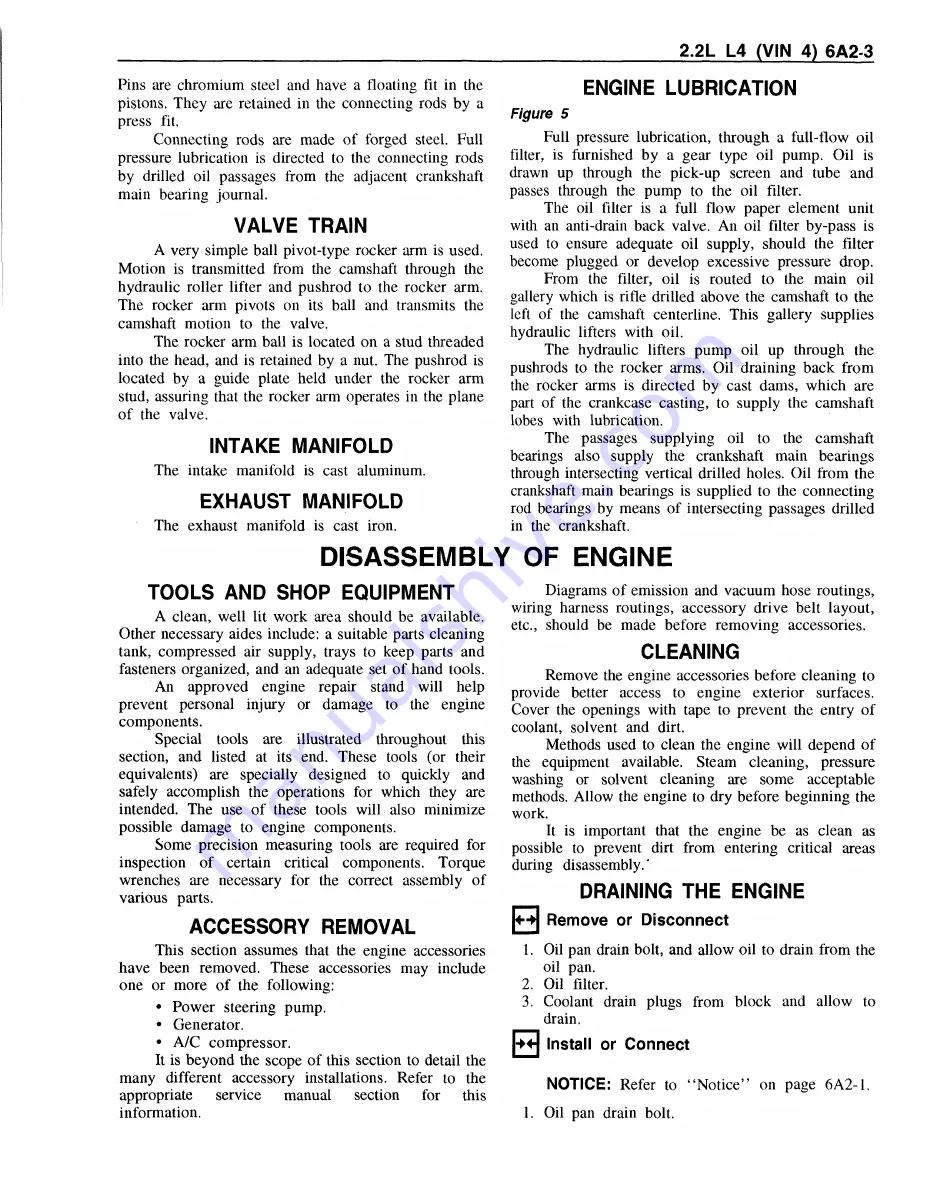
Pins are chromium steel and have a floating fit in the
pistons. They are retained in the connecting rods by a
press fit.
Connecting rods are made of forged steel. Full
pressure lubrication is directed to the connecting rods
by drilled oil passages from the adjacent crankshaft
main bearing journal.
VALVE TRAIN
A very simple ball pivot-type rocker arm is used.
Motion is transmitted from the camshaft through the
hydraulic roller lifter and pushrod to the rocker arm.
The rocker arm pivots on its ball and transmits the
camshaft motion to the valve.
The rocker arm ball is located on a stud threaded
into the head, and is retained by a nut. The pushrod is
located by a guide plate held under the rocker arm
stud, assuring that the rocker arm operates in the plane
of the valve.
INTAKE MANIFOLD
The intake manifold is cast aluminum.
EXHAUST MANIFOLD
The exhaust manifold is cast iron.
ENGINE LUBRICATION
Figure 5
Full pressure lubrication, through a full-flow oil
filter, is furnished by a gear type oil pump. Oil is
drawn up through the pick-up screen and tube and
passes through the pump to the oil filter.
The oil filter is a full flow paper element unit
with an anti-drain back valve. An oil filter by-pass is
used to ensure adequate oil supply, should the filter
become plugged or develop excessive pressure drop.
From the filter, oil is routed to the main oil
gallery which is rifle drilled above the camshaft to the
left of the camshaft centerline. This gallery supplies
hydraulic lifters with oil.
The hydraulic lifters pump oil up through the
pushrods to the rocker arms. Oil draining back from
the rocker arms is directed by cast dams, which are
part of the crankcase casting, to supply the camshaft
lobes with lubrication.
The passages supplying oil to the camshaft
bearings also supply the crankshaft main bearings
through intersecting vertical drilled holes. Oil from the
crankshaft main bearings is supplied to the connecting
rod bearings by means of intersecting passages drilled
in the crankshaft.
DISASSEMBLY OF ENGINE
TOOLS AND SHOP EQUIPMENT
A clean, well lit work area should be available.
Other necessary aides include: a suitable parts cleaning
tank, compressed air supply, trays to keep parts and
fasteners organized, and an adequate set of hand tools.
An approved engine repair stand will help
prevent personal injury or damage to the engine
components.
Special tools are illustrated throughout this
section, and listed at its end. These tools (or their
equivalents) are specially designed to quickly and
safely accomplish the operations for which they are
intended. The use of these tools will also minimize
possible damage to engine components.
Some precision measuring tools are required for
inspection of certain critical components. Torque
wrenches are necessary for the correct assembly of
various parts.
ACCESSORY REMOVAL
This section assumes that the engine accessories
have been removed. These accessories may include
one or more of the following:
• Power steering pump.
• Generator.
• A/C compressor.
It is beyond the scope of this section to detail the
many different accessory installations. Refer to the
appropriate
service
manual
section
for
this
information.
Diagrams of emission and vacuum hose routings,
wiring harness routings, accessory drive belt layout,
etc., should be made before removing accessories.
CLEANING
Remove the engine accessories before cleaning to
provide better access to engine exterior surfaces.
Cover the openings with tape to prevent the entry of
coolant, solvent and dirt.
Methods used to clean the engine will depend of
the equipment available. Steam cleaning, pressure
washing or solvent cleaning are some acceptable
methods. Allow the engine to dry before beginning the
work.
It is important that the engine be as clean as
possible to prevent dirt from entering critical areas
during disassembly.'
DRAINING THE ENGINE
[»->[ Remove or Disconnect
1. Oil pan drain bolt, and allow oil to drain from the
oil pan.
2. Oil filter.
3. Coolant drain plugs from block and allow to
drain.
Install or Connect
NOTICE:
Refer to “ Notice” on page 6A2-1.
1. Oil pan drain bolt.
Summary of Contents for Light Duty Truck 1994 Series
Page 1: ......
Page 11: ...VIEW A p n n n j VIEW C F7554 Figure 10 Hydra Matic 4L60 E Transmission I D Location ...
Page 24: ...NOTES ...
Page 26: ... ...
Page 69: ...NOTES ...
Page 71: ...3 2 STEERING ...
Page 73: ......
Page 84: ......
Page 102: ...40 ...
Page 130: ...NOTES ...
Page 146: ...NOTES ...
Page 162: ...NOTES ...
Page 166: ...Figure 5 Removing the Pinion Flange Figure 6 Pressing the Drive Pinion from the Cage ...
Page 178: ...Figure 3 Spreading the Differential Case Figure 4 Removing the Differential ...
Page 190: ...NOTES ...
Page 202: ...NOTES ...
Page 206: ...F5785 ...
Page 212: ...B Button Moved Out of Bearing Bore F5791 ...
Page 228: ...NOTES ...
Page 232: ......
Page 234: ......
Page 236: ...Adjuster 63 Bolt 64 Lock Figure 10 Turning the Adjuster Plug K3 Models ...
Page 237: ...Figure 13 Removing the Pinion Seal 39 Bearing Cup Figure 16 Removing the Inner Bearing Cap ...
Page 261: ...F7475 ...
Page 267: ...B Button Moved Out of Bearing Bore F5791 ...
Page 294: ...NOTES ...
Page 300: ...NOTES ...
Page 318: ...NOTES ...
Page 322: ...SR207LN2 EDS ...
Page 324: ......
Page 326: ...OVERHEAD OILING AND RETURN MAIN OIL GALLERY N30005 6A2 J EDS ...
Page 368: ...103 153 127 V1200 ...
Page 370: ......
Page 372: ......
Page 374: ...F9375 Figure 7 Engine Lubrication Diagram Engines Without Balance Shaft ...
Page 376: ...Figure 9 Engine Lubrication Diagram Engines With Balance Shaft ...
Page 399: ...V2974 ...
Page 410: ......
Page 412: ...195 196 201 174 252 163 165 164 244 3706r3924 ...
Page 452: ......
Page 454: ...163 164 V1202 ...
Page 456: ...20 21x 302 210 4 0 41 2 5 2 5 1 2 51 4 2 e3 54 3 9 252 252 S 255 255 25 6 256 209 V1196 ...
Page 458: ...100 1 8 4 185 183 177 v 75 201 3706r1204 ...
Page 460: ......
Page 510: ......
Page 512: ...V2131 ...
Page 514: ...110 106 106 103 90 93 89 88 87 86 v 7 7 7 7 j A _ 111 f t 2 a a s 53 49 L 47 46 3706r4751 ...
Page 566: ...NOTES ...
Page 574: ...NOTES ...
Page 618: ...SPECIAL TOOLS ...
Page 620: ...NOTES ...
Page 672: ......
Page 682: ......
Page 686: ......
Page 694: ...RH0213 4L60 E ...
Page 695: ...657 659 m i J 8092 H J 34196 4 3 34196 5 657 658 665 J 23907 J 7004 1 J 8092 RH0214 4L60 E ...
Page 696: ...J 8092 J 34196 4 33 31 J 8092 RH0215 4L60 E ...
Page 697: ...SPECIAL TOOLS ...
Page 698: ...SPECIAL TOOLS ...
Page 758: ...RH0194 4L80 E ...
Page 764: ......
Page 770: ...SPECIAL TOOLS ...
Page 771: ...SPECIAL TOOLS CONT ...
Page 772: ......
Page 775: ......
Page 776: ......
Page 785: ......
Page 804: ...NOTES ...
Page 806: ......
Page 808: ......
Page 822: ...3707r5079 ...
Page 840: ......
Page 848: ...NOTES ...
Page 852: ......
Page 860: ...F5435 ...
Page 866: ......
Page 878: ...F9167 ...
Page 882: ...16 FrontOutputShaft 18 DrivtQNr 19 DrivenGm t 20 DriveChain 22 FrontOutputBearing V2836 ...
Page 890: ...F9168 ...
Page 908: ......
Page 919: ......