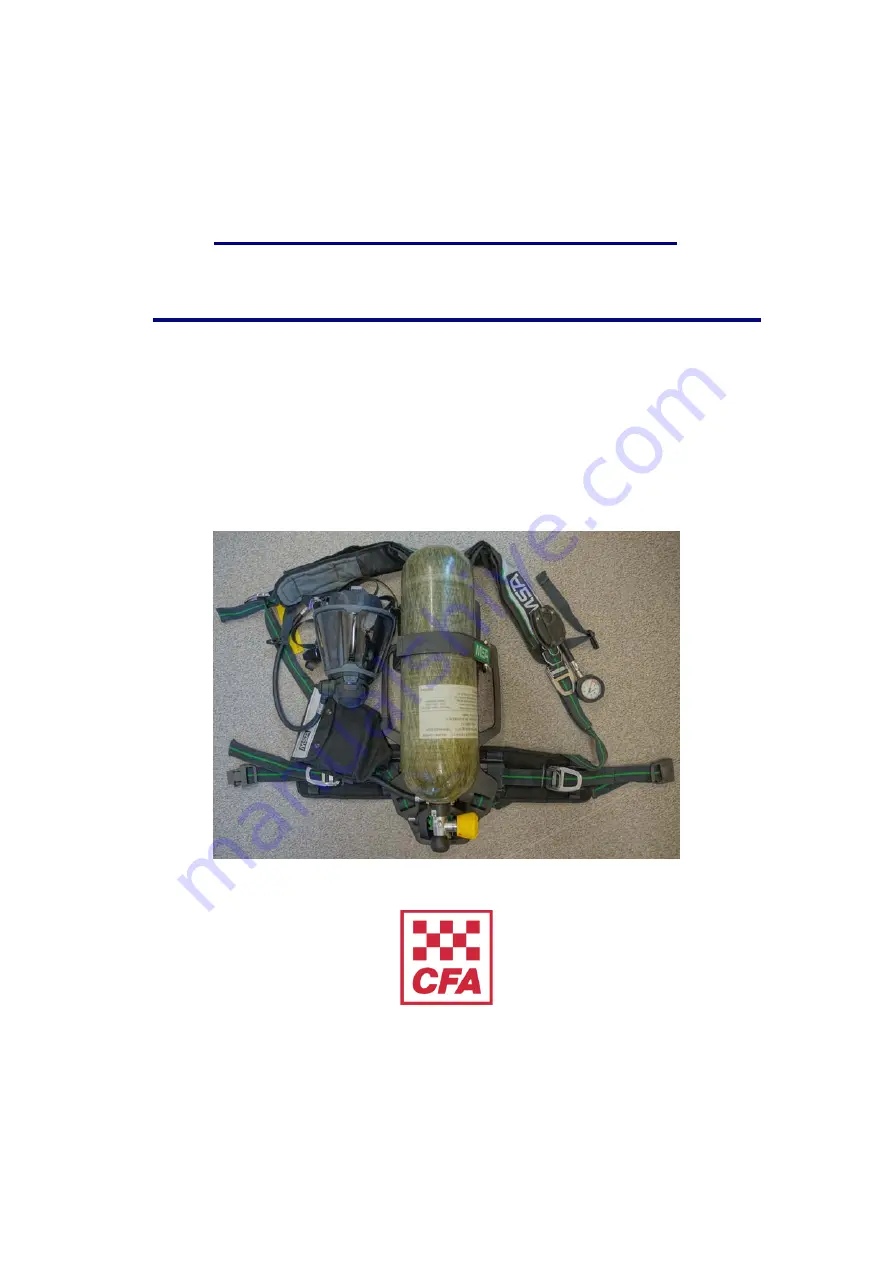
MSA G1 Classic
Breathing Apparatus
Reference Manual
This manual is published for use within CFA in conjunction with participation in a
course of instruction.
It has been developed having regard to current CFA occupational health and safety
guidelines and “Safety First” principles.
Edition 1
December 2019