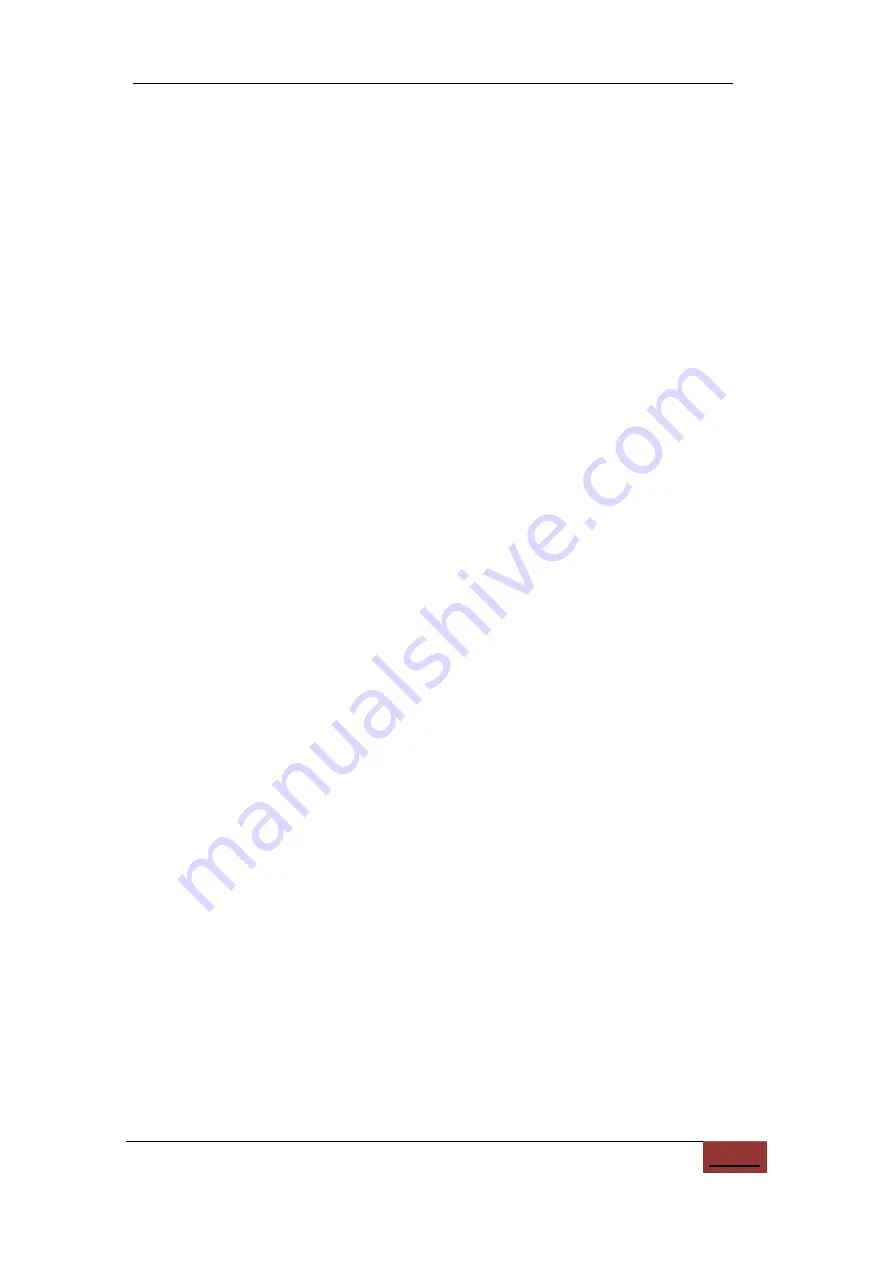
45
19.
Work Flow
(1)
Create CSV file:
Export CSV (pick-and-place) file by your PCB design software.
Units must be mm. (13.1);
(2)
Start Machine:
Turn on the power switch on right side. (9);
(3)
Run SmtMain:
Double click on icon to start control program. (9);
(4)
Check origin (optional):
When starting, the stage sets its origin using limit
switches. To check for drifts, image the PCB origin with the down camera by
selecting “Diagnostics / DownCamera\Nozzle to PCB origin”. (11);
(5)
PCB:
Place PCB against left stop in PCB clamp area. (18)
;
(6)
Import CSV file:
Import CSV data and convert to a work file. (13.2);
(7)
Edit work file:
Choose “Run / Edit”. (10.1). When done, save. Typical inputs:
a)
Feeder tab:
Define the feeder parameters. (10.1.2);
i.
Note or edit the
“feeder” number to match the parts;
ii.
Edit feeder
parameters for proper “feeder advance” and “pick angle”;
iii.
Place tapes and parts in corresponding feeders. (16);
iv.
Perform a needle pull to calibrate position of tape in feeders and check pick
location, using
“Run / Edit / Feeder tab / Edit / Calibrate” (10.1.2.1);
b)
PCB tab:
Define calibration locations on the PCB;
i.
Calibrate with 2- or 3-points in
“set systems parameters”. (12.1);
ii.
Define the calibration points in “PCB calibration”. (10.1.5);
iii.
Calibrate position of PCB. Do in
“Run / Edit” to save calibration. (10.1.5);
(8)
Nozzles:
Choose and install nozzles in head. (17);
(9)
Run work file:
Choose “Run / Load”. (10.2);
a)
Step by step:
Choose “step++” to check if working normally. (10.2);
b)
Component check (optional):
Look at first component with
“Run / Edit /
component tab / edit / calibrate
” (10.1.1.2) and check if aligned well. To offset rest
of components, measure offset and use
“set / component place offset”. (12);
c)
Run:
Components placed continuously.
Click “Stop” if machine alarms or parts
fed or placed improperly. (10.2);