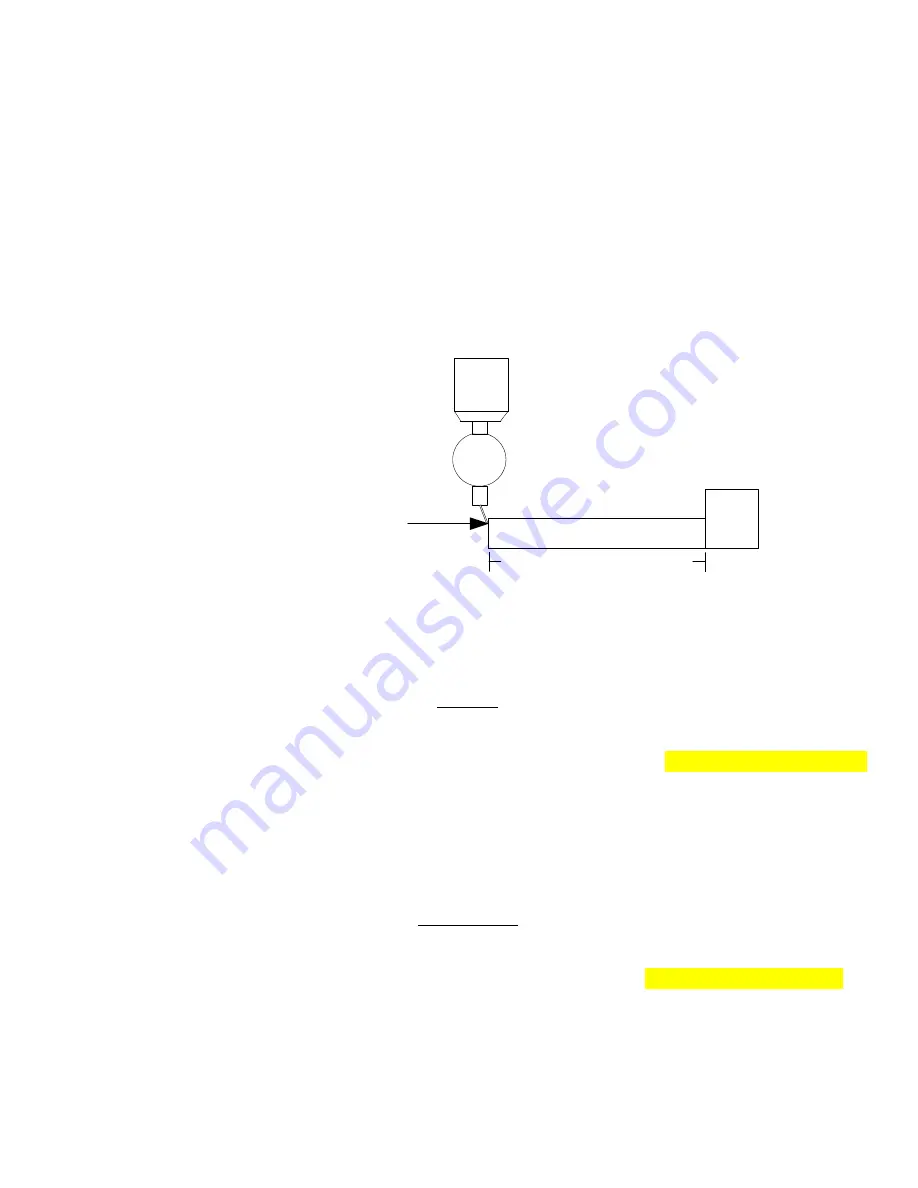
Appendix B: Troubleshooting Motion and Encoder Issues
Symptom or Error
Axis does not move
2. Have you configured your motor revs/unit (imperial) or units/rev
correct distance
(metric) correctly? (continued)
5.
Fine tuning:
Making sure they are parallel/perpendicular with the table, butt a place a gauge block
or anything else that can be measured accurately up against a 123 block - a 6”
(150mm) parallel works nicely as shown below:
Imperial - How to compute motor revs/inch:
Commanded distance / Distance moved = multiplier
Multiplier * Current revs/inch = corrected revs/inch
Ex: Commanded Distance = 6.0000” = ~.999417 (multiplier) * current revs/inch
Distance moved = 6.0035”
(multiplier) .999417 * (current revs/inch) 5.0000 = 4.997085
←
New motor revs/inch
Metric - How to compute motor mm's/rev:
Commanded distance / Distance moved = multiplier
Multiplier * Current revs/inch = corrected revs/inch
Ex: Distance moved = 150.021mm
= 1.00014 (multiplier) * current mm's/rev
Commanded Distance= 150mm
(multiplier) 1.00014 * (current mm's/rev) 5.0000 = 5.0007
←
New motor mm's/rev
Perform this procedure 1 or 2 more times (being sure to reset your part zero after any
change in the ratios). You should be able to accurately position to within a .0001
(.00254mm).
Spindle
Set X0, Y0, Z0
1. Jog in slowly from 1
direction to take up lash
Block measured 6” (150mm)
2. Zero indicator and axes
3. MDI Z to .5” (12mm) to clear
4. MDI command X 6” (150mm)
5. Read indicator to measure
distance traveled
6. Compute and enter new
motor revs/inch or
mm/rev