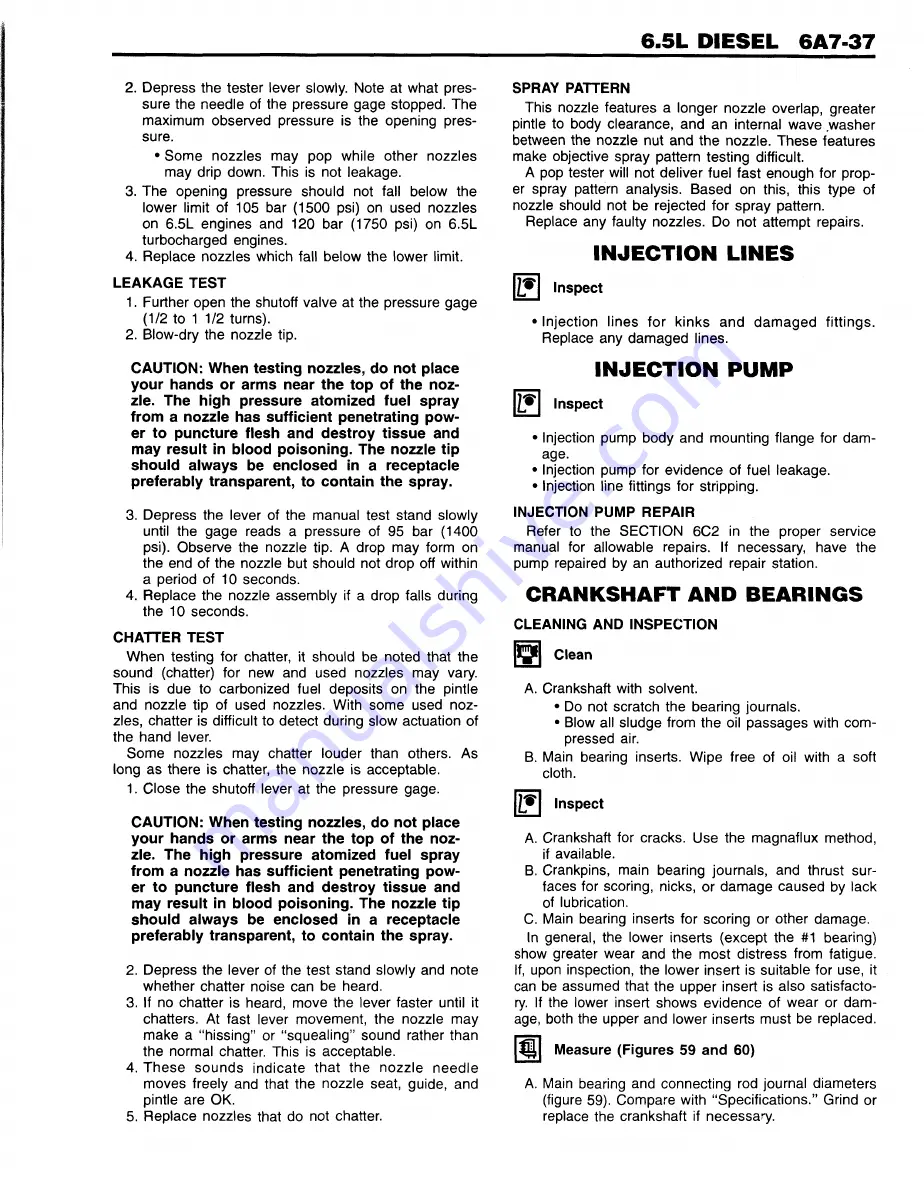
2. Depress the tester lever slowly. Note at what pres
sure the needle of the pressure gage stopped. The
maximum observed pressure is the opening pres
sure.
• Some nozzles may pop while other nozzles
may drip down. This is not leakage.
3. The opening pressure should not fall below the
lower limit of 105 bar (1500 psi) on used nozzles
on 6.5L engines and 120 bar (1750 psi) on 6.5L
turbocharged engines.
4. Replace nozzles which fall below the lower limit.
LEAKAGE TEST
1. Further open the shutoff valve at the pressure gage
(1/2 to 1 1/2 turns).
2. Blow-dry the nozzle tip.
CAUTION: When testing nozzles, do not place
your hands or arms near the top of the noz
zle. The high pressure atomized fuel spray
from a nozzle has sufficient penetrating pow
er to puncture flesh and destroy tissue and
may result in blood poisoning. The nozzle tip
should always be enclosed in a receptacle
preferably transparent, to contain the spray.
3. Depress the lever of the manual test stand slowly
until the gage reads a pressure of 95 bar (1400
psi). Observe the nozzle tip. A drop may form on
the end of the nozzle but should not drop off within
a period of 10 seconds.
4. Replace the nozzle assembly if a drop falls during
the 10 seconds.
CHATTER TEST
When testing for chatter, it should be noted that the
sound (chatter) for new and used nozzles may vary.
This is due to carbonized fuel deposits on the pintle
and nozzle tip of used nozzles. With some used noz
zles, chatter is difficult to detect during slow actuation of
the hand lever.
Some nozzles may chatter louder than others. As
long as there is chatter, the nozzle is acceptable.
1. Close the shutoff lever at the pressure gage.
CAUTION: When testing nozzles, do not place
your hands or arms near the top of the noz
zle. The high pressure atomized fuel spray
from a nozzle has sufficient penetrating pow
er to puncture flesh and destroy tissue and
may result in blood poisoning. The nozzle tip
should always be enclosed in a receptacle
preferably transparent, to contain the spray.
2. Depress the lever of the test stand slowly and note
whether chatter noise can be heard.
3. If no chatter is heard, move the lever faster until it
chatters. At fast lever movement, the nozzle may
make a “ hissing” or “squealing” sound rather than
the normal chatter. This is acceptable.
4. These sounds indicate that the nozzle needle
moves freely and that the nozzle seat, guide, and
pintle are OK.
5. Replace nozzles that do not chatter.
SPRAY PATTERN
This nozzle features a longer nozzle overlap, greater
pintle to body clearance, and an internal wave washer
between the nozzle nut and the nozzle. These features
make objective spray pattern testing difficult.
A pop tester will not deliver fuel fast enough for prop
er spray pattern analysis. Based on this, this type of
nozzle should not be rejected for spray pattern.
Replace any faulty nozzles. Do not attempt repairs.
IN JE C TIO N LIN ES
L1
I9
Inspect
Injection lines for kinks and damaged fittings.
Replace any damaged lines.
IN JE C TIO N PUM P
Inspect
• Injection pump body and mounting flange for dam
age.
• Injection pump for evidence of fuel leakage.
• Injection line fittings for stripping.
INJECTION PUMP REPAIR
Refer to the SECTION 6C2 in the proper service
manual for allowable repairs. If necessary, have the
pump repaired by an authorized repair station.
CRANKSHAFT AND BEARINGS
CLEANING AND INSPECTION
Clean
|mj|
A. Crankshaft with solvent.
• Do not scratch the bearing journals.
• Blow all sludge from the oil passages with com
pressed air.
B. Main bearing inserts. Wipe free of oil with a soft
cloth.
17
Inspect
A. Crankshaft for cracks. Use the magnaflux method,
if available.
B. Crankpins, main bearing journals, and thrust sur
faces for scoring, nicks, or damage caused by lack
of lubrication.
C. Main bearing inserts for scoring or other damage.
In general, the lower inserts (except the #1 bearing)
show greater wear and the most distress from fatigue.
If, upon inspection, the lower insert is suitable for use, it
can be assumed that the upper insert is also satisfacto
ry. If the lower insert shows evidence of wear or dam
age, both the upper and lower inserts must be replaced.
Measure (Figures 59 and 60)
A. Main bearing and connecting rod journal diameters
(figure 59). Compare with “ Specifications.” Grind or
replace the crankshaft if necessary.
Summary of Contents for Light Duty Truck 1994 Series
Page 1: ......
Page 11: ...VIEW A p n n n j VIEW C F7554 Figure 10 Hydra Matic 4L60 E Transmission I D Location ...
Page 24: ...NOTES ...
Page 26: ... ...
Page 69: ...NOTES ...
Page 71: ...3 2 STEERING ...
Page 73: ......
Page 84: ......
Page 102: ...40 ...
Page 130: ...NOTES ...
Page 146: ...NOTES ...
Page 162: ...NOTES ...
Page 166: ...Figure 5 Removing the Pinion Flange Figure 6 Pressing the Drive Pinion from the Cage ...
Page 178: ...Figure 3 Spreading the Differential Case Figure 4 Removing the Differential ...
Page 190: ...NOTES ...
Page 202: ...NOTES ...
Page 206: ...F5785 ...
Page 212: ...B Button Moved Out of Bearing Bore F5791 ...
Page 228: ...NOTES ...
Page 232: ......
Page 234: ......
Page 236: ...Adjuster 63 Bolt 64 Lock Figure 10 Turning the Adjuster Plug K3 Models ...
Page 237: ...Figure 13 Removing the Pinion Seal 39 Bearing Cup Figure 16 Removing the Inner Bearing Cap ...
Page 261: ...F7475 ...
Page 267: ...B Button Moved Out of Bearing Bore F5791 ...
Page 294: ...NOTES ...
Page 300: ...NOTES ...
Page 318: ...NOTES ...
Page 322: ...SR207LN2 EDS ...
Page 324: ......
Page 326: ...OVERHEAD OILING AND RETURN MAIN OIL GALLERY N30005 6A2 J EDS ...
Page 368: ...103 153 127 V1200 ...
Page 370: ......
Page 372: ......
Page 374: ...F9375 Figure 7 Engine Lubrication Diagram Engines Without Balance Shaft ...
Page 376: ...Figure 9 Engine Lubrication Diagram Engines With Balance Shaft ...
Page 399: ...V2974 ...
Page 410: ......
Page 412: ...195 196 201 174 252 163 165 164 244 3706r3924 ...
Page 452: ......
Page 454: ...163 164 V1202 ...
Page 456: ...20 21x 302 210 4 0 41 2 5 2 5 1 2 51 4 2 e3 54 3 9 252 252 S 255 255 25 6 256 209 V1196 ...
Page 458: ...100 1 8 4 185 183 177 v 75 201 3706r1204 ...
Page 460: ......
Page 510: ......
Page 512: ...V2131 ...
Page 514: ...110 106 106 103 90 93 89 88 87 86 v 7 7 7 7 j A _ 111 f t 2 a a s 53 49 L 47 46 3706r4751 ...
Page 566: ...NOTES ...
Page 574: ...NOTES ...
Page 618: ...SPECIAL TOOLS ...
Page 620: ...NOTES ...
Page 672: ......
Page 682: ......
Page 686: ......
Page 694: ...RH0213 4L60 E ...
Page 695: ...657 659 m i J 8092 H J 34196 4 3 34196 5 657 658 665 J 23907 J 7004 1 J 8092 RH0214 4L60 E ...
Page 696: ...J 8092 J 34196 4 33 31 J 8092 RH0215 4L60 E ...
Page 697: ...SPECIAL TOOLS ...
Page 698: ...SPECIAL TOOLS ...
Page 758: ...RH0194 4L80 E ...
Page 764: ......
Page 770: ...SPECIAL TOOLS ...
Page 771: ...SPECIAL TOOLS CONT ...
Page 772: ......
Page 775: ......
Page 776: ......
Page 785: ......
Page 804: ...NOTES ...
Page 806: ......
Page 808: ......
Page 822: ...3707r5079 ...
Page 840: ......
Page 848: ...NOTES ...
Page 852: ......
Page 860: ...F5435 ...
Page 866: ......
Page 878: ...F9167 ...
Page 882: ...16 FrontOutputShaft 18 DrivtQNr 19 DrivenGm t 20 DriveChain 22 FrontOutputBearing V2836 ...
Page 890: ...F9168 ...
Page 908: ......
Page 919: ......