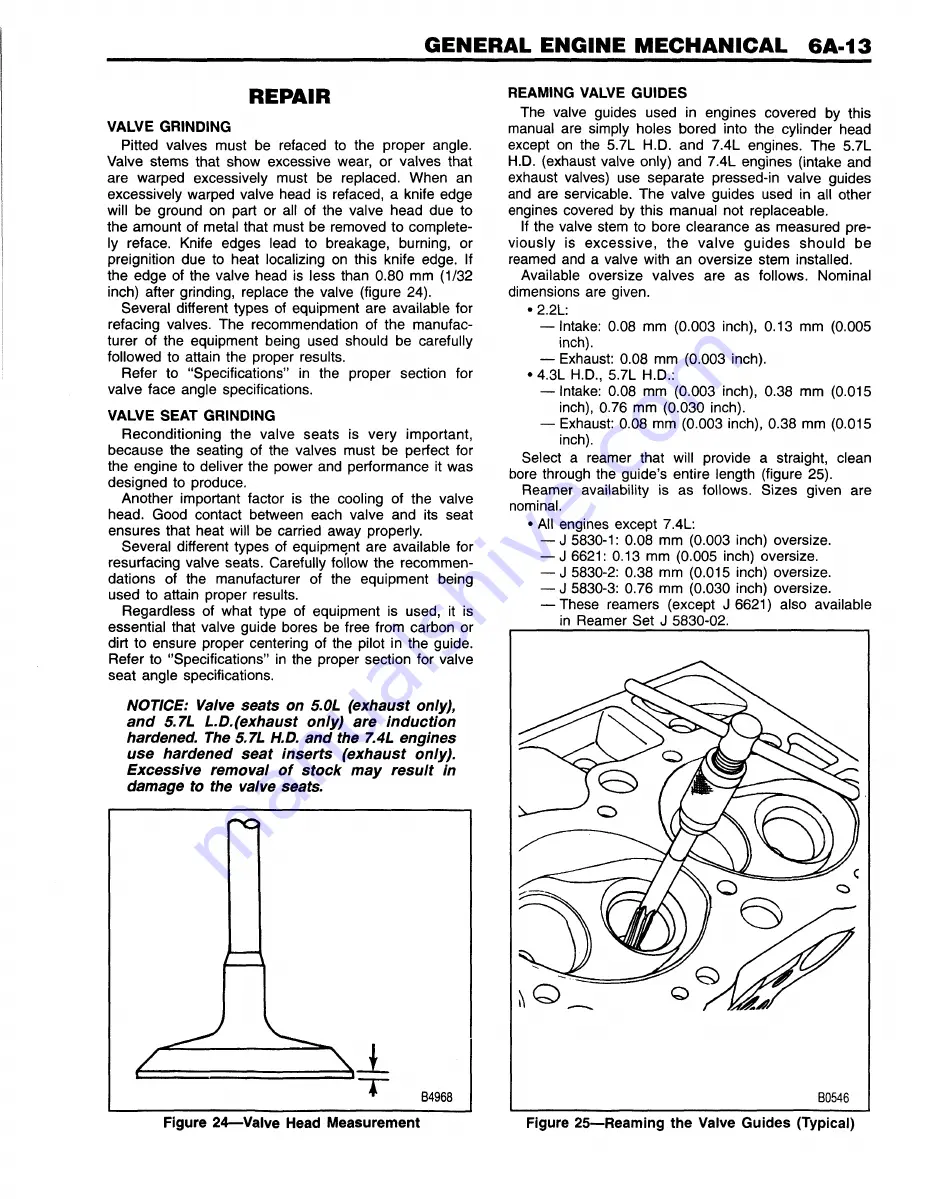
REPAIR
VALVE GRINDING
Pitted valves must be refaced to the proper angle.
Valve stems that show excessive wear, or valves that
are warped excessively must be replaced. When an
excessively warped valve head is refaced, a knife edge
will be ground on part or all of the valve head due to
the amount of metal that must be removed to complete
ly reface. Knife edges lead to breakage, burning, or
preignition due to heat localizing on this knife edge. If
the edge of the valve head is less than 0.80 mm (1/32
inch) after grinding, replace the valve (figure 24).
Several different types of equipment are available for
refacing valves. The recommendation of the manufac
turer of the equipment being used should be carefully
followed to attain the proper results.
Refer to “ Specifications” in the proper section for
valve face angle specifications.
VALVE SEAT GRINDING
Reconditioning the valve seats is very important,
because the seating of the valves must be perfect for
the engine to deliver the power and performance it was
designed to produce.
Another important factor is the cooling of the valve
head. Good contact between each valve and its seat
ensures that heat will be carried away properly.
Several different types of equipment are available for
resurfacing valve seats. Carefully follow the recommen
dations of the manufacturer of the equipment being
used to attain proper results.
Regardless of what type of equipment is used, it is
essential that valve guide bores be free from carbon or
dirt to ensure proper centering of the pilot in the guide.
Refer to "Specifications” in the proper section for valve
seat angle specifications.
NOTICE: Valve seats on 5.0L (exhaust only),
and 5.7L L.D.(exhaust only) are induction
hardened. The 5.7L H.D. and the 7.4L engines
use hardened seat inserts (exhaust only).
Excessive removal of stock may result in
damage to the valve seats.
REAMING VALVE GUIDES
The valve guides used in engines covered by this
manual are simply holes bored into the cylinder head
except on the 5.7L H.D. and 7.4L engines. The 5.7L
H.D. (exhaust valve only) and 7.4L engines (intake and
exhaust valves) use separate pressed-in valve guides
and are servicable. The valve guides used in all other
engines covered by this manual not replaceable.
If the valve stem to bore clearance as measured pre
viously is excessive, the valve guides should be
reamed and a valve with an oversize stem installed.
Available oversize valves are as follows. Nominal
dimensions are given.
• 2.2L:
— Intake: 0.08 mm (0.003 inch), 0.13 mm (0.005
inch).
— Exhaust: 0.08 mm (0.003 inch).
• 4.3L H.D., 5.7L H.D.:
— Intake: 0.08 mm (0.003 inch), 0.38 mm (0.015
inch), 0.76 mm (0.030 inch).
— Exhaust: 0.08 mm (0.003 inch), 0.38 mm (0.015
inch).
Select a reamer that will provide a straight, clean
bore through the guide’s entire length (figure 25).
Reamer availability is as follows. Sizes given are
nominal.
• All engines except 7.4L:
— J 5830-1: 0.08 mm (0.003 inch) oversize.
— J 6621: 0.13 mm (0.005 inch) oversize.
— J 5830-2: 0.38 mm (0.015 inch) oversize.
— J 5830-3: 0.76 mm (0.030 inch) oversize.
— These reamers (except J 6621) also available
in Reamer Set J 5830-02.
Summary of Contents for Light Duty Truck 1994 Series
Page 1: ......
Page 11: ...VIEW A p n n n j VIEW C F7554 Figure 10 Hydra Matic 4L60 E Transmission I D Location ...
Page 24: ...NOTES ...
Page 26: ... ...
Page 69: ...NOTES ...
Page 71: ...3 2 STEERING ...
Page 73: ......
Page 84: ......
Page 102: ...40 ...
Page 130: ...NOTES ...
Page 146: ...NOTES ...
Page 162: ...NOTES ...
Page 166: ...Figure 5 Removing the Pinion Flange Figure 6 Pressing the Drive Pinion from the Cage ...
Page 178: ...Figure 3 Spreading the Differential Case Figure 4 Removing the Differential ...
Page 190: ...NOTES ...
Page 202: ...NOTES ...
Page 206: ...F5785 ...
Page 212: ...B Button Moved Out of Bearing Bore F5791 ...
Page 228: ...NOTES ...
Page 232: ......
Page 234: ......
Page 236: ...Adjuster 63 Bolt 64 Lock Figure 10 Turning the Adjuster Plug K3 Models ...
Page 237: ...Figure 13 Removing the Pinion Seal 39 Bearing Cup Figure 16 Removing the Inner Bearing Cap ...
Page 261: ...F7475 ...
Page 267: ...B Button Moved Out of Bearing Bore F5791 ...
Page 294: ...NOTES ...
Page 300: ...NOTES ...
Page 318: ...NOTES ...
Page 322: ...SR207LN2 EDS ...
Page 324: ......
Page 326: ...OVERHEAD OILING AND RETURN MAIN OIL GALLERY N30005 6A2 J EDS ...
Page 368: ...103 153 127 V1200 ...
Page 370: ......
Page 372: ......
Page 374: ...F9375 Figure 7 Engine Lubrication Diagram Engines Without Balance Shaft ...
Page 376: ...Figure 9 Engine Lubrication Diagram Engines With Balance Shaft ...
Page 399: ...V2974 ...
Page 410: ......
Page 412: ...195 196 201 174 252 163 165 164 244 3706r3924 ...
Page 452: ......
Page 454: ...163 164 V1202 ...
Page 456: ...20 21x 302 210 4 0 41 2 5 2 5 1 2 51 4 2 e3 54 3 9 252 252 S 255 255 25 6 256 209 V1196 ...
Page 458: ...100 1 8 4 185 183 177 v 75 201 3706r1204 ...
Page 460: ......
Page 510: ......
Page 512: ...V2131 ...
Page 514: ...110 106 106 103 90 93 89 88 87 86 v 7 7 7 7 j A _ 111 f t 2 a a s 53 49 L 47 46 3706r4751 ...
Page 566: ...NOTES ...
Page 574: ...NOTES ...
Page 618: ...SPECIAL TOOLS ...
Page 620: ...NOTES ...
Page 672: ......
Page 682: ......
Page 686: ......
Page 694: ...RH0213 4L60 E ...
Page 695: ...657 659 m i J 8092 H J 34196 4 3 34196 5 657 658 665 J 23907 J 7004 1 J 8092 RH0214 4L60 E ...
Page 696: ...J 8092 J 34196 4 33 31 J 8092 RH0215 4L60 E ...
Page 697: ...SPECIAL TOOLS ...
Page 698: ...SPECIAL TOOLS ...
Page 758: ...RH0194 4L80 E ...
Page 764: ......
Page 770: ...SPECIAL TOOLS ...
Page 771: ...SPECIAL TOOLS CONT ...
Page 772: ......
Page 775: ......
Page 776: ......
Page 785: ......
Page 804: ...NOTES ...
Page 806: ......
Page 808: ......
Page 822: ...3707r5079 ...
Page 840: ......
Page 848: ...NOTES ...
Page 852: ......
Page 860: ...F5435 ...
Page 866: ......
Page 878: ...F9167 ...
Page 882: ...16 FrontOutputShaft 18 DrivtQNr 19 DrivenGm t 20 DriveChain 22 FrontOutputBearing V2836 ...
Page 890: ...F9168 ...
Page 908: ......
Page 919: ......