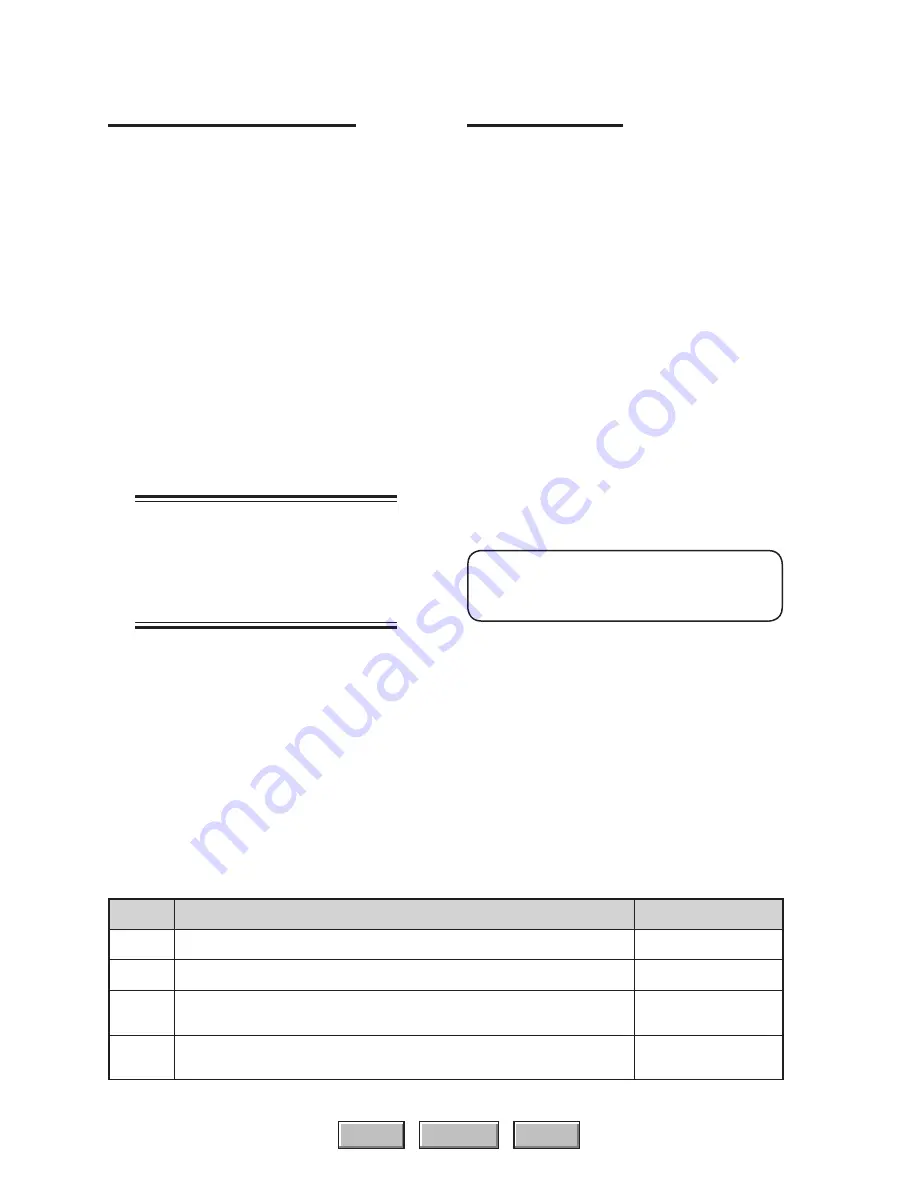
3024-024e
Edge Maxx
C-8
Make Programming Changes
To change the FPM setting, press the +
or – buttons to increase or decrease the
speed.
Press the CURSOR button to move to the
flatwork Item description.
Press the + or – buttons to cycle through
the pre-programmed flatwork descrip-
tions.
To enable the Gap Buster function, press
the CHI SELECT button so that it is lit.
The display changes to show CHI=1.
To handle fitted sheets or odd items, press
the BYPASS ON/OFF button to that it is
lit. The display changes to show BYP=1.
NOTE:
Either of these options
can be changed “on the fly” by
simply pressing the appropriate
CHI Panel button while a program
is running.
1.
2.
3.
3.
4.
End Programming
When finished changing program settings,
follow these steps to save or discard changes.
Saving Changes
Press the ENTER button to save.
As appropriate:
Press the CD button to leave program-
ming mode.
OR
Press another STATION button to
choose another program.
Canceling Changes
Press the CD button
without
pressing EN-
TER. The following messages displays:
ENTER TO SAVE
MINUS TO QUIT
Press the – button. The program number
being worked on re-displays with all
changes removed.
As appropriate:
Press the CD button to leave program-
ming mode.
OR
Press another STATION button to
choose another program.
1.
2.
•
•
1.
2.
3.
•
•
Setting
Function
Range
FPM
Conveyor Speed.
028 - 180
Item
Flatwork product description.
18 pre-programmed
CHI
Turns the Gap Buster Function on or off
0 - OFF
1 - ON
BYP
When on, automatically opens the lower spreader belts to accommodate fitted
sheets or odd items.
0 - Not open
1 - Open
TOC
INDEX
C-TOC
Summary of Contents for Edge MAXX
Page 1: ...EDGE MAXX Dual Input Large Piece Spreader Feeder INSTRUCTION MANUAL...
Page 12: ......
Page 102: ......
Page 132: ......
Page 196: ......
Page 228: ...3038 010k Edge Maxx PL 14 This page intentionally left blank TOC INDEX PL TOC...
Page 232: ...3038 010k Edge Maxx PL 18 This page intentionally left blank TOC INDEX PL TOC...
Page 250: ......
Page 252: ...SC 2 460V Motor Circuit TOC INDEX SC TOC...
Page 255: ...Edge Maxx 3210 393d SC 5 This page intentionally left blank TOC INDEX SC TOC...
Page 259: ...Edge Maxx 3210 393d SC 9 This page purposely left blank TOC INDEX SC TOC...
Page 273: ......
Page 274: ......
Page 275: ......
Page 276: ......
Page 278: ......
Page 280: ......